как сделать щепорез своими руками по чертежу? Выбор древесной дробилки для производства арболитовой щепы
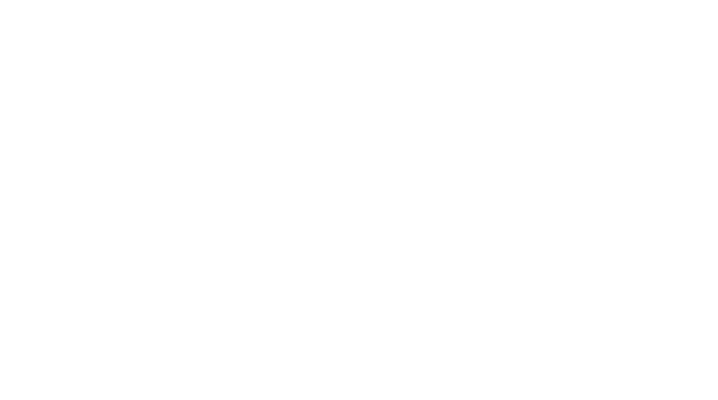
Арболит как строительный материал был запатентован еще в первой половине XX века. В нашей стране широко применяться он стал в последние годы.
Арболит или деревобетон (щепобетон) выпускается в виде блоков. Используется для возведения малоэтажных строений. Как следует из названия, в качестве наполнителя выступает древесная щепа. В ход идут отходы деревьев хвойных и лиственных пород.
Арболит относится к недорогим строительным материалам, отличающимся высокой экологичностью, малым весом блоков, отличной способностью удерживать тепло. Древесные отходы в составе смеси деревобетона составляют более трех четвертей – от 75 до 90 процентов.
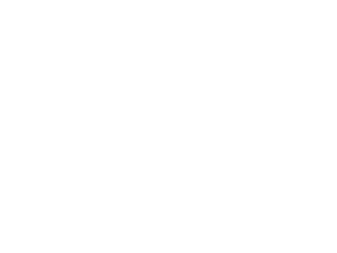
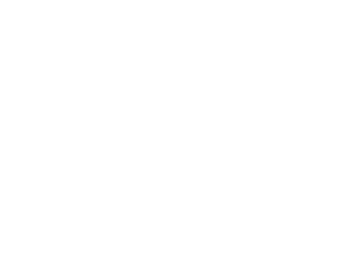
Что это такое?
Отходы деревообработки являются ценным строительным материалом. После измельчения до определенных размеров они становятся наполнителем бетонных смесей. Используется щепа для арболита или как его именуют щепобетона. Арболитовые блоки имеют массу достоинств. Доступная стоимость играет немалую роль. Кроме того, дом, построенный из арболита, практически не требует дополнительного утепления.
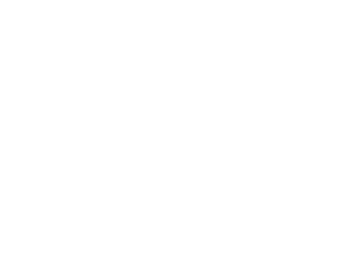

Есть у щепы и иные достоинства. Материал пригоден для использования в качестве:
- топлива для печей – в чистом виде или в виде гранул;
- декора – дизайнеры предлагают его в окрашенном и естественном виде для оформления дачных участков и даже парков;
- составляющей для изготовления и украшения мебели;
- ингредиента, используемого при копчении различных продуктов питания.
В производстве мелкие фракции идут на изготовление других стройматериалов: картона, гипсокартона, ДСП и ДВП.
Из чего делают?
При выборе древесины для арболита нужно знать ее состав. Так, лиственница не подходит для данного строительного материала из-за высокого содержания веществ, негативно влияющих на цемент. Ядом для цемента являются сахара. Кроме лиственницы, они в большом количестве имеются в древесине бука. Следовательно, отходы этого дерева использовать тоже нельзя.
Очень важный момент – срок рубки леса. Щепу нельзя делать сразу после вырубки. Материал должен вылежаться в течение трех – четырех месяцев.
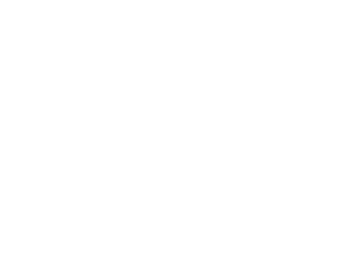

Практически все отходы могут стать исходниками для изготовления щепы.
- ветки и сучки;
- верхушки деревьев;
- горбыль;
- остатки и обломки;
- вторичные отходы.
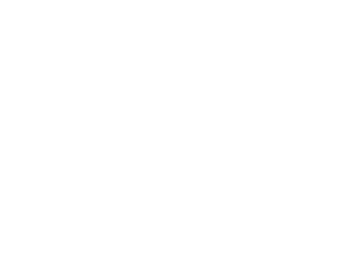
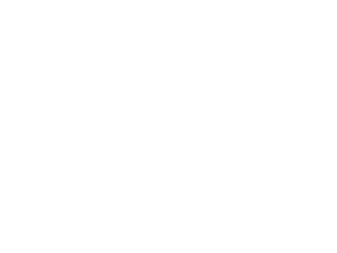
Допускается наличие в общей массе древесины для производства щепы хвои и листьев – не более 5%, а коры – не более 10%.
Наиболее часто щепу изготавливают из елей и сосен. Выбор в пользу хвои неслучаен. Дело в том, что любая древесина содержит в себе такие вещества, как крахмал, сахара и прочие вещества, способные существенно повлиять на снижение качества арболита. В процессе производства приходится выводить вредные составляющие. Поскольку в хвое их меньше, именно на эти породы приходится меньше усилий, времени и материальных затрат на подготовку щепы.
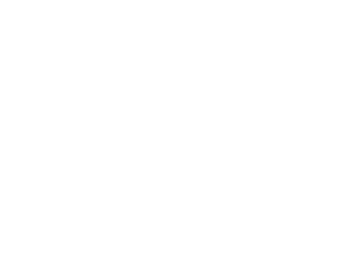
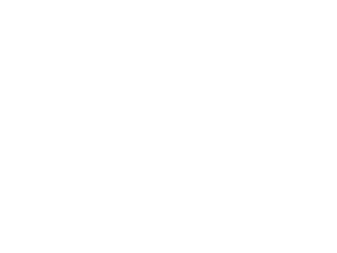
Какой должна быть щепа?
