Коэффициент уплотнения асфальтобетона, и его влияние на эксплуатационные характеристики дорожных конструкций.
Состояние автомобильных дорог — извечная российская проблема, выбоины, ямы, сколы и колея влияют прежде всего на безопасность и долговечность дорожных конструкций.
Разрушение и преждевременный износ покрытий автомобильных дорог обусловлен целым комплексом различных факторов, возникающих на стадии производства асфальтобетонной смеси, в процессе доставки готовой смеси к месту производства работ и при укладке асфальтобетона в конструкцию автомобильных дорог.
Существует большое количество видов асфальтобетонных смесей, изготовляемых на производстве и применяемых при строительстве дорожных конструкций. В зависимости от условий эксплуатации автомобильных дорог и требований проектных решений для каждого вида и типа асфальтобетона изготавливается смесь нормируемого состава. Ошибки при подборе составов смесей, применение некачественных исходных материалов приводит к снижению эксплуатационных характеристик асфальтобетона и приводит к появлению внешних и внутренних дефектов в конструкции автомобильной дороги.
Для строительства дорожных покрытий автомобильных дорог в основном применяют горячие асфальтобетонные смеси. Особенностью применения смесей этого вида является необходимость в их укладке и уплотнении при определенных температурах, зависящих от типа смеси и марки битума. Остывшая асфальтобетонная смесь не пригодна при устройстве конструкций автомобильных дорог. Время доставки готовой асфальтобетонной смеси к месту производства работ – главный фактор, влияющий на температуру смеси при ее укладке. Остывание горячей асфальтобетонной смеси в кузове автосамосвала приводит к образованию температурной и фракционной сегрегации (расслоению). Качественно уплотнить такие асфальтобетонные смеси практически невозможно.
Критерием качества уплотнения асфальтобетонных смесей является коэффициент уплотнения. Определить этот показатель возможно только в лабораторных условиях, на основании образцов (кернов), отобранных из конструктивных слоев дорожных одежд.
Отобранные из конструкции образцы разогревают и формуют для определения средней плотности максимально возможного уплотнения данной смеси, отношение средней плотности образцов асфальта отобранных из конструкции к средней плотности переформованного образца называется коэффициентом уплотнения асфальтобетона.
Специалисты Отдела обследования грунтов и конструктивных слоев дорожных одежд ежедневно выезжают на объекты города для контроля качества строительства автомобильных дорог. Проводя статистический анализ работы отдела с января по август 2017 года можно отметить незначительное уменьшение количества нарушений, связанных с коэффициентом уплотнения асфальтобетона, по сравнению с 2016 годом:
Всего за отчетный период специалисты отдела подготовили более 170 заключений по оценке соответствия коэффициента уплотнения асфальтобетона проектной и нормативной документации, выявлено около 30 нарушений:
Все нарушения в установленном порядке переданы в Мосгосстройнадзор для принятия мер.
Ведущий инженер-эксперт ООГиКСДО С.Б. КазаковКакой коэффициент уплотнения асфальта при укладке. | Пенообразователь Rospena
Определение параметра
Чтобы провести определение по нормам Государственного стандарта, необходимо брать образцы – керны – в трех местах покрытия в течение до трех дней при укладке горячего состава и до тридцати дней при работе с холодными материалами.
Технология определения по ГОСТу такая:
Технология укладки и уплотнения
- высушить образцы, пока масса не станет стабильной, охладить и взвесить;
- рассчитать фактическую плотность;
- затем нагреть пробы в термическом шкафу;
- измельчить их, распределить в форме и уплотнить на прессе с давлением 40 МПа, измерить высоту;
- по полученным данным вычислить плотность образцов и средний показатель;
- поделить фактическую плотность на стандартную – это и будет коэффициент уплотнения асфальта при укладке.
При работе с горячими составами уплотняют сперва вибрированием. Полученный параметр нужно сравнить со стандартным – если до стандарта он не дотягивает, значит, на испытуемом участке материал уплотнен недостаточно.
Требования к величине коэффициента
Полученный по пробам параметр сравнивают со значениями стандарта:
- от 0,96 для холодных составов;
- от 0,98 для горячей смеси – В;
- от 0,99 для горячего материала – А, Б.
Если вычисленное значение не соответствует данным стандартам, работы проведены некачественно и асфальтобетонная смесь слишком рыхлая в месте отбора пробы.
Порядок испытаний
Отбор керна проводится сверлением или вырубкой. В результате получаются круглые или прямоугольные части. Не отбирают с края дороги – следует отступить не меньше метра для установки керноотборника. В зависимости от типа смесей, часть асфальта, взятая на анализ, должна соответствовать определенным требованиям:
- песчаные смеси: диаметр керна – 5 см, масса вырубки – 1 кг;
- мелкозернистые – 7 см и 2 кг;
- крупнозернистые – 10 см и 6 кг.
Именно с такими параметрами разрешено проведение лабораторных испытаний без сомнений насчет их результативности и правдоподобности. Другие способы расчета коэффициента, тем более, самостоятельно считаются недействительными и проведенными с нарушениями технологической процедуры определения.
Технология уплотнения асфальтобетонной смеси катками
Соблюдение технологии уплотнения асфальтобетонных смесей напрямую влияет на долговечность и надежность дорожного покрытия. Любая небрежность или нарушение очередности операций уменьшает прочность полотна на 20% и более.
Актуальные требования к организации дорожного строительства отражены в СНиП 3.06.03-85. В этом же сборнике нормативных документов приведена и последовательность действий при асфальтировании дорог различными типами дорожной спецтехники.
Практика показала, без парка специализированной техники быстро построить качественную дорогу, независимо от категории, невозможно. Наиболее перспективна технология уплотнения асфальтобетонной смеси катками в комплексе с асфальтоукладчиком. Первичное подуплотнение трамбующим брусом или виброплитой уменьшает величину сдвиговой волны горячего асфальта при укатке. Благодаря этому получают более плотную структуру дорожного покрытия.
Предварительное уплотнение асфальта — подкатка
Асфальтоукладчик формирует ровный слой асфальтобетнной смеси заданной толщины. На этом же этапе происходит первичное уплотнение асфальта виброплитой или трамбующим брусом. Последующую подкатку выполняют
Технология уплотнения асфальта на предварительном этапе предполагает выполнение следующих операций:
- Предварительное упрочнение и подуплотнение горячей смеси 2-3 проходами катка, работающего в статическом режиме.
- 5-6 проходов катка по следу с включенным вибратором. Вибрационная нагрузка применяется исключительно при движении от асфальтоукладчика. Возвращение к укладчику выполняют при работе вальцов в статическом режиме. В этом случае нагон сдвиговой волны уменьшается.
Уплотнение асфальта катком на этапе подкатки требует соблюдения следующих параметров:
- Допустимая нагрузка в статическом режиме 1,75-1,85 кг/см2, при работе вибратора 2,4-2,6 кг/см2 при частоте до 39 ударов в минуту. Превышение этих показателей приводит к появлению дефектов на покрытии в виде трещин, неровностей или сдвигов.
- Уплотнение выполняется продольными заходами от наружной кромки захватки с постепенным перемещением к оси дороги. 100 мм полоса у осевой кромки укатывается при уплотнении следующей смежной полосы асфальта.
- Каждый предыдущий след перекрывают на 30 см. Скорость перемещения катка не должна превышать 4.8-5.6 км/ч.
- Подходы выполняются возвратно-поступательными движениями ведущими вальцами вперед.
Основной этап уплотнения асфальтобетонных смесей
После проведения работ по предварительному уплотнению, происходит процесс доуплотнение оставшихся слабых мест и общая отделка дорожного покрытия с применением катков на пневмошинах GRW 15, весом 11 тонн. Работы выполняют пневмокатками с весовой нагрузкой 20 тонн с учетом балласта. Важную роль играет одинаковое давление воздуха во всех шинах, оно должно составлять 8-8,5 атмосфер. В процессе укатки каток совершает 8-10 проходок по одному следу с допустимой скоростью перемещения 3,7-6,4 км/ч. Перекрытие смежных следов не должно быть меньше, чем 30 см. Такая технология уплотнения асфальтобетонного покрытия улучшает его прочностные характеристики, увеличивает устойчивость к динамическим нагрузкам.
Финишная укатка асфальта катками
Для финишной укатки асфальта катком технологией предусмотрено применение гладковальцевых статических катков CS 141/142 фирмы Dynapac, общим весом с балластом 13 тонн. Основной целью завершающей стадии укатки является устранение следов от шин пневмокатков и других дефектов поверхности. На завершающем этапе устраняют оставшиеся дефекты, включая следы от шин пневмокатка. При достаточной температуре асфальта (800С) происходит окончательное уплотнение структуры материала. Для завершения работ потребуется 5-8 проходов с перекрытием каждого следа на 30 см., при допустимой скорости движения 4,8 км/ч. Контактные давления вальцов этого катка превышают показатели предыдущих катков.
Качество уплотнения асфальтобетонного покрытия определяют, используя коэффициент уплотнения асфальта. Эта величина показывает соотношение фактической и нормативной плотности материала. Пробы для определения коэффициента берут через 1-3 дня после уплотнения горячих смесей. Качественный асфальтобетон типа А, Б имеет показатель 0,99, а для смеси типа В нормативный коэффициент 0,98.
Укладка и уплотнение щебеночно-мастичной асфальтобетонной смеси Текст научной статьи по специальности «Технологии материалов»
УДК 625.
УКЛАДКА И УПЛОТНЕНИЕ ЩЕБЕНОЧНО-МАСТИЧНОЙ АСФАЛЬТОБЕТОННОЙ СМЕСИ
А.В. Захаренко1, С.С. Шабуров2, Ю.В. Кибирев3, Д.А. Милицын4
1,2Национальный исследовательский Иркутский государственный технический университет,
664074, г. Иркутск, ул. Лермонтова, 83.
3,4ЗАО «Труд», 664017, г. Иркутск, ул. Академическая, 5 а.
Проанализирована совместная работа асфальтоукладчиков и катков различных марок по устройству асфальтобетонных покрытий из щебёночно-мастичных смесей. Даны рекомендации для выбора режимов укладки и уплотнения, приведены результаты испытаний. Табл. 3. Библиогр. 2 назв.
Ключевые слова: укладка; уплотнение; асфальтобетон; каток; асфальтоукладчик; температура.
LAYING AND COMPACTING OF MACADAM MASTIC BITUMINUOUS CONCRETE MIXTURE A.V. Zakharenko, S.S. Shaburov, Y.V. Kibirev, D.A. Militsyn
National Research Irkutsk State Technical University, 83, Lermontov St., Irkutsk, 664074.
Closed Joint Stock Company «Labour», 5a, Akademicheskaya St., Irkutsk, 664017.
The article analyzes a combined work of pavers and rollers of different brands on making bituminous concrete coatings from macadam-mastic mixture. The recommendations on choosing laying and compacting regimes are given, the test results are provided. 3 tables. 2 sources.
Key words: laying; compacting; bituminous concrete; roller; paver; temperature.
Процесс уплотнения асфальтобетонной смеси является завершающим и важнейшим в технологии строительства покрытий, так как достигнутая степень уплотнения обеспечивает необходимую прочность и устойчивость конструкции к воздействию эксплуатационных и климатических факторов. Уплотнение осуществляется в два этапа: предварительное — рабочими органами асфальтоукладчиков, и окончательное -вальцами катков. Повышение степени предварительного уплотнения обеспечивает значимый экономический эффект, сокращая количество катков, обеспечивающих окончательное уплотнение с трёх типов (лёгкий, средний, тяжёлый) до двух или даже одного. Данное исследование проводится с целью выбора параметров эффективного взаимодействия асфальтоукладчиков и катков ЗАО «Труд», гарантирующего достижение нормативной плотности при возможном сокращении числа применяемых катков или числа их проходов при укладке и уплотнении щебёночно-мастичной асфальтобетонной смеси. Щебёночно-мастичный асфальтобетон (ЩМА) — относительно новый материал для строительства асфальтобетонных покрытий, ещё не применявшийся в нашем регионе. Исходя из анализа гранулометрического состава смеси (табл. 1), можно сделать следующие выводы:
— увеличенное содержание щебня (69%) фракции
10-20 мм обеспечивает высокое сопротивление укладке и уплотнению даже по сравнению с многощебенистыми смесями типа А;
— готовое покрытие (при качественном его устройстве) будет обладать продлённым сроком эксплуатации, улучшенной трещиностойкостью, повышенным значением коэффициента сцепления с автомобильным колесом и его малой зависимостью от увлажнения во время дождя.