Древесный наполнитель для арболита имеет свой ГОСТ. На уровне государственного стандарта для щепы установлены жесткие требования.
Выделены три основных параметра:
- длина не больше 30 мм;
- ширина не больше 10 мм;
- толщина не больше 5 мм.
Обозначены и оптимальные размеры по ширине и длине:
- длина – 20 мм;
- ширина – 5 мм.
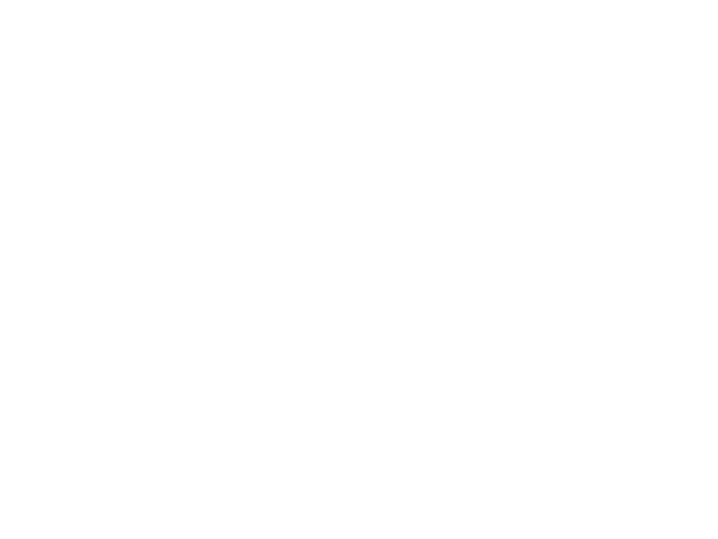
Новые требования появились с принятием ГОСТ 54854-2011. До этого существовал другой ГОСТ с меньшими требованиями. Тогда допускалось использование более длинной щепы – вплоть до 40 мм. В 2018 году «вольности» в размерах наполнителя не допускаются.
Стандарт регламентирует и наличие примесей: коры, листьев, хвои. Материал следует очищать от земли, песка, глины, а в зимнее время – от снега. Наличие плесени и загниваний недопустимо.
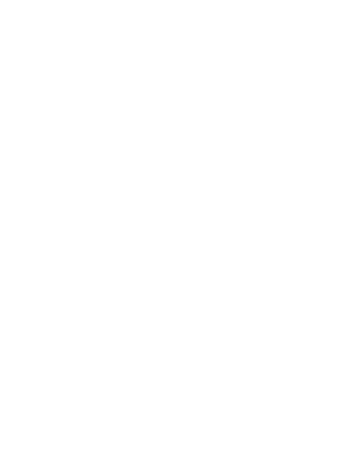
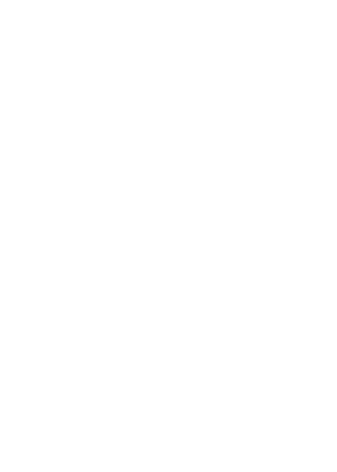
Выбор оборудования для изготовления
Наиболее подходящим оборудованием для получения щепы требуемой формы и размеров является специальный деревообрабатывающий шредер. Однако стоимость станка настолько высока, что вне производства приходится искать другие варианты.
Арболит вполне возможно изготавливать в домашних условиях. Для этого и щепу нужно делать самостоятельно. Измельчителем древесины в условиях подсобного хозяйства становится щеподробильный станок.
- Дисковые рубильные машины обрабатывают древесину различной формы. За счет регулировки наклона режущего инструмента можно получать заготовки требуемого размера.
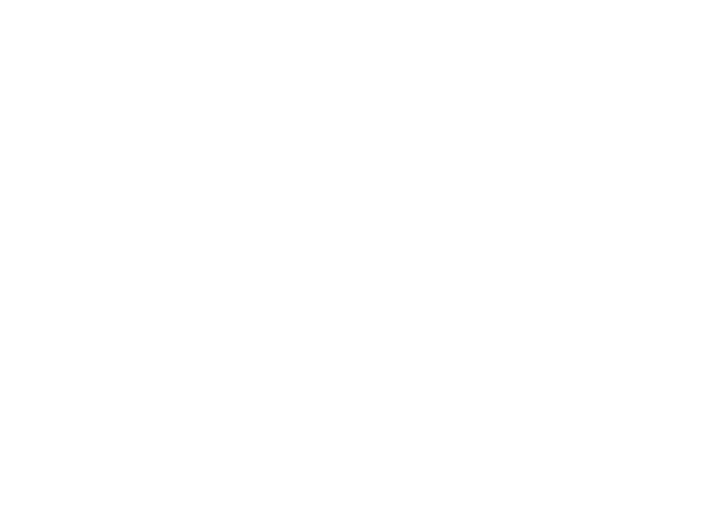
- В барабанных щепорезах измельчают всевозможные отходы: лесозаготовительные, мебельного производства, обрезков после строительства. Сырье загружают в объемный бункер, откуда оно попадает в камеру и разрезается ножами с двусторонними лезвиями.
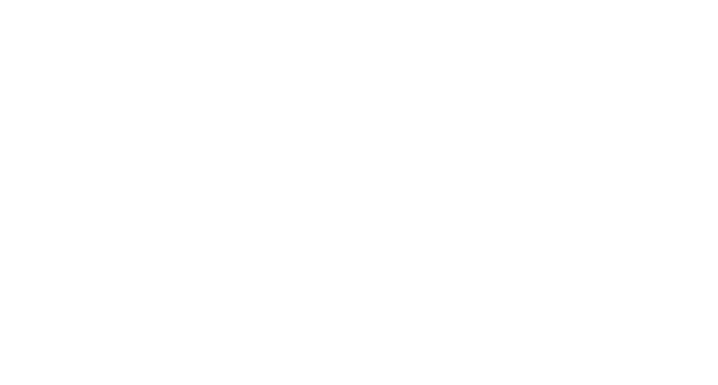
- Роторные дробилки молоткового типа выпускаются с двумя или одним валом. Основные элементы устройства – молотки и отбойники. Сначала древесина измельчается ударным способом, затем готовая продукция просеивается сквозь сито. От величины ячеек сита зависит размер получаемой щепы.
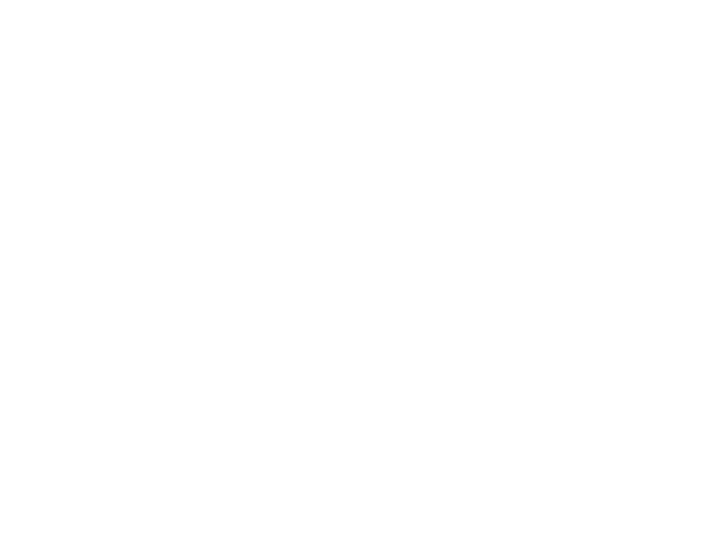
Во всех перечисленных устройствах предусмотрена только ручная загрузка материала.
Принцип производства
Принцип работы щепорезов сводится к нескольким этапам.
Сначала отходы – доски, горбыль, обрезки, сучки и другое сырье – закладываются в загрузочный бункер. Оттуда все это подается в закрытую камеру, где на валу вращается мощный диск. На плоском диске имеются прорези. На нем, кроме того, закреплены несколько ножей. Ножи движутся под углом. За счет этого обрабатываемая древесина разделяется на небольшие пластины с косым резом.
Сквозь дисковые прорези пластины проникают в барабан, где стальные пальцы производят дальнейшее измельчение. Пальцы и пластины крепятся на том же валу, что и диск. Пластины установлены очень близко к барабану. Они перемещают размолотую щепу по внутренней поверхности барабана.
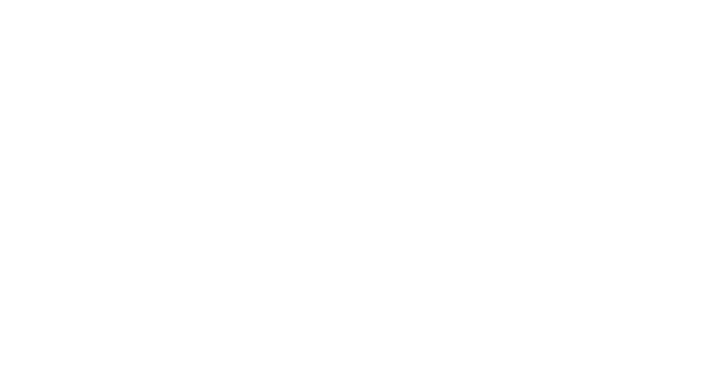
Нижняя часть барабана снабжена сеткой с ячейками, обеспечивающими заданные размеры щепы. Размер ячейки варьируется от 10 до 15 мм в диаметре. Как только готовая к использованию щепа попадает в нижнюю зону в вертикальном направлении, она проходит сквозь сетку в поддон. Оставшиеся частицы проворачиваются, удерживаемые пластинами, еще круг. В это время их положение постоянно меняется. Достигнув низа в нужном направлении, они также оказываются в поддоне.
Щепорезы могут иметь как электрический, так и бензиновый приводы. Мощность двигателя небольшого устройства находится в пределах четырех – шести киловатт, в более солидных доходит до 10-15 кВт. От мощности зависят способности устройства. С ее увеличением растет объем продукции за час работы механизма.
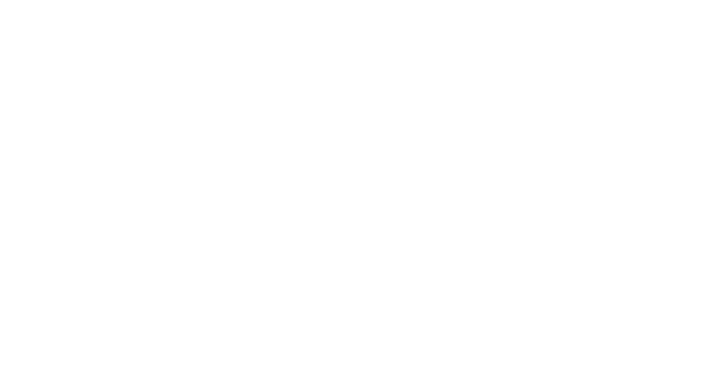
Как сделать щепорез своими руками?
Тем, кто захочет сделать собственный щепорез, потребуется чертеж устройства, материалы, определенные знания и навыки. Чертеж можно найти в интернете, к примеру, тот, что прилагается.
Узлы и детали придется делать и собирать самостоятельно.
Один из основных элементов механизма – диск диаметром порядка 350 мм и толщиной примерно 20 мм. Если ничего подходящего в хозяйстве не имеется, придется вытачивать из листа. Для посадки на вал потребуется сделать хорошо центрированное отверстие с пазом под шпонку. Кроме того, нужно будет выпилить три паза, сквозь которые древесина станет попадать под молотки, и нужное количество монтажных отверстий.
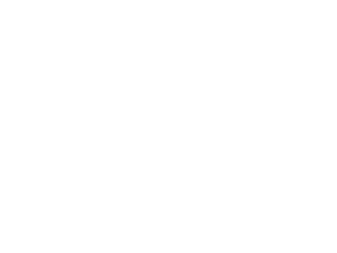
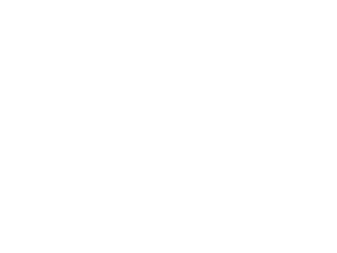
Несколько проще обстоят дела с ножами. Их делают из автомобильных рессор. На ножах просверливаются по два отверстия под крепеж. Кроме сверла, потребуется зенкер. Зенковка позволит утопить потайные головки крепежных деталей. Плотно прикрепить ножи к диску не составит труда любому взрослому мужчине.