Для укладки и предварительного уплотнения смеси использовался асфальтоукладчик «Vogele-1800». Его основным рабочим органом, обеспечивающим наибольшее уплотнение, является трамбующий брус. Виброплита обладает меньшим уплотняющим воздействием вследствие сниженной амплитуды колебаний (примерно в 5-10 раз). Размер опорной площадки трамбующего бруса в норме составляет 8-15 мм [1]. В процессе работы взаимное расположение трамбующего бруса и виброплиты периодически контролируется, иначе качества укладки и высокой степени предварительного уплотнения не достичь [2].
Согласно проектным данным, толщина готового покрытия на опытном участке, возводимом ЗАО «Труд», должна составлять 5 см. Исходя из рекомендаций [2], для смеси, наиболее близкой по своим свойствам к укладываемой многощебенистой смеси
1Захаренко Анатолий Владимирович, доктор технических наук, профессор кафедры строительных, дорожных машин и гидравлических систем, тел.: 89148849742.
Zakharenko Anatoly, Doctor of technical sciences, Professor of the Department of Construction, Roadmaking Machinery and Hydraulic Systems, tel.: 89148849742.
2Шабуров Сергей Семенович, кандидат технических наук, профессор кафедры автомобильных дорог, тел.: 89025135889. Shaburov Sergey, Candidate of technical sciences, Professor of the Department of Automobile Roads, tel.: 89025135889.
3Кибирев Юрий Владимирович, главный инженер, тел.: (3952) 563912. Kibirev Yury, Chief Engineer, tel.: (3952) 563912.
4Милицын Дмитрий Александрович, начальник центральной лаборатории, тел.: (3952) 619920. Militsyn Dmitry, Head of the Central Laboratory, tel.: (3952) 619920.
Таблица 1
Зерновой состав смеси_
Материал Карьер номер карточки Содержание, % Содержание зёрен мельче данного размера, (мм), в % по массе
40 20 15 10 5 2,5 1,25 0,63 0,315 0,16 0,071
Щебень фракции 10-20 мм Анга-солка 327 69,0 69,0 62,5 28,5 1,3 0,6 0,6 0,0 0,0 0,0 0,0 0,0
Щебень фракции 5-10 мм Анга-солка 326 9,0 9,0 9,0 9,0 8,2 0,2 0,1 0,1 0,00 0,0 0,00 0,0
Песок из отсевов дробления Анга-солка 325 12,0 12,0 12,0 12,0 12,0 11,6 9,7 6,7 4,73 3,2 1,94 0,85
Минеральный порошок Ново-Олхин-хин-ский извест вест-ковый завод 338 10,0 10,0 10,0 10,0 10,0 10,0 10,0 10,0 10,0 10,0 9,45 7,87
Битум БНД 90/130+ПАВ «БАП-ДС-3» (0,5% от кол-ва битума) ОАО «АНХК» ОАО «Ал-тайспе цпро-дукт» 328 — — — — — — — — — — — —
100,0 100,0 93,51 59,53 31,54 22,44 20,40 16,76 14,73 13,14 11,39 8,71
Пределы полных проходов (рекомендуемые ГОСТ 310152002) 100 100 100 90 70 50 42 25 30 20 25 15 24 13 21 11 19 9 15 8 13 8
типа А, процесс укладки должен происходить при следующих параметрах (табл. апС Ой-158» массой 15,8 т (2 прохода). С учётом этого для окончательного уплотнения предложено два варианта использования техники:
— каток гладковальцовый BW-161 — 6 проходов без вибрации; каток гладковальцовый SANY YZC1211 — 4 прохода без вибрации;
— каток гладковальцовый BW-141 — 6 проходов в вибрационном режиме; каток пневмошинный BW-24R — 4 прохода.
Значительная энергоёмкость уплотнения ЩМА, вызванная высоким содержанием щебня, требует мощного силового воздействие катков. Однако по этой
Параметры укладки
Таблица 2
Тип смеси Температура смеси, °С Частота колебаний, К/мин Скорость движения укладчика, м/мин
трамбующего бруса виброплиты
А 130-140 660-840 2500-3000 1,7-2,5
ЩМА 150-160 600-660 2500-3000 1-2
Таблица 3
Физико-механические свойства смеси
Показатель Значение
по ГОСТ 31015-2002 фактическое
Плотность, кг/см3 — 2,49
Пористость минеральной части, % от 15 до 19 15,10
Остаточная пористость, % от 1,5 до 4,0 2,98
Водонасыщение, % по объёму от 1,0 до 3,5 1,50
Предел прочности при сжатии, МПа, при температуре: 20 °С 50 °С не менее 2,0 не менее 0,60 2,20 0,74
Водостойкость при длительном водонасыщении не менее 0,90 0,92
Сдвигоустойчивость по: — коэффициенту внутреннего трения не менее 0,92 0,94
— сцеплению при сдвиге при температуре 50 °С, МПа не менее 0,16 0,21
Трещиностойкость — предел прочности на растяжение при расколе при температуре 0 °С, МПа не менее 2,0 не более 5,5 3,2
Сцепление вяжущего с минеральной частью ЩМАС-20, % не менее 3/4 поверхности покрыто плёнкой битума более 3/4 поверхности покрыто плёнкой битума
же причине применение вибрационной укатки весьма ограниченно вследствие возможного дробления щебня, входящего в состав смеси. Именно поэтому вибрация используется только на промежуточном этапе укатки и обязательно на высокой частоте (55 Гц), что создаёт минимальную возмущающую силу.
Практически исключает эффект дробления применение на заключительной стадии укатки пневмо-шинного катка BW-24R, массу которого рекомендовано увеличить до 24 т. Большое значение для достижения предельного уплотнения имеет температура укатки. Катком промежуточного уплотнения следует начинать работу при 145-150 °С асфальновой смеси, сразу после прохода асфальтоукладчика, обеспечивающего коэффициент предварительного уплотнения не ниже 0,95. На заключительном этапе температура укатки должна быть не ниже 100-110 °С. Скорость укатки также оказывает существенное влияние на уплотнение, так как при избыточном её значении недопустимо сократится время контакта вальцов и смеси, что приведёт к неполному развитию пластических деформаций, т.е. к фактическому недоиспользованию потенциальных возможностей катков. Так как на опытном участке небольшой протяжённости производительность катков не имеет определяющего значения, рекомендованы скорости укатки, близкие к минимальным: для гладковальцовых катков — 1-2 км/ч; для пневмошинных — 2-3 км/ч.
го слоя нет необходимости, поскольку опыт эксплуатации катков данных марок показывает, что глубина уплотнения превышает 10 см.
Проведённое опытное строительство ЩМА-покрытия на обходе мкр. Ново-Ленино (г. Иркутск) показало следующие результаты. Коэффициент предварительного уплотнения ЩМА после прохода асфальтоукладчика составил 0,95-0,96. После окончательного уплотнения катками первого варианта достигнут коэффициент уплотнения 0,99-1,00. Второй вариант использования катков обеспечил коэффициент уплотнения 1,00-1,01. Таким образом нормативная степень уплотнения достигнута. Анализ результатов показывает, что для дальнейшего применения возможен и третий вариант комплектования катков BW-161, BW-24R, особенно при понижении температуры окружающего воздуха, когда укатку смеси придётся заканчивать в условиях её ускоренного остывания. Физико-механические свойства смеси, определённые в лабораторных условиях, соответствуют требованиям стандарта и представлены в табл. 3.
Достигнутое значение остаточной пористости, безусловно, окажет существенное влияние на поведение покрытия при эксплуатации. Наблюдения за ним в зимний и весенний периоды позволят внести дополнительные коррективы в разработанную технологию для последующего широкого применения ЩМА в дорожном строительстве Приангарья.
В определении допустимой толщины уплотняемо-
Библиографический список
1. Динапак. Уплотнение и укладка дорожных материалов. тельстве. Производственная и техническая эксплуатация / Теория и практика. СПб., 1995. 86 с. Пермяков В.Б. [и др.]. Омск: Изд-во СибАДИ, 2007. 444 с.
2. Технологические машины и комплексы в дорожном строи-
Приборы операционного контроля при дорожном строительстве
Н.В. Величутин, ООО «СКБ Стройприбор»
Для увеличения срока службы автомобильных дорог требуются не только новые технологии, но и средства операционного контроля технологических операций проводимых при их строительстве. В настоящее время в ООО «СКБ Стройприбор» выпускается большое разнообразие средств контроля, которые могут применять не только дорожные лаборатории, но и строительные организации. Многие новые отечественные приборы по своим метрологическим характеристикам не только приблизились к зарубежным аналогам, но и по некоторым позициям превзошли их.
Дорожное основание вместе с земляным полотном и подстилающим слоем служат своеобразной опорой или фундаментом для асфальтобетонного покрытия. От того как будет выполнено дорожное основание зависит, будет ли дорожная одежда прочной или после непродолжительной эксплуатации появится колейность, просадки, трещины и прочие дефекты.
В дорожном строительстве России степень уплотнения песчаных и глинистых грунтов нормируют на основе некоторой эталонной зависимости «влажность грунта при уплотнении — плотность сухого грунта», получаемой опытом на стандартное уплотнение. При нормировании плотности удобнее пользоваться коэффициентом уплотнения, т.к. коэффициент уплотнения является безразмерной величиной и не зависит от состава грунта.
Для определения коэффициента уплотнения грунта применяется метод сравнения плотности выемки грунта с плотностью того же грунта, полученной в лабораторном приборе стандартного уплотнения. ООО «СКБ Стройприбор» выпускает стационарный, полуавтоматический прибор стандартного уплотнения ПСУ-МГ4. Прибор позволяет значительно ускорить получения стандартных характеристик грунта, т.к. в нем уплотнение грунта проводится одновременно в двух формах. В ПСУ-МГ4 имеется счетчик количества ударов (индикация количества ударов на дисплее), после окончания цикла уплотнения прибор автоматически отключается.Для сплошного контроля качества уплотнения грунта можно использовать экспресс-метод основанный на увеличении удельного сопротивления пенетрации с увеличением плотности грунта. В ООО «СКБ Стройприбор» выпускаются пенетрометры статического действия с помощью которого можно косвенно определить механические свойства грунта такие как угол внутреннего трения, модуль упругости, коэффициент уплотнения, плотность (для песчаных грунтов). Для измерения усилия пенетрации в ПСГ-МГ4 применяется тензометрический датчик силы. Для компенсации веса пенетрометра перед проведением измерения предусмотрена автоподстройка нуля. Вдавливание пенетрометра в грунт проводится плавно в течении 5 ÷ 10 секунд на глубину до 75 мм. Для уменьшения погрешности измерения в приборе применяется статистическая обработка измеряемого усилия при внедрении наконечника в грунт.