Молотки представляют собою обычные стальные пластины, имеющие толщину около 5 мм. Крепятся они на роторе с шагом 24 мм. Купить молотки можно в магазине.
Сито для щепореза – это длинный (около 1100 мм) цилиндр (Д= 350 мм), свернутый и сваренный из листа. Примечательно, что отверстия в сите должны иметь не ровные, а рваные края. Поэтому их не высверливают, а вырубают, к примеру, пробойником с диаметром от 8 до 12 мм.
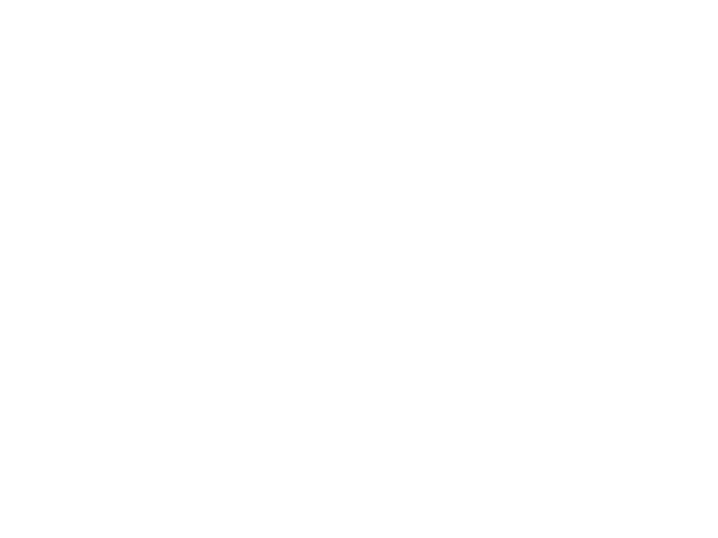
Все режущие и вращающиеся детали должны закрываться кожухом. Кожух, как и приемный бункер, изготавливают из листовой стали. Отдельные детали вырезают по картонным шаблонам и сваривают в единое целое. Для жесткости конструкции к листам приваривают ребра жесткости из труб или уголков. В корпусе следует предусмотреть все отверстия: для вала, загрузочного бункера и для выхода щепы.
Готовые детали собираются в механизм. На рабочий вал насаживается диск, молотки и подшипники. Вся конструкция закрывается кожухом. Диск ни в коем случае не должен касаться корпуса. Зазор должен составлять порядка 30 мм.
Привод монтируется на заключительном этапе. Самодельный щепорез может работать от электродвигателя напряжением 220 или 380 В. Допускается работа от бензинового или дизельного мотора.
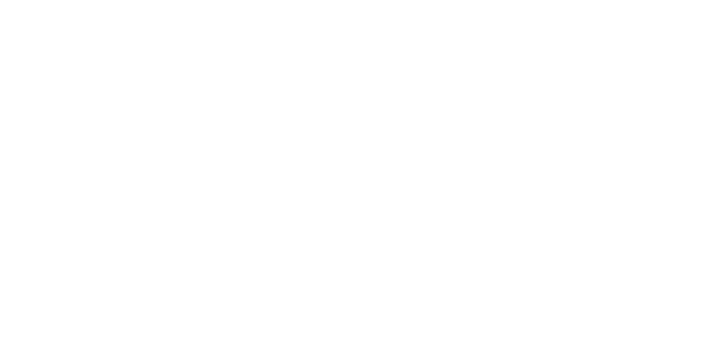
Электродвигатели обладают небольшой мощностью, зато малошумные и более экологичные. Двигатели внутреннего сгорания более производительны, но их работа сопровождается выделением вредных выхлопных газов.
Самодельные щепорезы выгодны при изготовлении арболита для частного строительства.
О том, как сделать щепорез своими руками, смотрите в следующем видео.
Щепорез для арболита своими руками: подробное описание
Производство арболита – это несколько операций, связанных с приготовлением щепы, ее подготовкой и смешиванием с цементно-песчаным раствором. Каждая операция проводится на своем оборудование, где щепорез для арболита занимает не последнее место. Устройство с одной стороны несложное, что дает возможность изготовить станок своими руками. Но с другой стороны процесс изготовления является ответственным, потому что рабочий орган вращается с достаточно большой скоростью – 1500 об/мин минимум, а значит, ко всем узлам и деталям щепореза предъявляются строгие требования по качеству.
Конструкция станка для измельчения древесины в щепу
Дробилка щепы состоит из нескольких больших узлов:
- Станина, изготовленная из уголка или профильной трубы.
- Корпус, внутри которого располагаются все вращающиеся детали. Изготавливают из листового железа толщиною 3 мм.
- Электродвигатель или двигатель внутреннего сгорания, работающий на бензине или солярке.
Касаемо движка. Чаще для станка щепореза используют электрический вариант, как самый удобный и простой в использовании. У него есть один отрицательный момент – это снижение мощности и скорости вращения, если падает напряжение в питающей сети. По всем остальным параметрам он превосходит ДВС.
Его технические характеристики, в основном это касается скорости вращения, выбираются из расчета соединения с валом рабочего органа щепореза. Если соединение будет производиться напрямую через пальчиковую муфту, то скорость электродвигателя должна быть в пределах 1500 об/мин. Если соединение производится посредству ременной передачи через шкивы, то скорость выбирается в пределах 3000 об/мин. При этом шкив с меньшим диаметром устанавливается на вал мотора, с большим диаметром (в два раза больше) на вал рабочего органа станка.
Электродвигатель закрепляется на станине самодельного оборудования в стороне от корпуса. Основное требование – расположение шкивов на одном уровне по вертикали, чтобы не было перекоса ременной передачи.