Перед проведением измерений пенетрометр необходимо настроить (откалибровать) на том типе грунта по которому в дальнейшем будет проводиться контроль. Для песчаных грунтов усилие пенетрации слабо зависит от влажности поэтому для таких грунтов можно построить и ввести в память прибора зависимость удельное сопротивление пенетрации – плотность грунта. В прибор можно ввести четыре таких зависимости для крупного, среднего, мелкого и пылеватого песка. Удельное сопротивление пенетрации глин и суглинков зависит не только от плотности, но и от влажности в связи с чем перед проведением измерений для таких грунтов необходимо определить максимальное усилие пенетрации после уплотнения такого грунта в приборе стандартного уплотнения.
Для измерения модуля упругости (модуля динамической деформации или несущей способности) грунтового и щебеночного основания дорожного полотна в ряде стран используются малогабаритные установки динамического нагружения. Установка динамического нагружения снабжается подвижным грузом, при сбрасывании которого на амортизатор возникает динамическое усилие, которое через круглый штамп воздействует на контролируемую поверхность. В измерителе модуля упругости ООО «СКБ Стройприбор» ПДУ-МГ4 (и его модификациях) модуль упругости определяется исходя как из измеренной деформации дорожного основания, так и измеренной силе действующей на круглый штамп. Применение в приборе двух датчиков (датчика силы и датчика перемещения), а также удлиненной направляющей с перемещаемым механизмом фиксации груза позволяет регулировать силу удара и значительно расширить диапазон определения модуля упругости. Применение корректного расчета существенно уменьшило разницу в показаниях при определении модуля упругости статическим и динамическим методами.
Для измерения теплопроводности мерзлых и талых грунтов, а так же для определения начала температуры замерзания грунта в ООО «СКБ Стройприбор» разработан прибор ИТП-МГ4 «Грунт». Прибор работает в стационарных условиях, все измерения проводятся в автоматическом режиме.
Немаловажное значение при укладке асфальтобетонного покрытия имеет качество уплотнения. Для измерения плотности асфальтобетона в ООО «СКБ Стройприбор» разработан и изготавливается серийно плотномер асфальтобетона ПА-МГ4. Основная трудность, с которой столкнулись при разработке данного прибора это присутствие воды на асфальтобетонном покрытии. Ёмкостный датчик в качестве чувствительного элемента был исключен сразу. Хотя применение ёмкостного датчика и позволяет получить большую точность при измерении плотности, но наличие воды существенно искажает результаты измерений, так как диэлектрическая проницаемость воды 80 существенно выше диэлектрической проницаемости асфальтобетонной смеси 4 ¸ 6. Кроме того такой прибор необходимо будет калибровать под конкретный материал, возникнет потребность в постоянной установке «нуля», при наличии воды показания будут существенно завышены.
В приборе удалось решить проблему определения наличия воды в асфальтобетоне и ввести компенсацию влажности на показания плотности с применением радиоволнового метода измерения. Прибор работает на двух частотах, имеет две передающих и одну приемную антенну, которые позволяют проводить зондирование асфальтобетонной смеси на глубину до 20 и до 150 мм.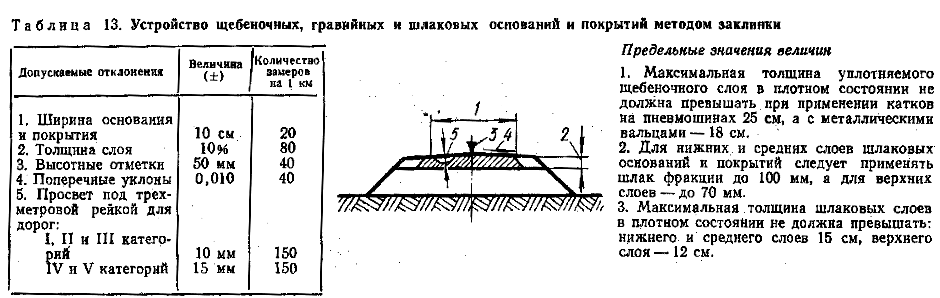
В приборе нет процедуры установки нуля. Имеется всего лишь одна базовая зависимость. И самое основное — прибор может измерять плотность асфальтобетона с погрешностью 2,5% без предварительной калибровки практически на любых типах асфальтобетонов с любым материалом заполнителя (исключение составляет асфальтопесчаная смесь, и другие смеси типа Г). В приборе проводится коррекция результатов измерения в зависимости от температуры асфальтобетонной смеси и даже от температуры окружающего воздуха. Прибор имеет несколько режимов измерения: непрерывный и одиночный, а так же режим измерения с усреднением. В процессе измерения на дисплее плотномера отображаются: плотность асфальтобетонной смеси; коэффициент уплотнения; температура и влажность покрытия. В отличие от зарубежных аналогов в ПА-МГ4 измерения выполняются в более широком частотном диапазоне, что позволяет точнее определять влажность покрытия и как следствие повысить точность в определении плотности асфальтобетона с учетом корректировки на влажность.
Для определения качества битума на предприятии выпускаются пенетрометр АПН-360МГ4 и прибор ИКШ-МГ4.Пенетрометр АПН-360МГ4 предназначен для определения глубины проникания иглы (пенетрации) в испытуемый образец при заданных нагрузке и температуре по ГОСТ 11501-78 в соответствии с МИ2418. Пенетрометр обеспечивает автоматическую регистрацию глубины проникания иглы и времени испытаний. Процесс испытаний отображается на графическом дисплее. Остановка процесса испытаний – автоматическая, с занесением результата в память прибора. Прибор оснащен пузырьковым уровнем, регулировочными ножками, подъемным столом, подсветкой иглы.
Прибор ИКШ-МГ4 предназначен для определения температуры размягчения нефтебитумов по ГОСТ 11506-73 в соответствии с МИ 2418.Прибор обеспечивает автоматический нагрев образцов с заданной скоростью, фиксацию и запоминание температуры размягчения. Равномерность нагрева по высоте (в объеме) обеспечивается механической мешалкой. Процесс испытания отображается на дисплее. Остановка испытаний – автоматическая, с занесением результата в память прибора.
Все приборы оснащены функцией передачи данных на ПК.
На основании вышеизложенного можно сделать вывод, что для получения высококачественного дорожного полотна необходим постоянный инструментальный контроль как при устройстве грунтового и щебеночного основания, так и при укладке асфальтобетонного покрытия. Приборы позволяющие проводить оперативный контроль с требуемыми метрологическими характеристиками имеются.
Все публикации
Архив по годам: 2006; 2008; 2013; 2015; 2016; 2018; 2019; 2020;
Влияние химических добавок на коэффициент уплотнения асфальтобетона при строительстве покрытия в условиях пониженных температур
Библиографическое описание:Боль, П. В. Влияние химических добавок на коэффициент уплотнения асфальтобетона при строительстве покрытия в условиях пониженных температур / П. В. Боль. — Текст : непосредственный // Молодой ученый. — 2016. — № 17 (121). — С. 25-27. — URL: https://moluch.ru/archive/121/33399/ (дата обращения: 22.03.2021).
Влияние химических добавок на коэффициент уплотнения асфальтобетона при строительстве покрытия вусловиях пониженных температур
Боль Павел Владимирович, магистрант
Сибирская государственная автомобильно-дорожная академия
В статье представлены результаты испытаний асфальтобетона, в состав которого введены химические добавки EVOTHERM®J-1 (США), CECECABASE RT945 (Франция), REDISETTMWMX (Швеция), позволяющие понижать температуру смеси при производстве работ.
Ключевые слова: асфальтобетонная смесь, химическая добавка
Указания по производству работ при строительстве асфальтобетонных покрытий из горячих смесей в условиях пониженных температур [1] требуют применения в составе смесей химических добавок, таких как EVOTHERM®J-1, CECECABASE RT945, REDISETTMWMX, выпускаемых в США, Франции и Швеции. Целью нашей публикации является определение возможности уплотнения горячей асфальтобетонной смеси до требуемых [2] значений.
Смеси с пластифицирующими добавками выпускались 2015 г. на асфальтобетонном заводе (АБЗ), являющемся структурным подразделением управления дорожного хозяйства и благоустройства г. Омска (УДХБ г. Омска). Строительство покрытий выполнялось в период с августа по ноябрь 2015 г. на улично-дорожной сети в Омске. Из построенного покрытия брались вырубки для определения средней плотности асфальтобетона. На дорогах производилась экспресс оценка средней плотности асфальтобетона, что позволяло сгустить сетку контроля и увеличить объем выборки средних плотностей. Обоснование сгущения сетки контроля выполнено аналогично методикам, описанным работах [3–6], и применяемым для обоснования увеличения количества испытаний при определении коэффициента уплотнения земляного полотна. Максимальная средняя плотность определялась ежедневно в лаборатории АБЗ. Комплекс этих мероприятий позволил набрать внушительные выборки коэффициентов уплотнения.
Деление выборок произведено по факторам: виду используемой добавки, температуре воздуха и скорости ветра, при которых выполнено укладка и уплотнение смеси. Выборки обработаны методами математической статистики, что позволило установить вероятности уплотнения смеси до требуемого коэффициента уплотнения 0,99. Результаты статистической обработки приведены в табл. 1.
Таблица 1
Вероятность уплотнения горячей асфальтобетонной смеси типа Бс химическими добавками до коэффициента уплотнения 0,99
Вид добавки | Скорость ветра | Вероятность уплотнения смеси типа Бдо коэффициента уплотнения 0,99 при температуре | ||
0оС | -5оС | -10оС | ||
EVOTHERM®J-1 | 2 | 99 | 98 | 95 |
4 | 98 | 95 | 90 | |
CECECABASE RT945 | 3 | 98 | 97 | 90 |
5 | 97 | 95 | 85 | |
REDISETTMWMX | 2 | 99 | 98 | 96 |
3 | 98 | 96 | 93 | |
В результате мы пришли к выводу, что применение добавок EVOTHERM®J-1 и REDISETTMWMX наиболее рационально при устройстве покрытия в условиях пониженных температур воздуха.
Весной 2016 г. выполнены штамповые испытания дорожных одежд с асфальтобетонным покрытием, построенным при пониженных температурах воздуха в 2015 г. Методика и оборудования аналогична, применяемым для испытания грунтов [7].
Строительство при пониженных температурах [1] имеет особенностями, что требует более детального расчета толщины таких покрытий и дорожной одежды в целом. Для этого мы применили современные расчетные методики, опубликованные в работах [8–12]. Эти работы позволили разработать альбом типовых конструкций с асфальтобетонными покрытиями при их строительстве при пониженных температурах, величина которых ниже 0 о С. В этом альбоме выполнено прогнозирование пластических деформаций по функциям работы [11], но с параметрами асфальтобетона, установленными в работе [12]. Также рассчитан срок службы до начала пластичности по критериям сопротивления сдвигу [9, 10] и разрушения по критериям Писаренко–Лебедева и О. Мора [9, 13, 14].
Литература:
1. Методические рекомендации по строительству асфальтобетонных покрытий при пониженных температурах воздуха. — М.: Союздорнии, 1976.
2. СП 78.13330.2012 Автомобильные дороги. Актуализированная редакция СНиП 3.06.03–85.
3. Александрова Н. П., Семенова Т. В. Совершенствование методов экспресс контроля уплотнения грунтов в земляном полотне лесных дорог. Часть 1. Обобщающая математическая модель // Международный научно-исследовательский журнал. — 2016. № 6–2(48). — С. 10–14.
4. Александрова Н. П., Троценко Н. А. Применение измерителя жесткости грунта Geogauge для оценки качества уплотнения при операционном контроле // Вестник СибАДИ, 2014, № 3 — С. 40–47.
5. Александрова Н. П., Семенова Т. В., Долгих Г. В. Методы определения максимальной плотности грунтов земляного полотна автомобильных дорог [Электронный ресурс]: учебно-методическое пособие — Электрон. дан. − Омск: СибАДИ, 2015. — Режим доступа: http://bek.sibadi.org/fulltext/ESD53. pdf, свободный после авторизации. — Загл. с экрана.
6. Александрова Н. П., Семенова Т. В., Стригун К. Ю. Совершенствование методов экспресс оценки качества уплотнения грунтов земляного полотна строительства автомобильных дорог / Н. П. Александрова, // Вестник СибАДИ. — 2015. — № 4. — С. 46–57.
7. Калинин А. Л., Долгих Г. В., Александров А. С. Штамповые испытания песчаных слоев дорожной одежды, армированных геосинтетикой // Вестник научных конференций. 2016. № 5–2 (9). С. 65–66.
8. Александрова Н. П., Александров А. С., Чусов В. В. Модификация критериев прочности и условий пластичности при расчетах дорожных одежд // Вестник Сибирской государственной автомобильно-дорожной академии. — 2015. № 1 (41). — С. 47–54.
9. Александрова Н. П., Чусов В. В. Особенности расчета асфальтобетонных покрытий по сопротивлению сдвигу с учетом накапливания повреждений // Вестник Сибирской государственной автомобильно-дорожной академии. — 2016. № 3 (49). — С. 42–50.
10. Чусов В. В., Александрова Н. П. Два способа расчета мер теории накапливания повреждений // В сборнике: Наука XXI века: опыт прошлого — взгляд в будущее: материала II международной научно-практической конференции — Омск, СибАДИ, 2016 — С. 271–275.
11. Стригун Т. В., Александрова Н. П. Моделирование пластических деформаций дискретных материалов в слоях дорожных конструкций// В сборнике: Наука XXI века: опыт прошлого — взгляд в будущее: материала II международной научно-практической конференции — Омск, СибАДИ, 2016. — С. 229–233.
12. Кузин Н. В. Исследование пластичности дорожных асфальтобетонов // Молодой ученый. — 2016. — № 10 (114). — С. 255–257.
13. Чусов В. В. Модифицированные критерии Писаренко-Лебедева и Кулона-Мора, учитывающие меры теории накапливания повреждений // Молодой ученый. — 2016. — № 9 (113). — С. 338–341.
14. Чусов В. В. Прогнозирование изменения мер теории накапливания повреждений при циклической нагрузке // В сборнике: Наука сегодня: глобальные вызовы и механизмы развития: материалы международной научно-практической конференции, г. 3 проходов легких катков проверять ровность покрытия трехметровой рейкой и шаблоном поперечного’уклона. Покрытие считается укатанным, если перед катком на покрытии не образуется волна и не отпечатывается след вальца. Уплотнение асфальтобетонной смеси в недоступных для катка участках должно производиться с помощью горячих металлических трамбовок до полного исчезновения следов от их ударов на поверхности покрытия. При устройстве цементобетонных покрытий необходимо проверять: плотность и ровность основания, правильность установки опалубки и устройства швов, толщину покрытия (путем взятия одного керна с площади не более 2000 м2), режим ухода за бетоном, ровность покрытия и отсутствие на его
поверхности пленок цементного молока. Коэффициент уплотнения песчаного основания для бетонных монолитных покрытий должен быть не ниже 0,98. Зазоры под трехметровой рейкой на поверхности спланированного основания не должны превышать 10 мм. Разница в отметках смежных элементов опалубки (рельс-форм) не должна превышать 5 мм. Зазор между опалубкой каркасом деформационных швов и прокладками должен быть не более 5 мм. При устройстве бетонных покрытий необходимо контролировать тщательность уплотнения бетона и деформационных швов и в местах примыкания к опалубке. Уложенный бетон покрытия должен быть предохранен защитными покрытиями (пленкообразующими материалами, битумными или дегтевыми эмульсиями или слоем песка толщиной не менее 10 см по слою битумизированной бумаги) от обезвоживания после исчезновения излишков влаги с его поверхности, но не позже 4 ч с момента укладки. Изъятие деревянных реек из швов сжатия и расширения должно осуществляться не ранее чем через две недели после устройства покрытия. При изъятии реек необходимо не допускать поломки кромок швов. При нарезке деформационных швов нарезчиками с алмазными дисками прочность бетона покрытия должна быть не менее 100 кгс/см2. Швы нарезают на глубину не менее 1Д толщины покрытия и заполняют горячими мастиками. Температура разогрева битума для приготовления мастик и мастик во время их укладки должна быть равна -f-160 —f-180 °С.
Укладку плит сборных покрытий внутриквартальных проездов, тротуаров и площадок необходимо производить под уклон на заранее подготовленйое основание, начиная с маячного ряда, располагаемого по оси покрытия или по его краю в зависимости от направления стока поверхностных вод. Посадку плит на песчаное «основание необходимо производить вибропосадочными машинами, а прикатку — транспортными средствами до исчезновения видимых осадок плит. Уступы в стыках смежных плит не должны превышать 5 мм. Сразу после окончания посадок плит следует производить заполнение швов между плитами герметизирующими материалами. Песчаное основание для сборных плиточных покрытий тротуаров и пешеходных дорожек, не рассчитанных на воздействие 8-тонной осевой нагрузки . от транспортных средств, должно быть толщиной не менее 3 см и иметь боковой упор из грунта и быть уплотненным до коэффициента плотности не ниже 0,98. Не допускается наличие просветов основания при проверке его шаблоном или контрольной рейкой. Необходимо обеспечивать при укладке плиток их полное прилегание к основанию (путем осадки погружения плиток в песок основания до 2 мм). Вертикальные смещения между плитками не должны быть более 2, а ширина швов —не более 15 мм (за исключением покрытий с расширенными декоративными швами). Бортовые .камни должны повторять проектный профиль покрытия. Швы между камнями должны быть не более 10 мм и заполняться раствором, приготовленным на. портландцементе марки не ниже 400 и имеющем подвижность, соответствующую 5—6 см погружения стандартного конуса. В стыках бортовых камней в плане и профиле не допускаются уступы. Не разрешается устройство криволинейного борта радиусом 15 м и менее из прямолинейных камней. Бортовые камни устанавливают на грунтовом основании, уплотненном до плотности при коэффициенте не менее 0,98, или на бетонном основании с присыпкой грунтом с наружной стороны или укреплением бетоном. Бортовые камни в местах пересечения внутриквартальных проездов и пешеходных дорожек с тротуарами, подходами к площадкам и проезжей частью должны заглубляться с устройством плавных примыканий (для обеспечения проезда детских колясок, санок и въезда транспортных средств).
Отмостки по периметру зданий должны плотно примыкать к цоколю здания и иметь уклон 1—10%. Наружная кромка отмосток в пределах прямолинейных участков не должна иметь искривлений по горизонтали и вертикали более 10 мм. Ступени наружных лестниц должны иметь уклон не менее 1%, в сторону вышележащей ступени, а также вдоль ступени. Изготавливают ступени из бетона марки не ниже 300 и морозостойкостью не менее 150. Отклонения от проектных размеров при устройстве проездов, дорожек и площадок не должны превышать:
— высотные отметки при устройстве оснований под покрытия и покрытий всех видов ±5 см;
— толщины слоев морозозащитных, изолирующих, дренирующих, а также оснований и покрытий всех видов ±10%, но не более 20 мм;
— допускается просвет под трехметровой рейкой на основаниях и покрытиях: из грунтов, щебеночных, гравийных и шлаковых—15 мм; из асфальтобетона, битумоминеральных смесей и из цементобетона — 5 мм;
— ширины слоя основания или покрытия всех видов, кроме цементобетон-ных-«ДО см} из цементобетона — 5 см.
Похожие статьи:
Противопожарное оборудование жилых и общественных зданий
Навигация:
Главная → Все категории → Контроль качества зданий
Статьи по теме:
Главная → Справочник → Статьи → Блог → Форум
Уплотнение горячих асфальтовых покрытий: Часть I
Единственным наиболее важным фактором, влияющим на долгосрочную долговечность покрытия из горячего асфальта (HMA), является плотность смеси, которая достигается подрядчиком во время строительства. Плотность материала определяется как вес материала, занимающего определенный объем пространства. Процесс уплотнения вызывает сжатие асфальтобетонной смеси и уменьшение ее объема. По мере увеличения плотности горячего асфальтового материала содержание воздушных пустот в смеси уменьшается (они обратно пропорциональны друг другу).Правильно спроектированная смесь HMA должна иметь содержание воздушных пустот в диапазоне от 3% до 5%.
Если уплотненная горячая асфальтовая смесь имеет высокое содержание воздушных пустот (более 8%), смесь не будет работать так же хорошо при движении. Точно так же, если уплотненная асфальтовая смесь имеет низкое содержание воздушных пустот (менее 3%), смесь будет подвержена остаточной деформации или колейности, а также деформации под воздействием транспортных нагрузок. Таким образом, для того, чтобы смесь функционировала должным образом, подрядчик должен иметь возможность уплотнять смесь до желаемого уровня плотности или содержания воздушных пустот.
Плотность асфальтобетонной смеси определяет ее долговечность. Все следующие факторы связаны с содержанием воздушных пустот в горячем асфальтовом материале: усталостная долговечность; остаточная деформация; окисление; повреждение от влаги; искажение; и распад.
По мере того, как воздушные пустоты в горячей асфальтовой смеси уменьшаются, усталостная долговечность или количество повторений нагрузки до разрушения этой смеси увеличивается. Испытания показали, что уменьшение содержания воздушных пустот в данной асфальтобетонной смеси с 8% до 5% может удвоить усталостную долговечность дорожного покрытия.Таким образом, для данной толщины HMA как части конструкции дорожного покрытия способность смеси выдерживать нагрузку может быть значительно увеличена, когда смесь уплотняется до более низкого содержания воздушных пустот.
Устранение неисправностей
Степень остаточной деформации или колейности, которая возникает под нагрузкой в горячем асфальтовом материале, также напрямую связана с содержанием воздушных пустот в смеси. По мере того как содержание воздушных пустот уменьшается, количество колейности, которое может возникнуть в этой смеси, также уменьшается.При правильной конструкции смеси хорошо уплотненная смесь не будет покидать колеи под действием транспортных нагрузок. Если конструкция смеси в каком-либо аспекте несовершенна, надлежащее уплотнение смеси все же может значительно снизить количество колейности и поперечных искажений, которые будут возникать при повторяющихся приложениях нагрузки. Если, однако, содержание воздушных пустот в смеси уменьшается до менее 3%, это может привести к увеличению скорости образования колейности смеси.
Со временем асфальто-цементное вяжущее в асфальтобетонной смеси окисляется и становится более хрупким.Этот процесс окисления или старения приводит к уменьшению пенетрации и увеличению вязкости асфальтового цемента. Скорость окисления напрямую связана с содержанием воздуха в смеси. Чем ниже содержание воздушных пустот, тем менее быстро горячий асфальтовый материал будет стареть и становиться более жестким.
Повреждение или снятие влаги происходит, когда вода может попасть в смесь и под повторяющимся движением транспорта пробивается между асфальтовым покрытием на заполнителе и поверхностью заполнителя.Степень повреждения влагой в первую очередь связана с характеристиками заполнителя, используемого в смеси, но также напрямую связана с содержанием воздушных пустот в смеси. По мере того, как содержание воздушных пустот в смеси уменьшается, количество повреждений, наносимых влагой, также уменьшается. Действительно, смесь, которая может плохо отслаиваться при содержании воздушных пустот 8%, может не пострадать от влаги, если она может быть уплотнена до содержания воздушных пустот ниже 4%.
Искажение или толчок — это смещение смеси, обычно в продольном направлении, под действием движения.Искажение в первую очередь связано с дизайном и свойствами смеси, но также связано с содержанием воздушных пустот. Для данной смеси уменьшение содержания воздушных пустот во время строительства уменьшит количество искажений, которым смесь будет подвергаться при воздействии транспортных нагрузок, особенно при остановках или поворотах. Увеличение плотности смеси (уменьшение содержания воздушных пустот) увеличит внутреннюю стабильность и прочность смеси и может значительно снизить степень деформации, возникающей под нагрузкой.