Корпус станка для изготовления щепы представляет собой скругленную форму, разделенную на две части. Нижняя – стационарная (неподвижная), верхняя – откидная на петлях. Делается это для того, чтобы была возможность проводить монтаж, осмотр и ремонт внутреннего наполнения. Сбоку корпуса устанавливается и с помощью сварки крепится воронка, через которую в станок подаются деревянные отходы.
Как собрать корпус
Из листа стали вырезается два блина диаметром 50-100 см (или более) в зависимости от производительности щепореза. В них делают посередине отверстия диаметром, чуть больше диаметра вала установки рабочего органа. В пределах 40 мм. Блины разрезаются пополам на две части.
Из того же стального листа вырезаются две полосы шириною 40-50 см и длиною, равной длине полукруга блина. Полосы сгибаются по окружности блинов и привариваются к их краям. Получается два корыта сферической формы, которые впоследствии соединяются между собой петлями. Одно из них крепят к станине сваркой или болтами. В неподвижной части делается отверстие (прорезь во всю ширину), оно располагается выше нижней точки скругления корпуса.
Узлы и детали щепореза
Внутреннее наполнение станка – это вал, установленный на шариковых подшипниках, которые сами расположены в корпусах. Оба подшипника располагаются вне корпуса агрегата. Один из них с глухой крышкой, второй – со сквозной. Через последний будет просунут вал, на который будет надет большой шкив ременной передачи.
Станина станка изготавливается так, чтобы под корпуса подшипников попадали несущие элементы рамы. Потому что основная нагрузка как раз ляжет именно на подшипники. Самостоятельно изготовить корпуса для них практически невозможно, но можно приобрести б/у изделия, главное почистить их хорошо, особенно внутренние полости.
Диск с ножами
И два главных элемента рабочего органа самодельной щеподробилки – диск с ножами и молоточки. С изготовлением диска сложностей много. Во-первых, его толщина – 20 мм минимум. Диаметр – 35-400 см (от производительности). Во-вторых, вырезать точно и подогнать его под требуемые размеры вручную не получится. Вращение даже при 1500 об/мин – это серьезные обороты. И если установленный на вал диск будет хотя бы немного несбалансированным, то вашу самодельную установку от вибрации разнесет на запчасти. Поэтому рекомендуется диск заказать в цеху, где есть токарный станок. Там же нужно сделать три осевые прорези через каждые 120° длиною в 40% от радиуса диска. Они будут выполнять функции режущих кромок. Именно в них будут попадать отходы пиломатериалов или сучки и стволы спиленного дерева.
Сами по себе прорези не смогут качественно резать древесину, поэтому их усиливают ножами с внутренней стороны. Последние изготавливают из рессор. Крепятся ножи к диску болтами через сквозные отверстия. Все это можно сделать своими руками сверлильным станком. На глаз все это подгонять сложно, поэтому лучше найти чертеж щепореза в детальной разработке, где показаны установочные размеры ножей.
Внимание! Монтажные отверстия ножей с одной стороны расширяются до размеров ширины шляпки болта. Точно также делают с отверстием на дисках с одной стороны. Причина – шляпки болта и их гайки не должны выходить своими плоскостями за пределы ножа и диска соответственно. То есть, сводится к минимуму износ ботового соединения при соприкосновении с перерабатываемой древесиной.
На вал диск «сажается» на шпонку. Толщина диска 20 мм небольшая для качественного соединения и передачи вращательного момента. Поэтому к диску с двух сторон приваривают цапфы – это небольших размеров муфты длиною по 5-6 см. Их внешний диаметр должен быть больше диаметра вала на 4-5 см. В цеху после приварки цапф к диску производят выработку шпоночной канавки.
Молоточки
Следующий узел – молоточки. Их функция – разбивать разрезанную щепу на более мелкие кусочки. Это подвижные элементы в виде маятника, устанавливаемые нижней частью на ось. Последняя устанавливается и крепится под прорезями диска, в котором для этого делаются отверстия. То есть, три прорези – три оси для молоточков. Противоположные края осей крепятся на специальную круглую крышку, которая при сборке щепореза (шипореза) для арболита приваривается к валу. Чтобы молоточки не западали друг на друга, их разделяют сегментами в виде стальных пластин, приваренных поперек диска.
Количество молоточков варьируется в пределах 4-6 штук. По сути, это прямоугольные пластины из листа толщиною 4-6 мм. Чтобы они располагались на одном расстоянии друг от друга, между ними надо проложить кусочки труб с одинаковой длиной. Внутренний диаметр трубы больше диаметра оси. Кстати, в качестве последней можно использовать стандартный болт М10 или 12.
Сито
Еще один элемент внутреннего наполнения дробилки для арболита, который выполняет функции сортировки нарезанных пиломатериалов. Это металлический цилиндр высотою чуть меньше ширины корпуса станка, диаметр меньше, чем диаметр корпуса. В нем сделаны отверстия 8-12 мм. Его задача – не пропустить из щепореза куски пиломатериалов большего размера, чем требуется для производства арболита.
Правила сборки станка
Необходимо строго выдерживать последовательность сборочных операций.
- Собирается измельчительный узел. На вал «насаживаются» диск с ножами, молоточки и подшипники внутри своих корпусов.
- На станину устанавливается нижняя стационарная часть корпуса.
- Внутрь вставляется измельчительный узел с ситом вместе, первый должен быть вставлен во второй.
- Измельчитель упирается на станину посредству подшипников, которые к раме тут же крепятся болтами.
- Сито надо прикрепить к неподвижной части корпуса винтами или болтами. Для этого к нему заранее привариваются ушки.
- На торчащий из одного подшипника конец вала насаживается большой шкив.
- Устанавливается электродвигатель, надевается на шкивы ремни.
- Приваривается или присоединяется болтами воронка к корпусу щепореза.
- Устанавливается на петли верхняя откидная часть корпуса.
Можно считать, что измельчитель древесины для арболита своими руками сделан. Остается лишь провести электромонтаж и первый пуск оборудования. Для электромотора требуется подводка трех фаз и установка подобранного под его мощность автомат. Вариантов электромонтажа два:
- собрать отдельный блок и установить с кнопкой пуска прямо на станине;
- кнопку оставить на станке, а автомат смонтировать в распределительном щитке помещения.
Первый вариант лучше, потому что дает возможность перемещать щепорез для арболита (с б/у или новым электродвигателем) в любое место, как полноценное оборудование.
Проверка работы
Если щепорез для арболита своими руками сделан по чертежам, то можно не сомневаться в его корректной работе. Закрываете корпус верхней частью, включаете электродвигатель и через воронку подаете древесину. Из выходного отверстия тут же должна начать поступать щепа требуемых размеров. Если этого не произошло, значит, где-то была совершена ошибка.
Принцип работы щепореза
- В воронку подаются деревянные отходы.
- Их на куски разрезает диск с ножами. Размеры кусочков большие для изготовления арболита.
- Их размельчают молоточки.
- Щепа необходимого размера проходит сквозь сито, выходя наружу. Остальная, больших размеров, опять размельчается молоточками.
Главный совет
Перед тем как сделать щепорез своими руками, ознакомьтесь с чертежами станка. Следуйте в точности параметрам, обозначенным на схемах, и это гарантия качества конечного результата.
из чего делают, размер, форма, подготовка
Древесная щепа для арболита является основным компонентом в составе материала (от 75% до 90% всего объема). Выбор и подготовка древесного заполнителя является важным этапом, напрямую влияющим на конструкционные и теплоизоляционные характеристики арболита.
Из чего делают щепу для арболита
Древесина для арболита подойдет практически любая. Лучшим вариантом будет использование хвойных пород (например, сосна, ель) или твердолиственных пород (например, береза, дуб, тополь, осина). Категорически нельзя использовать лиственницу, бук (из-за повышенного содержания вредных для цемента веществ — сахаров), также нельзя использовать свежесрубленную древесину, она должна полежать 3-4 месяца.
Для производства щепы в ход идут любые отходы лесозаготовок (сучья, ветки, верхушки деревьев), отходы деревообработки (горбыль, остатки оцилиндровки), вторичные отходы (деревянная мебель, паллеты и др.). Объем древесного заполнителя должен содержать не больше 10% примеси коры, не больше 5% хвои и листьев от массы сухого заполнителя.
Почему хвоя лучше? Древесина содержит вещества, которые вредно влияют на характеристики арболита, особенно на прочность: различные группы сахаров, крахмал, экстрактивные вещества. Их содержание в хвойных породах деревьев меньше, чем в твердолиственных и других породах. В любом случае заполнитель, производимый из вышеперечисленных пород, нуждается в дальнейшей подготовке и обработке. Просто на выведение сахаров из заполнителя твердолиственных пород деревьев, в отличие от хвойных, потратится немного больше усилий и компонентов.

Химический состав пород древесины
Щепа для арболита: форма и размер
Геометрию и размер щепы для приготовления арболитовой смеси определяет ГОСТ 19222 по арболиту.

Щепа для арболита
Во-первых, по ГОСТ 19222 древесная фракция должна иметь игольчатую форму для создания армирующего эффекта и увеличения прочности материала. Во вторых лучшая щепа для арболита должна соответствовать следующим требованиям:
- длина не должна превышать 30 мм (оптимальная длина 20 мм)
- ширина должна быть не больше 10 мм (лучший вариант 5 мм)
- толщина 5 мм
Станок для изготовления щепы арболита
Правильную геометрию и размер фракций заполнителя можно получить путем изготовления ее на рубительных и щеподробительных станках. Отличным вариантом получения правильной игольчатой формы и размера щепы является использование шредеров для древесины. Однако шредер для дерева очень дорогой станок. Не худший результат дадут щепорезы для арболита (молотковые дробилки). Можно также изготавливать фракции крупных размеров на роторных рубительных машинах, а затем вторично измельчать в дробилке для щепы.

Шредер для дерева
Если купить один из вышеописанных станков, то можно легко изготовить щепу для арболита своими руками. Но чаще всего древесный заполнитель оказывается проще приобрести у лесохозяйственных предприятий.
Подготовка щепы для арболита
Вредные вещества, которые содержатся в древесном заполнителе, негативно влияют на прочность арболита. Поэтому важным этапом перед изготовлением арболитовой смеси является подготовка и обработка древесного заполнителя.
Существуют следующие способы подготовки заполнителя:
Физический способ
Подразумевает обработку древесины водой, которая вымывает значительную часть водорастворимых веществ. Именно поэтому в свежесрубленном дереве находится больше водорастворимых сахаров, чем в сплавном лесе. Древесина, которая хранится под навесом, будет содержать больше водорастворимых веществ, чем древесина, пролежавшая под дождем. Большого эффекта можно добиться длительным вымачиванием щепы в бассейне, но для этого необходимы площади. Достаточно вымачивать в течение суток в обычной воде или 2-3 часа в подогретой.
Химический способ
Самый простой способ: окисление дубильных веществ кислородом воздуха. Для этого древесину выдерживают на воздухе, и желательно под солнцем.
Химические реакции, возникающие при обработке щепы химическими веществами, переводят сахара в нерастворимые и безвредные соединения, а также создают непроницаемую пленку. Для обволакивания древесных отходов непроницаемой пленкой используют карбамидоформальдегидную смолу (КС-11 или КФ-МТ-П). Для уменьшения влияния вредных для цемента сахаров перед созданием цементной смеси щепу для арболита пропитывают минерализатором (4 – 10 % раствором хлорной извести). Процесс пропитки называется минерализация.
На практике популярна обработка древесного заполнителя растворами хлористого кальция, жидкого стекла и сернокислого глинозёма для устранения влияния вредных сахаров на цемент. Хлористый кальций следует использовать только для обработки выдержанной щепы деревьев хвойных пород. При использовании жидкого стекла и сернокислого глинозема порода древесина и время ее выдержки не важны, однако при их использовании уменьшается показатель прочности арболита почти в два раза.

Хлористый кальций или хлорид кальция CaCl2
Биологический способ
Устранение древесных ядов осуществляется при помощи катализаторов, в качестве которых могут выступать бактерии. К этому способу можно отнести элементарный прогрев древесины. Он активизирует биологические процессы, которые приведут к частичному брожению и окислению водорастворимых сахаров. В процессе сушки сахара становятся нерастворимыми: остекловываются и кристаллизуются.
Комбинированный способ
Этот способ сочетает вышеописанные химические и физические способы. Однако надо признать, что комбинированный способ трудоемкий.