Распад или растрескивание напрямую связаны с содержанием воздушных пустот в смеси. Если смесь должным образом уплотнена (до содержания воздушных пустот 8% или меньше), она, как правило, не рассыпается при правильном содержании асфальта. Однако, если та же смесь уплотняется до высокого содержания воздушных пустот, под воздействием транспортных нагрузок может произойти сильное расслоение. По мере того, как содержание воздушных пустот в смеси уменьшается, количество растекания также будет уменьшаться.
Асфальтобетонная смесь должна быть полностью уплотнена, прежде чем она остынет до температуры около 175 F.При температурах выше этого значения смесь обычно все еще достаточно теплая, чтобы оборудование для уплотнения могло переориентировать частицы заполнителя в их наиболее плотную конфигурацию. Однако ниже этой температуры смесь, как правило, слишком густая, чтобы значительно увеличивать ее плотность при продолжении прокатки, хотя следы от валков часто можно удалить ниже этой предельной температуры уплотнения. Поэтому смесь необходимо уплотнять, пока она еще горячая. Пять факторов напрямую влияют на скорость охлаждения асфальтобетонной смеси, когда этот материал помещается поверх другого существующего слоя конструкции дорожного покрытия.Эти переменные: температура воздуха; базовая температура; температура выкладывания смеси; толщина слоя; и скорость ветра.
При прочих равных условиях, при повышении температуры окружающего воздуха время, доступное для уплотнения, также увеличивается. Смесь потребуется больше времени, чтобы остыть до предельной температуры 175 F в теплый день, чем в прохладный. Повышение температуры воздуха позволяет оборудованию для уплотнения достичь желаемого уровня плотности смеси.
Более важной, чем температура воздуха, в скорости охлаждения горячей асфальтовой смеси является температура поверхности слоя, на который укладывается новая смесь.Хорошо известно, что тепло в слое асфальтобетона теряется в двух направлениях. Поверхность смеси охлаждается по мере передачи тепла воздуху. Нижняя часть смеси также охлаждается, поскольку тепло передается нижележащему основному материалу. Смесь охлаждается вниз в основание быстрее, чем вверх в окружающий воздух.
Базовая температура — температура слоя, на который укладывается новая асфальтобетонная смесь — на самом деле более важна, чем температура воздуха при определении времени, доступного для уплотнения.Повышение базовой температуры дает больше времени для уплотнения.
По мере увеличения температуры смеси, выходящей из-под стяжки, время, доступное для уплотнения, также увеличивается. Смесь, помещенная при температуре 300 F, для данной толщины подъема и других факторов окружающей среды, потребует больше времени для охлаждения до предельной температуры 175 F, чем та же смесь, помещенная при температуре 250 F.
Толщина критически важна для скорости охлаждения
Вероятно, наиболее важным фактором в скорости охлаждения асфальтобетонной смеси является толщина укладываемого и уплотняемого слоя.По мере увеличения толщины слоя время, доступное для уплотнения, также увеличивается. Для 3-дюймовой модели требуется значительно больше времени. толстый слой горячей асфальтовой смеси для охлаждения до предельной температуры 175 F, чем для 1 дюйм. слой остыть до той же температуры. Время охлаждения не прямо пропорционально толщине подъема, но геометрически пропорционально. Например, в день при 40 F при той же температуре основания, 3 дюйма. Толстому слою HMA, помещенному при температуре 250 F, потребуется 19 минут, чтобы охладиться от температуры укладки до температуры отсечки 175 F.В тот же день 40 F, с той же базовой температурой и для той же температуры укладки смеси 250 F, 1 дюйм. толстый слой HMA остынет до температуры отсечки всего за 3 минуты.
Тонкий слой асфальтобетонной смеси остывает быстрее при сильном ветре, чем при слабом ветре или его отсутствии. Ветер оказывает гораздо большее влияние на поверхность смеси, чем на различных глубинах в слое HMA. Сильный ветер может вызвать настолько быстрое охлаждение поверхности, что образуется корка.Эта корка должна быть разрушена роликами до завершения процесса уплотнения. Чем выше скорость ветра, тем меньше времени остается на уплотнение, при прочих равных условиях.
Диксон и Корлью опубликовали набор кривых охлаждения для асфальтобетонных смесей. Эти кривые показывают количество времени, доступное для уплотнения при различных комбинациях условий. Кривые воспроизведены в Разделе Шестой Части Третьей Руководства по укладке горячего асфальта, доступного в Национальной ассоциации асфальтобетонных покрытий.Для ввода графиков используются три переменные: температура укладки смеси, базовая температура (которая считается равной температуре воздуха) и толщина уплотненного слоя.
Уплотнение | Вашингтонская ассоциация асфальтобетонных покрытий
Уплотнение — это процесс, при котором объем воздуха в смеси HMA уменьшается за счет использования внешних сил для переориентации составляющих частиц агрегата в более близкорасположенную структуру. Это уменьшение объема воздуха в смеси приводит к соответствующему увеличению плотности HMA (Roberts et al., 1996).
Уплотнение является важнейшим фактором, определяющим характеристики плотного ступенчатого покрытия (Scherocman and Martenson 1984; Scherocman 1984; Geller 1984; Brown 1984; Bell et al. 1984; Hughes 1984; Hughes 1989). Неадекватное уплотнение приводит к уменьшению жесткости дорожного покрытия, уменьшению усталостной долговечности, ускоренному старению / снижению прочности, образованию колейности, растрескиванию и повреждению от влаги (Hughes, 1984; Hughes, 1989).
Рисунки 1: Катки в работе
Рисунки 2: Катки в работе
Compaction Measurement and ReportingCompaction уменьшает объем воздуха в HMA.Поэтому характерной особенностью, вызывающей озабоченность, является объем воздуха в уплотненном покрытии, обычно определяемый количественно как процент воздушных пустот по объему и выражаемый как «процент воздушных пустот». Процент воздушных пустот рассчитывается путем сравнения плотности испытуемого образца с плотностью, которую он теоретически имел бы, если бы все воздушные пустоты были удалены, известной как «теоретическая максимальная плотность» (TMD) или «плотность риса» после изобретателя процедуры испытания.
Хотя процент воздушных пустот является интересующей характеристикой HMA, измерения обычно указываются как измеренная плотность по отношению к эталонной плотности.Это делается путем сообщения плотности как:
.- Процент TMD (или «процент риса») . Выражение плотности легко преобразовать в воздушные пустоты, потому что любой объем, не являющийся асфальтовым вяжущим или заполнителем, считается воздухом. Например, плотность 93 процентов риса означает, что имеется 7 процентов воздушных пустот (100% — 93% = 7%).
- Процент от лабораторно определенной плотности . Лабораторная плотность — это обычно плотность, полученная при проектировании смеси.
- Процент плотности контрольной полосы . Контрольная полоса — это короткая дорожная полоса, которая уплотняется до желаемого значения при тщательном изучении, а затем используется в качестве стандарта уплотнения для конкретной работы.
Тротуарная записка WAPA с отчетом о уплотнении
WSDOT сообщает о уплотнении в процентах от TMD, и поэтому большинство других агентств и владельцев также склонны использовать этот метод отчетности.
Воздушные пустоты в дорожном покрытии измеряются в полевых условиях одним из двух основных методов:
- Сердечники (Рисунок 3) .Небольшой сердечник дорожного покрытия извлекается из уплотненного HMA и отправляется в лабораторию для определения его плотности. Обычно результаты измерения плотности ядра доступны не раньше, чем на следующий день. Этот тип тестирования воздушных пустот обычно считается наиболее точным, но также требует больших затрат времени и средств.
- Ядерные манометры (Рисунок 4) . Измеритель ядерной плотности измеряет плотность HMA на месте с помощью гамма-излучения. Датчики обычно содержат небольшой источник гамма-излучения (около 10 мКи), такой как цезий-137, расположенный на наконечнике небольшого зонда, который либо помещается на поверхность тротуара, либо вставляется в тротуар.Показания снимаются примерно через 2–3 минуты.
Каждое подрядное агентство или собственник обычно указывает методы и оборудование для измерения уплотнения, которые будут использоваться в контрактах, находящихся под их юрисдикцией.
WAPA Pavement Note по измерению уплотнения на месте
WSDOT использует ядерные датчики для измерения уплотнения для использования при оплате контракта. Ядерные датчики всегда калибруются по измерениям плотности активной зоны.
Рисунок 3: Извлечение керна
Рисунок 4: Измеритель ядерной плотности
Факторы, влияющие на уплотнение
На уплотнениеHMA влияет множество факторов; некоторые из них связаны с окружающей средой, некоторые определяются составом и структурным проектированием, а некоторые находятся под контролем подрядчика и агентства во время строительства (см. Таблицу 1).
Таблица 1: Факторы, влияющие на уплотнение
Факторы окружающей среды | Факторы смешанных свойств | Конструкторы | |||||
Температура | Агрегат | Катки | |||||
Температура земли Температура воздуха Скорость ветра Солнечный поток | Градация Размер Форма Трещины Объем | Тип Число Скорость и синхронизация Количество проходов Толщина подъема | |||||
Вяжущее асфальтовое | Другое | ||||||
Химические свойства Физические свойства Количество | Производственная температура HMA Расстояние транспортировки Время транспортировки Опора фундамента |
Оборудование для уплотнения
Для уплотнения HMA доступно три основных вида оборудования: (1) асфальтоукладчик, (2) каток со стальными колесами и (3) каток с пневматическими шинами.Каждая единица оборудования уплотняет HMA двумя основными способами:
- Путем приложения веса к поверхности HMA и сжатия материала под областью контакта с землей . Поскольку это сжатие будет больше при более длительных периодах контакта, более низкие скорости оборудования будут производить большее сжатие. Очевидно, что более высокий вес оборудования также приведет к увеличению сжатия.
- B y, создающее напряжение сдвига между сжатым материалом под областью контакта с землей и соседним несжатым материалом .В сочетании со скоростью оборудования это дает скорость сдвига. Снижение скорости оборудования может снизить скорость сдвига, что увеличивает напряжение сдвига. Более высокие напряжения сдвига способны преобразовывать заполнитель в более плотные конфигурации.
Эти два средства уплотнения HMA часто вместе именуются « усилие уплотнения ».
Асфальтоукладчик
Приблизительно от 75 до 85 процентов TMD будет получено, когда смесь выйдет из-под стяжки (Рисунок 5) (TRB 2000).
Рис. 5: Когда мат выходит за стяжку, его толщина составляет около 75–85% от TMD.
Стальные колесные катки
Стальные колесные катки — это самоходные уплотняющие устройства, в которых для сжатия нижележащей HMA используются стальные барабаны. Они могут иметь один, два или даже три барабана, хотя чаще всего используются тандемные (2 барабанные) катки. Барабаны могут быть статическими или вибрирующими и обычно имеют ширину от 35 до 85 дюймов и диаметр от 20 до 60 дюймов. Вес ролика обычно составляет от 1 до 20 тонн (рисунки 6 и 7).
Некоторые стальные колесные катки оснащены вибрационными барабанами. Вибрация барабана добавляет динамическую нагрузку к статическому весу ролика, создавая большее общее усилие уплотнения. Вибрация барабана также снижает трение и блокировку заполнителя во время уплотнения, что позволяет частицам заполнителя перемещаться в конечные положения, которые создают большее трение и блокировку, чем можно было бы достичь без вибрации. Как правило, комбинация скорости и частоты, которая дает 10–12 ударов на ногу, является хорошей.При 3000 полуколебаниях в минуту это приводит к скорости 2,8 — 3,4 миль в час. Новые стальные колесные ролики также могут быть оснащены «колеблющимися» барабанами, которые по сути представляют собой вибрационные барабаны с более круговым (а не вертикальным) движением.
Рисунок 6: Малый статический стальной колесный каток 1,45 тонны, барабан шириной 34 дюйма
Рисунок 7: Большой стальной вибрационный каток 18,7 т, барабан шириной 84 дюйма
Пневматические катки для шин
Катки с пневматическими шинами представляют собой самоходные уплотняющие устройства, в которых используются пневматические шины для уплотнения нижележащей HMA.Ролики пневматических шин используют набор гладких (без протектора) шин на каждой оси; обычно четыре или пять на одной оси и пять или шесть на другой. Шины на передней оси совмещены с зазорами между шинами на задней оси, чтобы обеспечить полное и равномерное уплотнение по ширине катка. Усилие уплотнения контролируется изменением давления в шинах, которое обычно составляет от 60 до 120 фунтов на квадратный дюйм (TRB, 2000). В дополнение к статической сжимающей силе, ролики пневматических шин также развивают замешивающее действие между шинами, которое имеет тенденцию перераспределять агрегаты внутри HMA.Поскольку асфальтовое связующее больше прилипает к холодным шинам, чем к горячим шинам, область шины часто изолируется резиновым матом или фанерой для поддержания температуры, близкой к температуре мата во время катания (рисунки 8 и 9). Некоторые новые катки с пневматическими шинами могут быть оснащены вибрирующими или качающимися колесами.
Рисунки 8: Ролики пневматических шин
Рисунки 9: Ролики пневматических шин
Роликовые переменные
Есть несколько переменных, связанных с роликами, которые можно регулировать от задания к заданию, например:
- Последовательность и количество роликов.
- Скорость ролика.
- Количество роликов, проходящих по заданной площади мата.
- Место, в котором работает каждый ролик.
- Рисунок, используемый каждым валиком для уплотнения мата.
Не все эти переменные можно плавно регулировать, но, изменяя их комбинацию, можно разработать план прокатки, который оптимизирует уплотнение мата.
zp8497586rq
(PDF) Критерии приемки по степени уплотнения асфальтобетонного покрытия
7
4.Заключение и рекомендации
Что касается требований к степени уплотнения, изложенных в первом разделе, можно сказать
, что национальный стандарт TCVN 8819 и спецификация проекта не являются совместимыми документами.
В соответствии с Решением № 25/2005 QĐ / BGTVT от MOT, Техническая спецификация проекта
должна быть подготовлена в соответствии со списком применимых стандартов, утвержденных для проектов
, поэтому Спецификация проекта должна соответствовать TCVN 8819.Дело в том, что стандарт
определяет «коэффициент уплотнения слоя горячего асфальта не менее 0,98», в нем
не дается никаких рекомендаций о том, что следует делать, если коэффициент уплотнения немного ниже 0,98,
и то же самое. Спецификация проекта предусматривает любую концепцию корректировки цен для любого технически приемлемого диапазона
.
Анализ данных образцов из пакетов A1 и A7 показывает, что если K98 был установлен как «нокаут»
критериев, таких как абсолютное минимально допустимое значение, а именно любое значение меньше 0.98 должны быть отклонены
, большая часть (93% и 65% соответственно) площадок построенного покрытия в этих
упаковках должна быть удалена, что было бы невероятно катастрофическим для Проекта, так как это
серьезно повлияет на экономику. значение подрядчиков и ход реализации Проекта. В отличие от
, если K96 установлен в качестве контрольного показателя приемки, как указано в Спецификации проекта (Раздел
5200), почти 100% выполненных работ будут приняты, однако большая часть работ будет включена в предупреждение. область качества, которая характеризуется высокой пустотой и низким качеством, как
обсуждалось ранее.
Как указано в Разделе 01850 — «Приемка работ» в Спецификации, приемка работ
была разделена на 3 категории, а поверхность покрытия относится к Категории 3: «Элементы
, качество отделки которых может даже различаться. Контроль качества был проведен хорошо ». В такой ситуации применяется статистическая методология
с использованием коэффициента корректировки платежа, который уменьшает платеж
в зависимости от уровня допустимого отклонения от регулируемого уровня.К сожалению, при приемке
работ по асфальтобетонному покрытию корректировка оплаты применяется только к толщине слоя асфальта
и содержанию битума, но не по степени уплотнения. Дело в том, что контроль качества сильно зависит от степени уплотнения
, поэтому метод корректировки оплаты должен быть расширен до степени уплотнения
.
Для соответствия национальному стандарту TCVN 8819 и требованиям Министерства транспорта по качеству проекта
, в то же время для смягчения трудностей для подрядчиков, было рекомендовано следующее компромиссное решение
:
Установить K98 как желаемый минимум степени уплотнения в соответствии с TCVN 8819.
Установите K96 как абсолютный минимум для принятия / отклонения.
— Отклоняются участки со степенью уплотнения менее 0,96. Подрядчик должен снять
работы за свой счет.
— Участки со степенью уплотнения от 0,96 до 0,98 принимаются условно с
скорректированной оплатой по коэффициенту оплаты.
В частности, профиль платежа должен быть следующим:
— Категория 1: K> 98: 100% платеж.
— Категория 2: K96-K98: применяется коэффициент оплаты (PF).
— Категория 3: K <96: отклонить.
Общая сметная стоимость асфальтовых работ в рамках Проекта составляет приблизительно 2 334 миллиарда донгов (цена
с эскалацией). Если предположить, что качество всех пакетов аналогично пакету A1, а предел
категории 1 расширен до K97,5, чтобы учесть математически округленный эффект), тогда 85%
областей будут оплачены в соответствии с 2-я категория.Поскольку стандартное отклонение образцов составляет
статистически значимо мало, равномерность обеспечивается, поэтому коэффициент цены можно регулировать в диапазоне
K96-K97,5. Если предположить, что 2% от общего капитала дорожных покрытий дисконтируется по этой категории, то
составит 40 миллиардов донгов. Финансовые последствия этого довольно существенны, но, что более важно,
в рамках этой схемы будет способствовать контролю качества, поскольку подрядчики будут применять радикальные меры
для повышения степени уплотнения с помощью таких средств, как увеличение усилия уплотнения.
Тротуар 101: Уплотнение | Инженерно-технические консультанты
Есть много факторов, которые следует учитывать и учитывать при укладке нового горячего асфальта (HMA), будь то в новых или реабилитационных приложениях. Одним из таких факторов является УПЛОТНЕНИЕ нового асфальта. Уплотнение — это процесс уменьшения объема материала путем сжатия. В асфальтовом покрытии это достигается за счет
типов роликов, количества роликов, рисунков прокатки и температуры укладки материала.
Правильное уплотнение горячего асфальта приведет к уменьшению толщины материала примерно на 25% (1/4 дюйма на дюйм). Рекомендуется указывать толщину покрытия в качестве окончательной уплотненной толщины, а не «устанавливать X-количество дюймов асфальта».
Преимущества правильно уплотненного горячего асфальта заключаются в следующем.
- Соединение частиц асфальта вместе для уменьшения воздушных пустот, известное как уплотнение, для уменьшения проницаемости
- Повышенная прочность
- Долговечность материала
- Создание гладкой и однородной поверхности
Измеритель ядерной плотности для проверки готового покрытия для обеспечения надлежащего уплотнения.
Уплотнение дорожного покрытия достигается за счет использования механических вибрационных катков. Ролики движутся по дорожному покрытию при максимальной температуре, обычно от 240 ° F до 290 ° F, чтобы уплотнить или укрепить дорожное покрытие. Удерживая катки для дорожного покрытия в правильной схеме или зоне качения, можно достичь требований к целевой плотности уплотнения. Часто для достижения желаемых уровней уплотнения требуются ролики разного размера в зависимости от толщины дорожного покрытия.Также важно использовать поперечный валок при укладке асфальта, чтобы поддерживать однородность поверхности, особенно когда
мощение парковок и проездов. Идеальный диапазон уплотнения обычно составляет от 92% до 98% от теоретической плотности.
По мере укладки асфальтового покрытия существует несколько методов испытания асфальтового покрытия на уплотнение. Самый распространенный метод — это измеритель ядерной плотности. Датчик измеряет степень уплотнения при укладке дорожного покрытия. Таким образом, техник может сообщить оператору катка, если требуется дополнительное уплотнение.После укладки дорожного покрытия также могут быть выполнены образцы керна с лабораторным анализом для подтверждения уровней уплотнения. Рекомендуется провести испытания готового покрытия, чтобы убедиться, что материалы размещены в соответствии со спецификациями и отраслевыми стандартами.
Существует ряд проблем, которые могут возникнуть, когда не достигается надлежащее уплотнение.
- Чрезмерное уплотнение может привести к расслоению дорожного покрытия и его расслоению. Это может привести к преждевременным трещинам и разрушению.
- Недостаточное уплотнение может привести к растрескиванию дорожного покрытия.Это когда асфальтовая смесь начинает отделяться, и компоненты заполнителя отделяются от смеси. Это может привести к ослаблению покрытия, что приведет к преждевременному повреждению покрытия и общему сокращению продолжительности жизни.
Исправление неправильного уплотнения после укладки дорожного покрытия является очень сложным и дорогостоящим. В большинстве случаев тротуар необходимо удалить и заменить.
Целью уплотнения горячего асфальта является получение гладкого, структурно прочного, прочного и долговечного асфальтового покрытия.Если остались вопросы, обратитесь к профессиональному консультанту по дорожным покрытиям.
Автор: Рон Брукман
Консультант по дорожным покрытиям, инженерно-технические консультанты, Inc.
410-312-4761
Национальный центр технологии асфальта
Как заявил Р. Брюс Ноэль на ежегодном собрании Ассоциации технологов асфальтобетонных покрытий (AAPT) в 1977 году: «Самым важным строительным контролем, который обеспечит долгосрочную эксплуатационную надежность, является уплотнение.«Когда уплотнение увеличивается, можно оптимизировать плотность на месте, тем самым повышая долговечность и продлевая срок службы дорожного покрытия.
Обзор нескольких прошлых исследований ясно показывает влияние уменьшения воздушных пустот на улучшение утомляемости и колейности асфальтовых смесей как в лабораторных, так и в полевых условиях. В зависимости от типа смеси и эксперимента (который включал усталостные испытания изгибающей балки при постоянном напряжении и полевые результаты WesTrack) усталостные характеристики улучшились между 8,2 и 43.8% при уменьшении воздушных пустот на 1%. Аналогичным образом, на основе результатов колейности WesTrack и лабораторных испытаний числа потоков, сопротивление колейности улучшилось на 7,3–66,3% с уменьшением количества воздушных пустот на 1% в зависимости от типа смеси и анализа. Результаты недавнего исследования, проведенного Министерством транспорта Нью-Джерси, которое включало данные по 55 участкам дорожного покрытия, также предполагают, что уменьшение на 1% воздушных пустот на месте увеличивает срок службы асфальтовой смеси на 10%.
В целях иллюстрации рассмотрим эффект увеличения плотности асфальтового покрытия с 92 до 93%.Срок службы увеличится консервативно на 10%, а это означает, что наложение будет длиться 20 лет вместо 18. На рисунке 1 показан анализ стоимости жизненного цикла (LCCA) двух альтернатив с периодом анализа 20 лет.
Рисунок 1: Анализ стоимости жизненного цикла (на 1000 долларов США)
Для варианта 1 первоначальная стоимость строительства перекрытия, уплотненного до плотности 93%, предполагается, что она составляет 1 000 000 долларов. Предполагается, что стоимость обеспечения увеличения плотности на месте на 1% будет незначительной, поэтому для обеих альтернатив используется одна и та же начальная стоимость.В 20-м году наложение в альтернативе 1 будет заменено, таким образом, ликвидационная стоимость будет равна 0, а чистая приведенная стоимость (NPV) составит 1 000 000 долларов. Для альтернативы 2, в которой наложение уплотняется до плотности 92%, наложение будет заменено в 18-й год с будущими затратами в размере 1 000 000 долларов США. Новый оверлей (также предполагается, что он прослужит 18 лет) будет иметь оставшийся срок службы 16 лет в конце 20-летнего периода анализа и пропорциональную ликвидационную стоимость в размере 889 000 долларов. Стоимость замещения и ликвидационная стоимость дисконтируются до года 0 по реальной ставке дисконтирования 4%, в результате чего чистая приведенная стоимость для альтернативы 2 составляет 1 088 000 долларов.Таким образом, по проекту мощения стоимостью 1 000 000 долларов экономия затрат на чистую приведенную стоимость в размере 88 000 долларов (или 8,8%) будет достигнута просто за счет увеличения требуемой плотности на месте на 1%.
Поскольку плотность на месте является таким важным фактором, влияющим на долговременные эксплуатационные характеристики дорожного покрытия, она является ключевым фактором оплаты для принятия в большинстве штатов. Наиболее распространенный критерий минимальной плотности на месте составляет 92 процента от теоретического максимального удельного веса (G мм ). Большинство критериев плотности основаны на том, что могло быть достигнуто в прошлом, и не обязательно являются оптимальной плотностью на месте.В последние годы были достигнуты значительные успехи в проектировании и строительстве асфальта, что позволило добиться большей плотности.
Ролики пневматических шин используются на испытательном треке NCAT для достижения надлежащего уплотнения и плотности на месте.
Поскольку более высокая плотность на месте может привести к значительной экономии средств за счет увеличения срока службы дорожного покрытия, дорожные агентства могут рассмотреть возможность повышения требований к минимальной плотности. Более высокой плотности на месте можно достичь, следуя передовым методам и применяя новые технологии и методы.В качестве руководства по передовой практике недавно представленный веб-семинар под названием «Лучшие практики уплотнения» доступен для загрузки (бесплатно для членов NAPA) на store.asphaltpavement.org.
Технологии горячего асфальта (WMA), включая технологии вспенивания асфальта и химические и органические добавки, могут способствовать уплотнению. WMA улучшает удобоукладываемость асфальтового вяжущего и позволяет производить смеси при температурах на 25-90 ° F ниже, чем HMA. Обзор нескольких региональных исследований, сравнивающих качество смесей WMA и HMA, показал, что аналогичная плотность на месте может быть достигнута с WMA при значительно более низких температурах уплотнения.Использование WMA может привести к повышению плотности на месте для проектов с увеличенным временем транспортировки, а также для проектов в холодную погоду.
Интеллектуальное уплотнение (IC) — еще одна технология, которая может помочь улучшить плотность на месте. В системе IC вибрационные катки оснащены картографией на основе GPS, а также приборами, которые обеспечивают мониторинг уплотнения и жесткости материала в реальном времени. Это позволяет вносить необходимые корректировки для достижения оптимальной плотности и равномерного покрытия, устраняя ненужные проходы роликов и делая процесс более эффективным.Дополнительные элементы управления с обратной связью также могут непрерывно регулировать силу и частоту роликового барабана. IC — потенциально полезный инструмент для контроля качества, но он не заменяет приемочные испытания, поскольку взаимосвязь между измерениями жесткости IC и плотностью на месте несовместима.
Многие преждевременные разрушения покрытия вызваны низкой плотностью продольных стыков. Хорошо сконструированные продольные швы требуют очень пристального внимания к деталям в процессе укладки и уплотнения.Во время уплотнения первой полосы каток должен выступать за свободный край на шесть дюймов. При размещении соседней полосы должно быть перекрытие от одного до полутора дюймов, и очень важно, чтобы было достаточно материала (примерно 20% дополнительной толщины), чтобы обеспечить надлежащее уплотнение. Эта дорожка должна быть уплотнена с горячей стороны так, чтобы роликовый барабан выступал на шесть дюймов над стыком. В последние годы для улучшения продольных швов использовалось несколько других методов, в том числе использование конического или клинового соединения, которое также облегчает вертикальный переход между полосами движения во время строительства.Кроме того, существуют два метода, которые могут способствовать возникновению склеивания между холодным и горячим краями стыка: нанесение липкого покрытия на стык и использование инфракрасных обогревателей для повторного нагрева холодной кромки.
Незначительное увеличение плотности возможно и представляет собой рентабельное средство увеличения срока службы дорожного покрытия. Чтобы спецификации повышенной плотности имели максимальную пользу и эффективность, агентства должны учитывать следующее:
• Соответствующий выбор проекта . При выборе проектов для реализации более высоких требований к плотности на месте оцените базовое основание.Если основание слабое, добиться оптимального уплотнения будет сложно.
• Толщина подъема . Увеличение толщины подъема может повысить эффективность уплотнения, поскольку мат охлаждается медленнее, что дает больше времени для уплотнения. Кроме того, толщина подъема должна быть достаточной для переориентации частиц заполнителя во время уплотнения. Мелкодисперсные смеси должны иметь минимальную подъемную толщину, в три раза превышающую номинальный максимальный размер заполнителя (NMAS). Для крупнозернистых смесей минимальная толщина подъема должна в четыре раза превышать NMAS.
• Дизайн смеси . Соответствующее содержание связующего должно быть выбрано для желаемых воздушных пустот на месте. Градация, содержание связующего и объемные свойства, такие как воздушные пустоты и пустоты в минеральном заполнителе (VMA), могут влиять на уплотняемость смеси и должны тщательно контролироваться во время производства, чтобы минимизировать изменчивость.
• Критерии . Соответствующие меры уплотнения поля следует использовать для требований приемки. Сравнение плотности на месте с теоретической максимальной плотностью дает меньше возможностей для вариабельности уплотнения в полевых условиях, чем сравнение с плотностью лабораторных образцов.
• Поощрение за результат . Как показано в примере LCCA, плотность на месте оказывает значительное экономическое влияние на дорожные агентства. Таким образом, должны быть созданы стимулы для повышения эффективности уплотнения и достижения более высокой плотности на месте.
Этот обзор литературы, который поддерживает стратегическую директиву программы FHWA по технологии асфальтовых покрытий о продлении срока службы дорожного покрытия за счет улучшенного уплотнения, скоро будет доступен в виде отчета NCAT.
Асфальтобетон — обзор
6.6.2 Нестабильность
Асфальтобетонные покрытия по своей природе неоднородны и демонстрируют нестабильность (несовместимость), которая может иметь серьезные последствия для механических свойств дорожной асфальтовой смеси (Masad et al., 2009) . Градиенты свойств наиболее сильны по толщине слоев асфальтобетона. Основными источниками неоднородности (и нестабильности) являются (i) старение и (ii) изменение температурного профиля (Dave et al., 2010). Таким образом, термин долгосрочная стабильность относится к долговечности асфальта не только в его первоначальном виде, но и в виде цементов для асфальтовых покрытий. После нанесения асфальта в качестве асфальта для мощения он подвергается воздействию экстремальных условий окружающей среды: (i) высоких температур, особенно в южных регионах США, (ii) отрицательных температур, особенно в северных штатах США. , (iii) атмосферное излучение и (iv) механическое напряжение.Следовательно, необходимо учитывать потенциальные реологические проблемы, а также химические аспекты.
Асфальтены и полярные ароматические углеводороды играют фундаментальную роль в определении механических и реологических свойств битумов (индекса пенетрации (PI) и кинематической вязкости в зависимости от времени и температуры старения). Другие важные свойства асфальта, такие как коэффициент температурной восприимчивости и характеризующий фактор, зависели от количества асфальтенов и полярных ароматических углеводородов.Процедура отделения асфальта основана на растворимости в нормальном гептане с последующей адсорбционной хроматографией растворимой части (Speight, 1992a; Mohammed and Morshed, 2008; Speight, 2014).
Термин «старение» используется для описания явления упрочнения. Упрочнение в первую очередь связано с потерей летучих компонентов при старении асфальта во время эксплуатации. Этот фактор вызывает увеличение вязкости асфальта и повышение устойчивости. Кроме того, долговечность асфальта является основным фактором, влияющим на экономику асфальта при его усадке.Системы асфальтовых дорог представляют собой наиболее очевидную и, возможно, самую важную область, в которой наблюдаются характеристики асфальта. Затвердевание, которое происходит в асфальте в условиях эксплуатации, долгое время считалось лучшим показателем его экономической ценности.
Состав асфальта в значительной степени зависит от сырой нефти, из которой он был получен, и обычно основан на качественном определении четырех общих фракций, обнаруженных во всех асфальтах (Speight, 1992a, 2014). Каждая фракция значительно отличается по цвету, плотности и содержанию ароматического углерода.Таким образом, асфальт, отвечающий заданным характеристикам, представляет собой смесь этих количеств.
Асфальтеновые составляющие выделяются в виде фракции, которая нерастворима в низкомолекулярных парафиновых растворителях, таких как n -пентан или n -гептан, но растворима в ароматических растворителях — мальтены определяются как компоненты, растворимые в парафиновых растворителях. (Рисунок 6.2) (ASTM D893, ASTM D2007, ASTM D3279, ASTM D4124; Speight, 1992a, b, 1994, 2014, 2015a). Карбены нерастворимы в ароматических растворителях, но растворимы в четыреххлористом углероде или трихлорэтилене.Карбоиды не растворимы во всех растворителях, растворяющих асфальтены и карбены.
С точки зрения окисления и начала нестабильности, более полярные частицы в асфальте (т.е. компоненты смолы и асфальтена) будут окисляться первыми во время продувки воздухом. После предельного включения кислорода в структуре асфальтенов могут происходить значительные изменения, особенно в отношении включения полярного кислорода, который может влиять на молекулярную массу. Таким образом, изменение характера асфальта может быть не столько из-за окислительной деструкции, сколько из-за включения кислородных функций, которые нарушают естественный порядок внутримолекулярного структурирования.Существует вероятность того, что включение кислородных функций увеличивает способность асфальта связываться с заполнителем. Неконтролируемое введение кислородных функций может привести к производству низкосортного асфальта, в котором фазовое разделение окисленного асфальтена, возможно, уже произошло, или, если оно произойдет в продукте, результатом может быть разрушение дорожного покрытия из-за ослабления прочности. асфальт-агрегатные взаимодействия.
Хотя это не определено как свойство стабильности асфальта (поскольку оно измеряет снижение пенетрации, пластичности и увеличения вязкости), когда тонкий слой подвергается воздействию тепла и воздуха, образуется тонкая пленка, которая будет способствовать образованию кислородсодержащих продуктов полимеризации. .Это, в свою очередь, уменьшит проникновение асфальта (повысит его твердость), снизит его пластичность (сделает его более хрупким или менее эластичным) и увеличит его вязкость. Воздействие тепла и кислорода на устойчивый асфальт будет гораздо меньше. Существует прямая связь между результатами этого теста и изменениями исходных свойств асфальта во время транспортировки, хранения и использования.
Поскольку асфальт с некоторым правом считается коллоидной системой, природа этой системы будет определять реологические свойства асфальта, определяемые его пенетрацией, температурой размягчения, пластичностью и вязкостью при заданных температурах.На этом этапе стоит рассмотреть подход, применяемый к нестабильности / несовместимости тяжелых остаточных видов топлива и его потенциальное применение к асфальту (Speight, 1992a, b, 2014). Эта концепция основывает нестабильность / несовместимость на химическом составе, а также на внутренней коллоидной структуре (Por, 1992) путем определения индекса коллоидной нестабильности, который представляет собой отношение суммы асфальтеновых компонентов и насыщенных масел к сумме смол. и ароматические растворители:
CII = (Асфальтены + Насыщенные) / (Ароматические соединения + Смолы)
Равновесие хорошо пептизированной асфальтеновой системы, такой как асфальт, может быть легко нарушено (i) применением тепла во время эксплуатации в течение нескольких дней. чрезмерно высоких температур и / или трения автомобильных шин; (ii) окисление из-за постоянного воздействия воздуха; (iii) УФ-облучение при длительном воздействии солнечного света; и (iv) добавление парафинового разбавителя.В каждом случае изменяется химический состав и затрагивается ароматичность, вызывая нарушение равновесия коллоидной системы (Moschopedis and Speight, 1973, 1975, 1977, 1978; Speight, 1992a, b, 2014).
В результате частицы асфальтена лишаются своих обволакивающих слоев, которые ранее непрерывно сливались с последующими слоями. Система мицелл становится прерывистой, а ядра асфальтенов склонны к агломерации. Такой процесс приводит к нестабильности асфальта, что, возможно, приводит к фазовому разделению асфальтенов от асфальта, что приводит к потере взаимодействия асфальт-вяжущее.Результат — разрушение дорожного покрытия.
Другой оценкой реологических свойств является PI. Логарифм проникновения находится в линейной зависимости от температуры:
logpen = AT + K
В этом уравнении A — это наклон температурной чувствительности по отношению к логарифму проникновения. Путем экстраполяции на температуру размягчения получается проникновение приблизительно 800. Наклон A может быть получен путем измерения пенетрации при двух различных температурах или по соотношению проникновения и температуры точки размягчения.
PI можно получить следующим образом:
dlogpen / dt = (20 − PI) / (10 + PI) × 0,02A = dlogpen / dtPI = 10 × (2−50A) / (1 + 50A)
A PI, превышающий +2, будет указывать на гелевую структуру с эластичными свойствами и тиксотропную природу, тогда как PI ниже -2 укажет на структуру золя с ньютоновскими свойствами, тогда как асфальт, демонстрирующий удовлетворительные реологические свойства, должен иметь PI от +1 до — 1. После начальной деформации с определенной упругостью должны преобладать ньютоновские свойства с пропорциональностью между скоростью деформации и приложенным напряжением.Кривые над этими областями указывают на гелеобразный асфальт, а кривые под этими участками обозначают асфальт с зольной структурой.
Присутствие асфальта, осажденного пропаном, в асфальтовой смеси улучшает свойства устойчивости таких смесей из-за как реологической, так и химической природы асфальта, осажденного пропаном. Улучшенные свойства стабильности таких смесей можно увидеть по уменьшению различий в вязкости, проникновении и пластичности после воздействия повышенных температур и кислорода (например,г., в ТФОТ).
Благоприятное влияние асфальта, осажденного пропаном, ограничено их пропорциями — например, до 35% (об. / Об.) Осажденного пропаном асфальта в смесях с вакуумным остатком может быть верхним пределом, в зависимости от природа остатков в вакууме, а также природа и пропорции других компонентов, таких как, например, экстракты смазочного масла, которые иногда используются в таких смесях (Ishai et al., 1988).
Это указывает на то, что долговременная стабильность асфальта связана с основными реологическими и физико-химическими характеристиками исходного, а также выдержанного образца асфальта различного состава.Также считается (Ishai et al., 1988), что понимание взаимосвязи этих характеристик со свойствами асфальта (асфальтобетонного покрытия) позволяет прогнозировать характеристики долговечности асфальта в полевых условиях, а также прогнозировать другие соответствующие свойства (Mohammed and Eweed, 2012). В этом случае на стабильность указывают индексы старения: отношения вязкости и температуры размягчения, а также процент остаточного проникновения до и после воздействия TFOT (Por, 1992).
Наконец, последствия загрязнения остатка частиц во время перегонки или остатка висбрекинга (также называемого гудроном висбрекинга ) (Speight, 2014, 2015b) могут иметь серьезные последствия для эксплуатационных характеристик асфальта. Если для производства асфальта используется загрязненный твердыми частицами остаток или смола висбрекинга, в результате получается асфальт плохого качества (более подходящий в качестве асфальта для стоянок), который будет стоить гораздо ниже, чем дорожное покрытие хорошего качества (без частиц) асфальт.
Новая радиоволновая технология оценивает целостность асфальта
Информация в реальном времени о плотности и однородности асфальта может повысить качество строительства — * Роджер Робертс, 8095 GSSIПравильно утрамбованный асфальт является основным фактором срока службы дороги, так как неадекватно уплотненный асфальт разрушается на более высокая скорость, чем правильно уплотненный материал. Ежегодно на строительство и ремонт дорог тратятся миллиарды, поэтому крайне необходимо найти новые технологии, которые могут обеспечить целостность асфальта на новых дорогах с твердым покрытием.Теперь доступна новая радиоволновая технология для неразрушающего определения плотности асфальта во время нанесения.
Содержание воздушных пустот в асфальте варьируется в зависимости от степени уплотнения во время укладки асфальта и изменений в составе асфальтовой смеси. Асфальт со слишком большим количеством воздушных пустот (часто считается, что они превышают 8%) разрушается более быстрыми темпами. Слишком мало воздушных пустот (менее 3%) возникает из-за чрезмерно уплотненного асфальта, что также нежелательно.
В любом случае асфальт подвержен преждевременному разрушению, и срок службы дороги меньше, чем у асфальта с оптимальным содержанием воздушных пустот.
Инженеры-строители ищут оптимальное место для уплотнения асфальта при его укладке. Обычно они оценивают асфальт путем измерения изменений плотности, которые можно использовать для расчета содержания пустот в воздухе.
Для обеспечения оптимального уплотнения асфальт во время укладки должен выдерживаться в определенном температурном диапазоне. Если асфальтоукладчик и транспортные средства не справляются с поддержанием однородного горячего материала, могут образовываться участки с холодными пятнами.Когда валик используется на участках за пределами оптимального диапазона температур, он не может должным образом уплотнять материал. Например, такие «холодные пятна» могут возникнуть, если асфальтоукладчик заправляется из концевых самосвалов, которые охлаждают асфальт ближе к металлическим бокам и торцу грузовика больше, чем в середине. Некоторые дороги с плохим покрытием имеют регулярные дефекты, связанные с заправкой грузовых самосвалов.
Возможно, сначала эти области не удастся заметить, но, скорее всего, они станут очевидными позже.На самом деле, есть много дорог, на которых через каждые несколько сотен метров можно наблюдать холодное пятно, которое начинает ухудшаться, превращаясь в неровный участок дороги. Если рабочая бригада не обнаружит проблему во время асфальтирования, возможно, потребуется заменить дорогу гораздо раньше, чем если бы материал был нанесен должным образом.
Другая проблема уплотнения возникает, когда установленная схема прокатки не соблюдается должным образом. Схема прокатки относится к количеству раз, скорости и нахлестке, которые ролики должны использовать при прокатке нового асфальта для достижения оптимального уплотнения.Если асфальтоукладчики пропускают участок и не уплотняют материал с помощью необходимого количества валков, они могут создать участки, где уплотнение не будет выполнено.
Выявление и исправление любых проблем с рисунком прокатки в течение первых нескольких дней работы по укладке дорожного покрытия выгодно как владельцу, так и подрядчику, поскольку в спецификации контракта могут быть включены требования о том, как укладывается асфальт с точки зрения приемлемого содержания пустот. Контракты могут также включать бонус за попадание в конкретный диапазон пустого содержимого асфальта или штраф, если бригада выходит за пределы указанного диапазона пустого содержимого.
Существует несколько доступных методов, которые можно использовать для измерения вариаций плотности асфальта, которые затем используются для расчета вариаций пустотного содержания. Одним из методов неразрушающего контроля (NDT) является датчик ядерной плотности, который состоит из источника излучения, испускающего облако частиц, и датчика, который подсчитывает полученные частицы, которые рассеиваются исследуемым материалом. Вычисляя процент частиц, которые возвращаются в датчик, датчик может быть откалиброван для измерения плотности и внутренней структуры исследуемого материала.
Ядерный манометр довольно точен, но имеет несколько недостатков. Датчик помещается на асфальт, и измерения проводятся в течение определенного периода времени, обычно несколько минут или меньше. Метод требует контакта с устройством, которое должно оставаться неподвижным в точке измерения. Из-за продолжительности времени, необходимого для измерения, ядерные манометрические измерения проводятся редко. Сбор только этих точечных измерений не позволяет адекватно охватить всю изменчивость асфальта.
Кроме того, поскольку в нем используется радиоактивный материал, ядерный манометр требует обучения пользователя и безопасного хранения. Также существуют особые требования к транспортировке. Стоимость повторного лицензирования, обслуживания и повторной калибровки может составлять около 2000 долларов США в год.
Подобно ядерному датчику, неядерный датчик плотности измеряет электрический импеданс; Затем выполняется процедура калибровки, чтобы соотнести его с плотностью. Подобно датчику ядерной плотности, этот метод весьма ограничен, поскольку он измеряет только очень маленькие части асфальта.
Поскольку ядерные и неядерные плотномеры могут собирать только одно значение на большой площади, они не могут уловить все вариации содержания пустот, которые могут быть важны для обеспечения качественной укладки.
Другой вариант неразрушающего контроля — использование радиоволн, которые можно использовать для получения измерений в реальном времени на большой полосе дорожного покрытия за короткие промежутки времени. Отражения радиоволн от асфальта можно использовать для прямого расчета значений диэлектрической проницаемости асфальта, которые затем соотносятся с пустотностью нового покрытия, что является относительным показателем плотности.
Еще один метод, о котором следует упомянуть, — это удаление керна, когда керн извлекается из асфальта, чтобы можно было измерить его свойства. Удаление керна используется в качестве основного метода оценки уплотнения асфальта и используется в качестве резервной копии для измерений с помощью других методов. Удаление керна проводится на ограниченной основе, поэтому оно часто не отражает истинную изменчивость содержания пустот в асфальте.
Первоначальная взаимосвязь между содержанием пустот и состоянием дороги была известна давно.В конце 1990-х исследователи из Техасского транспортного института (TTI) обнаружили взаимосвязь между диэлектрической проницаемостью, рассчитанной с помощью георадара (GPR), конкретным применением радиоволн и пустотами.
Позже исследователи разработали рабочую методологию использования инфракрасных и радиоволновых технологий для улучшения оценки качества асфальтовой смеси и уплотнения. Затем они искали способ коммерциализировать его, чтобы его могли легко использовать государственные департаменты транспорта.
Раньше использование георадара требовало специального оборудования, большого объема интерпретации данных и ряда ручных операций. В 2013 году TTI начала работать с GSSI над упаковкой компонентов устройства в модернизированное и удобное для оператора устройство, которое обеспечило бы профилирование однородности асфальтовой смеси в режиме реального времени. Работа была выполнена в рамках программы стратегических исследований автомобильных дорог Федерального управления шоссейных дорог (SHRP 2).
В течение следующих нескольких лет GSSI разработала технологию PaveScan RDM, которую компания TTI использовала в нескольких пилотных исследованиях.В бесконтактной технологии PaveScan используется датчик, который обычно выдает результат измерения через каждые полфута вдоль полосы движения, поэтому данные за милю включают примерно 10 000 измерений для каждого используемого датчика.
Компания TTI обнаружила, что новая система PaveScan преодолевает трудности, связанные с оборудованием, обработкой данных и квалификацией персонала, которые существовали в прошлом. Согласно TTI, «применение георадара было реализовано во всех пилотных проектах, где результаты радаров давали количественную оценку плотности и однородности.
GSSI позже разработала трехканальную систему, которая может быть установлена на транспортном средстве для получения измерений содержания движущихся пустот за один проход, охватывая оба пути колес и пути между колесами. Один датчик расположен на одном колесном пути, один посередине и один на другом колесном пути, поэтому для каждого полуметра вдоль пройденной полосы выводятся три измерения. Таким образом, объем данных на милю включает примерно 30 000 измерений, которые собираются всего за 20 минут.