Известен пример комбинированного способа применяемого в Англии. Древесный заполнитель 10 минут кипятиться, после промывается в воде. Так частично удаляются водорастворимые сахара. Затем ее кипятят в 20% растворе железного купороса, для осаждения дубильных веществ.
Еще один рецепт комбинированного способа: щепу вымачивают в жидком стекле от 5 часов до 24 часов, затем ее промывают и высушивают.
В разделе ГОСТ 19222 «Определение пригодности древесного заполнителя» описана методика по которой вы можете проверить эффективность того или иного способа.
Щепорез — особенности и разновидности конструкции, изготовление своими руками
Самостоятельное изготовление строительных материалов требует наличия необходимых компонентов. В этом отношении производство арболита является одним из предпочтительных вариантов. Оно не требует использования больших мощностей, не нуждается в сложном специальном оборудовании. Блоки из арболита обладают значительными преимуществами — они легкие, хорошо удерживают тепло, прочные и вполне надежные. Проблем с поставками цемента и прочих минеральных наполнителей нет, основным вопросом является стабильная поставка древесной щепы.
Она составляет примерно 80-90% от объема всего брикета, поэтому количество и качество материала имеет важное значение. Щепу практически негде приобрести, единственным вариантом становится изготовление своими руками. Для этого необходим станок, измельчающий древесину до нужной фракции. Его можно купить или взять в аренду, но многие пользователи предпочитают сделать самодельный измельчитель. Рассмотрим этот вариант внимательнее.
Щепа для изготовления арболита
Поскольку арболит это строительный материал, технология изготовления и качество компонентов строго регламентируются ГОСТом.
Согласно требованиям, размеры щепы должны составлять:
- Длина — 40 мм.
- Ширина — 10 мм.
- Толщина — 5 мм.
В составе материала допускается небольшое количество примесей:
- Опилки — 5-10% (максимум).
- Хвоя — 5%.
Мнение эксперта
Левин Дмитрий Константинович
Форма щепы должна быть образована расщеплением вдоль волокон, а не поперечной резкой. Это обеспечивает механические качества наполнителя — прочность, способность удерживать форму, сохранность материала во время хранения в больших емкостях.
Что такое щепорез?
Щепорез (шредер, дробилка, измельчитель и т.д.) — это механическое устройство, производящее расщепление древесины на мелкие фрагменты. Существует несколько вариантов конструкции, способных производить материал разной величины фракции.
Есть установки для изготовления пеллет, которые делают щепу мелкой фракции. Более крупный материал, который делают другие конструкции, идет на производство арболита. Кроме этого, есть обычные измельчители веток и стеблей для дачи, которые используются для изготовления компоста и не калибруют щепу определенным образом.
Исходным сырьем могут быть:
- Обрезки досок.
- Обзол.
- Ветки.
- Тонкие стволы растений.
Есть универсальные конструкции, которые способны работать не только с древесиной, но и с углем, пластиком и прочими материалами.
Использование устройства
Измельчители древесины нужны в разных ситуациях.
Они используются для выполнения следующих задач:
- Переработка и утилизация обрезков растений на садовых участках;
- В промышленном и кустарном производстве;
- Изготовление сырья для производства ОСБ, арболита, пеллет и т.д.
Если садовые измельчители можно заменить ручной переработкой отходов, то производство щепы в промышленных целях возможно только с помощью щепореза той или иной конструкции. Объемы материала даже для небольшого кустарного производства весьма велики, а если планируется запускать более крупное предприятие, то и установки для производства щепы становятся практически основным производственным оборудованием. Если вести речь о производстве арболита, приходится соблюдать требования ГОСТ, что делает оборудование важнейшим звеном всего процесса.
Конструкция, принцип действия, разновидности
Щепорезы: 1-Одновалковый 2-Двухвалковый 3-Дисковый
Существует три конструкционных разновидности щепорезов:
- Одновалковый. Это дорогие и производительные машины, которые широко используются в производстве. Основным рабочим органом этого устройства является вал с установленными на нем победдитовыми резцами. Исходное сырье подается к нему при помощи специального узла — подпрессовщика. Вращаясь, вал срубает с заготовок щепу, размер которой зависит от расстояния между твердосплавными зубьями.
Для достижения максимальной производительности необходимо использовать однородное сырье. Некоторые компании перерабатывают старые, отработавшие свой ресурс, поддоны.
- Двухвалковый. Эта конструкция позволяет перерабатывать не только древесину, но и другие материалы. Универсальность и простота изготовления привели к тому, что большинстве самодельных щепорезов сделаны на основе именно этой конструкции. Рабочий орган состоит из двух валов, на которых плотно установлены фрезы. Они вращаются по направлению друг к другу и перемалывают сырье, которое подается из бункера. Качество переработки зависит от мощности двигателя и скорости вращения валов — чем быстрее, тем меньше размер щепы. Следует учитывать, что слишком медленное вращение приводит к затягиванию заготовок между зубьями и расклиниванию фрез. Поэтому режим вращения следует подбирать соответственно характеристикам перерабатываемого материала.
- Дисковые. эти установки работают на другом принципе. Рабочим органом является вращающийся диск, на боковой плоскости которого в радиальном направлении установлены продолговатые резцы. При подаче сырья на диск происходит измельчение до определенного размера, который можно регулировать изменением наклона режущих кромок относительно радиусных линий. Кроме того, возможна регулировка размера фракции увеличением числа резцов.
Мнение эксперта
Левин Дмитрий Константинович
Наиболее простыми и доступными конструкциями считаются двухвалковые и дисковые. Они часто используются домашними мастерами в качестве прототипов для самоделок.
Достоинства и недостатки
К достоинствам щепорезов следует отнести:
- Способность перерабатывать большие количества древесины и других материалов в однородный сыпучий материал стабильной фракции.
- Универсальность, возможность изменять размеры щепы.
- Разнообразие приводных механизмов — возможность установки электрических и бензиновых двигателей.
- Компактность, для установки не требуется много места.
Недостатками измельчителей:
- Необходимость подключения к сети электропитания или подачи топлива для ДВС.
- Для переработки больших объемов требуются мощные двигатели и прочные режущие поверхности.
- Конструкция станка постоянно испытывает серьезные нагрузки и требует частого обслуживания.
Мнение эксперта
Левин Дмитрий Константинович
Дополнительным и важным недостатком щепорезов следует считать высокую цену. Самые дешевые модели стоят около 50-60 тыс. руб, а более производительные модели обойдутся куда дороже. Это является основной причиной предпочтения самостоятельного создания измельчителей.
Вас может заинтересовать: Дровокол своими руками. Виды устройств и инструкции
Возможно ли изготовление приспособления своими руками?
Самостоятельное изготовление щепореза вполне возможно, но для этого необходимо обладать соответствующими навыками и возможностями. Понадобятся инструменты, материалы, соответствующие приспособления. Кроме этого, для вращения вала придется использовать электродвигатель с натяжным устройством, или бензиновый мотор.
Щепорезы на бензиновых (или дизельных) двигателях изготавливаются реже, так как безопасный вывод выхлопных газов представляет собой небезопасную систему. Установка на улице возможна только в теплое время года, а зимой работать с подобным оборудованием крайне сложно.
Прежде, чем приступить к непосредственному изготовлению станка, надо определиться с конструкцией и подобрать все необходимые инструменты и материалы. Возможно, некоторые узлы придется заказывать у токаря или применить готовые элементы. Обычно исходят из имеющихся под рукой деталей. Кроме того, надо тщательно взвесить свои возможности и решить, сесть ли смысл браться за изготовление мощного и довольно опасного станка.
Дисковый щепорез.
Варианты конструкции самодельных щепорезов
Обычно для изготовления своими руками используются два варианта конструкции:
- Двухвалковый щепорез. Пользователей привлекает простота создания режущего инструмента — используются дисковые пилы или фрезы по дереву. установленные на двух параллельных вращающихся валах. Передать на них вращение несложно, найти необходимое количество фрез также не составляет существенных проблем Остается лишь изготовить станину и сварить кожух станка.
- Дисковый тип. Здесь используются ножи от электрорубанка, установленные на вращающемся диске. Сам рабочий орган требует хорошей балансировки, иначе от сильной вибрации станок быстро выйдет из строя. Обычно диск заказывают у токаря, а самостоятельно только монтируют ножи и изготавливают защитный кожух с подающим и выбрасывающим диффузорами.
Оба вида станков изготавливаются с помощью различных инструментов:
- Болгарка с отрезным диском.
- Сварочный инвертор с набором электродов.
- Сверлильный станок.
- Набор гаечных ключей.
- Набор обычного слесарного инструмента (молоток, пассатижи, отвертки и т.п.).
Мнение эксперта
Левин Дмитрий Константинович
В процессе работы могут понадобиться и другие инструменты, доступные пользователю. Окончательный выбор определяет конструкция, выбранная за основу будущего станка.
Все работы ведутся поэтапно:
- Изготовление станины из швеллера или мощного уголка.
- Установка ступиц рабочего органа и проверка работоспособности вала (или валов).
- Установка приводных шкивов и натяжного механизма, настройка правильности хода при натяжке приводных ремней.
- Нарезка листов металла для изготовления корпуса. Они крепятся к станине на резьбовые соединения.
- Изготовление и присоединение диффузоров подачи и выброса щепы.
Этапы изготовления указаны условно, во время сборки возможны дополнительные операции.
Наиболее популярные производители и модели
Перед тем, как приступить к созданию собственного проекта, полезно ознакомиться с устройством и особенностями наиболее удачных промышленных образцов. Это помогает точнее понять принцип работы, внести в схему необходимые уточнения.
Рассмотрим некоторые из популярных моделей щепорезов:
Skorpion 350 SDB
Польская дробилка барабанного типа. Справляется не только с мелкими, но с крупными заготовками (поленья до 280 мм). Обладает повышенным запасом прочности режущего инструмента, гусеничная подача способствует обработке мелких фрагментов древесины.
Моби 250
Автономные измельчители, выполненные в виде полуприцепа. Оснащены собственными дизельными двигателями, подключаются к системе гидропривода. Предназначены для работы в полевых условиях.
Cramer COMBI CUT 9600
Немецкий агрегат, обладает хорошим качеством сборки и высокой надежностью всех узлов и деталей. Выполнен в виде автономного узла с собственным двигателем Honda. Способен переработать 830 кг сырья в час.
MTD ROVER 464 Q
Садовый измельчитель веток полупрофессионального уровня. Оснащен двумя раздельными диффузорами для загрузки веток и стеблей растений. Привод от бензинового мотора, для перемещения имеются 2 колеса.
Дровосек МР 300
Универсальный отечественный щепорез стационарного типа, способный работать с электроприводом 22, 380 В или на базе бензинового двигателя. Способен перерабатывать до 300 кг сырья в час. Предназначен для садовых работ с ветками и скошенными стеблями растений.
Viking GE 105
Дисковый щепорез, изготовленный в Австрии. Используется для измельчения веток, обзола и прочих видов исходного сырья. Оснащен электроприводом, максимальная толщина заготовок — 35 мм.
Калибр ЭСИ-2400Н
Китайский садовый измельчитель дискового типа. Оснащен электроприводом с питанием от сети 220 В. Компактный и легкий агрегат, вес которого составляет всего 11 кг.
Перечисленные устройства сравнительно недороги, так как изготовлены преимущественно для использования в саду или на даче. Промышленные установки высокой производительности стоят значительно дороже. Для самостоятельного изготовления лучше выбирать конструкцию небольшой мощности, чтобы не перегружать узлы и детали станка. Это опасно и может привести к разрушениям и травмам.
Заключение
В Ваш сад требуется щепорез?
Конечно!Думаю нет
Необходимо еще раз определить основные этапы создания самодельного щепореза:
- Выбор конструкции.
- Создание рабочего чертежа.
- Приобретение инструментов, материалов.
- Заказ в специализированной мастерской некоторых сложных узлов (обычно это ступицы, приводные валы, ножевые диски и т.п.)
- Сборка станка.
- Испытания, проверка надежности, выявление и исправление ошибок.
- Ввод агрегата в эксплуатацию.
Большинство пользователей за основу принимает готовый каркас или станину, на которые устанавливаются режущие инструменты. В этом вопросе действуют по ситуации, поскольку привязка к имеющимся элементам ограничивает свободу выбора, но сокращает время работ. Основным требованием следует считать прочность, надежность и наличие защитных кожухов на всех вращающихся элементах.
Читайте также другие полезные статьи: