виды машин для пластмассы, принцип работы
Развитие технического прогресса привело к появлению различных технологий, которые позволяют производить изделия, отличающиеся улучшенными эксплуатационными характеристиками. Одной из востребованных в настоящий момент является экструзия. Собой она представляет технологический процесс переработки пластмасс, из которых изготавливают разнообразные детали, а также производят различную профильную продукцию.
Сама технология состоит в приготовлении сплава из полимерных материалов с последующим его продавливанием через специальные насадки, которые придают ему определенную форму. Основным элементом линии по производству изделий из пластика является экструдер.
Принцип действия и конструкция
Технологический процесс экструзии является сложным физико-химическим процессом, на который оказывают воздействие механические усилия в условиях высокой температуры и влаги. Нагрев продуктов переработки происходит благодаря тому, что возникающая при борьбе с внутренним трением, а также при пластических деформациях механическая энергия превращается в тепло.
В процессе экструзионной обработки существует несколько сменных параметров. К числу наиболее важных следует отнести:
- состав сырья;
- влажность;
- его природа.
При протекании экструзионного технологического процесса может происходить изменение:
- температуры материала;
- давления;
- интенсивности и длительности воздействия на исходное сырье.
Принцип работы экструдера
Само по себе такое оборудование представляет электромеханическое устройство, основным предназначением которого является осуществление процесса формовки профильных деталей из пластика или его полуфабрикатов
- корпус системы нагрева полимерных материалов. В качестве основного источника тепловой энергии при осуществлении этого технологического процесса могут выступать обычные резистивные или индукционные системы. При использовании последних возникновение высоких температур происходит за счёт наведения на корпус высокочастотных индукционных токов Фуко;
- узел нагрузки. Через этот элемент в полость корпуса различными способами поступает исходное сырье;
- экструзионная головка. По-другому специалисты называют ее фильерой. Именно она обеспечивает форму изделий, которая получается по завершении технологического процесса;
- механический привод
- система контроля и управления. Благодаря ей обеспечивается поддержание необходимого технологического режима.
В качестве исходного материала обычно выступают гранулы и порошок. Они загружаются в оборудование, а далее под действием рабочего органа происходит их перемещение в рабочую зону корпуса. Там под воздействием давления, силы трения и температуры подаваемое извне исходное сырье нагревается, а в процессе его плавления возникает состояние, которое требуется по условиям технологического процесса.
Во время движения исходного сырья в полости корпуса происходит его тщательное перемешивание до состояния однородной гомогенизированной массы.
В условиях высокого давления происходит продавливание расплава при помощи формующих головок и сетчатых фильтров. В результате обеспечивается окончательная гомогенизация и придание материалу заданного профиля.
После этого материал естественным образом охлаждается или же применяется принудительный способ с последующей полимеризацией. В конечном итоге получаются изделия, имеющие необходимую конфигурацию и обладающие заданными механическими и физическими свойствами.
Виды экструдеров
Современные модели экструзионных установок могут различаться между собой как конструкцией рабочего органа, так и назначением.
Одношнековый
Среди всех разновидностей экструзионного оборудования наиболее распространенным является шнековое. Такие машины удовлетворяют всем требованиям экструзионного процесса. В этих агрегатах в качестве основного рабочего органа применяется шнек. Специалисты называют его винтом Архимеда. Многие прекрасно знают этот рабочий элемент по домашним мясорубкам.
При использовании экструдера для производства изделий из пластмассы лопасть шнека захватывает сырье в зоне загрузки, а далее происходит его последовательное перемещение по всей длине цилиндра корпуса, начиная от зоны нагрева через участок гомогенизации и формовки. В зависимости от особенностей технологической карты, которую имеет оборудование, а также вида используемого для производства изделий исходного сырья шнеки могут предусматривать несколько вариантов исполнения — конические, цилиндрические и нормальные быстроходные.
Также могут использоваться шнеки, которые сужаются к выходу. Для этого оборудования в качестве главного параметра специалисты рассматривают соотношение рабочего диаметра шнека и его длины. Также различаются шнеки по шагу витков и их глубине.
Главный недостаток одношнекового экструдера заключается в том, что не всегда имеется возможность для их применения. Например, если в качестве исходного сырья выступают порошковые полуфабрикаты, то наличие одного винта в составе оборудования не позволяет справиться с перемешиванием массы в процессе ее расплавления и последующей гомогенизации. В таких случаях выбор делают в пользу двухшнековых экструдеров.
Двухшнековый
Особенность этого оборудования состоит в том, что в нём винты сцеплены между собой. Поэтому при использовании таких экструдеров имеется возможность совершения шнеками параллельных и встречных вращательных движений. Эти рабочие части оборудования могут быть прямыми или коническими.
Использование подобных машин приводит к тому, что в процессе разогрева исходного сырья его смешивание и гомогенизация осуществляется более тщательно. В конечном итоге на головку для формования изделий поступает однородная и дегазированная масса.
Необходимо отметить следующий момент: в отдельных технологических процессах могут использоваться экструдеры, имеющие большее количество шнеков — до 4. Помимо этого нередко применяется планетарный автомат, когда число шнеков, вращающихся вокруг центрального винта, доходит до 20.
Необходимость в применении такого оборудования возникает при использовании в качестве исходного сырья отдельных видов пластиков, которые в условиях воздействия высоких температур имеют склонность к разрушению. Говоря другими словами, могут лишаться своих основных физических качеств. Таким образом, использование подобных экструдеров обеспечивает нагрев сырья за счет силы трения и высокого давления.
Производство ПВХ-профилей
В настоящий момент востребованным видом изделий являются пластиковые и композитные профили. В большинстве случаев производители изготавливают их, используя метод экструзии. Для изготовления такой продукции в зависимости от применяемого материала, а также сложности и формы изделия задействуются одно- или двухшнековые аппараты, которые имеют соответствующие формовочные головки.
Ассортимент выпускаемых с использованием экструдеров изделий довольно широкий, начиная от тонких нитей и полос и заканчивая листами крупных панелей, которые имеют профиль сложной геометрии. Пластиковые окна и двери, выпускаемые сегодня многими компаниями, собираются с использованием именно ПВХ-профилей, которые изготовлены на экструзионном оборудовании.
При производстве ПВХ-профилей многие производители добавляют в полимерный состав специальные компоненты, что дает возможность изготовления сложных композитов. Например, сегодня многие производители выпускают дерево-пластиковые изделия, которые довольно часто используются для изготовления разных строительных конструкций.
Изготовление труб
В такой сфере, как производство трубных изделий важным условием является отсутствие пузырьков газа в гомогенизированной смеси. По этой причине экструдеры, которые задействуются при производстве такой продукции, производители оснащают системами дегазации. В большинстве случаев применяются шнековые установки. Помимо прочего используют барьерные шнеки, благодаря которым обеспечивается надежное разделение твердого полуфабриката от полностью расплавленного. За счет этого достигается сохранение однородности состава, что положительным образом отражается на качестве выпускаемой трубной продукции и её эксплуатационных характеристиках.
Экструдеры для полиэтилена
Все плёнки, изготовленные из полимерных материалов, производятся компаниями исключительно с использованием способа экструзии. Для производства подобной продукции применяется выдувной экструдер. У оборудования, используемого для производства стрейч-пленки, формовочный узел может иметь вид узкой щели. При применении такого оборудования на выходе получается однослойная пленка, которая имеет необходимые параметры толщины и ширины.
В отдельных моделях могут использоваться круглые щелевые фильеры большого диаметра. При использовании мини-экструдеров можно получить пленку с шириной рукава до 300 мм и с параметром толщины 600 мкм. Такие устройства обладают компактными размерами, что обеспечивает возможность их установки даже в небольшом по площади помещении.
Экструзионные линии
В условиях промышленных предприятий экструзионное оборудование следует рассматривать в качестве главного компонента линии по осуществлению этого процесса. Помимо основного оборудования — экструдера она включает и целый набор других механизмов и устройств:
- намоточные и отрезочные механизмы. Они используются для приведения изделий в необходимый для складского хранения и транспортировки вид;
- маркирующие и ламинирующие системы различного принципа действия;
- механизмы протяжки готовых профилей;
- система охлаждения. Её установка выполняется на выходе экструдера, чтобы повысить скорость процесса полимеризации готовых изделий. Эти системы могут быть различного типа — воздушные или в виде охлаждающей ванны;
- система подготовки и загрузки сырья. В отдельных случаях полуфабрикат необходимо предварительно подвергнуть процедуре просушивания и последующей калибровке перед тем, как подавать его в загрузочный бункер.
В составе оборудования могут использоваться и другие механизмы, а также применяться технологические устройства для автоматизации непрерывного процесса производства.
Подводя итоги
Экструзионная технология является довольно популярной в настоящее время. Ее используют при производстве различных изделий. В основном она применяется для изготовления продукции из пластика. Знакомые каждому в нашей стране пластиковые окна и двери изготавливают с использованием этого процесса. Для производства продукции используется такой прибор, как экструдер. Это оборудование отличается несложным устройством, поэтому изготовить экструдер для пластика своими руками — вполне осуществимая задача.
Особенность этого процесса заключается в предварительном подогреве сырья, которое потом подвергается процедуре плавления в условиях определенного температурного режима и давления. Далее полимерная масса продавливается через формовочные насадки, что и позволяет получить изделия с нужными физическими и качественными характеристиками.
Устройство для литья пластика (экструдер)


В этой статье рассмотрим, как изготовить экструдер. Но сначала давайте, что такое экструдер и экструзия.
Экструдер — это машина для непрерывной переработки полимерного сырья в однородный расплав и придания ему формы путём продавливания через экструзионную головку и специальное калибрующее устройство.
Экструзия (технологический процесс) — метод и процесс получения изделий из полимерных материалов путём продавливания расплава материала через формующее отверстие в экструдере.
Говоря простым языком, в камере устройства пластмасса расплавляется и под давлением выдавливается через сопло головки в пресс-форму.
Инструменты и материалы:
-Металлическая труба с резьбой на конце;
-Головка торцевая;
-Удлинитель для головки;
-Сварочный аппарат;
-УШМ;
-Тиски;
-Напильник;
-Перфорированный уголок;
-Два уголка-кронштейна;
-Медная трубка;
-Крепеж;
-Металлический хомут;
-Нагревательный элемент;
-Терморегулятор с датчиком;
-Стекловолокно;
-Алюминиевый скотч;
-Фитинги;
-Металлическая полоса;
-Угольник;
-Дрель;
Шаг первый: поршень
Камеру экструдера будет из металлической трубы 20 мм. Внутренняя стенка трубы должна быть ровная без шва. Внутрь камеры будет закладываться пластик, нагреваться и выдавливаться через сопло. Для выдавливания нужен поршень. Поршень мастер изготовил из торцевой головки. Подобрал головку по диаметру трубки. Установил ее на удлинитель. Приварил головку к удлинителю. Заварил торцевое отверстие головки.

Шаг второй: камера
На одном конце трубы имеется резьба. На противоположном конце делает загрузочное окно. Размечает и вырезает стенку трубы. Зачищает края напильником. Через прорезь будет загружаться пластик в камеру.
На резьбу накручивает переходную муфту.
Шаг третий: нагревательный элемент
Теперь нужно установить на камере нагревательный элемент. Мастер использует два нагревательных элемента по 400 Вт. Из перфорированного уголка делает крепление. Закрепляет нагреватели металлическими хомутами. Между уголками устанавливается медная трубка. В трубку устанавливается термодатчик.
Шаг четвертый: термоизоляция
Обматывает устройство стекловолокном. Поверх стекловолокна наматывает металлический скотч. Термоизоляция предотвратит потери тепла и защитит от случайного прикосновения.

Шаг пятый: установка
Из уголка мастер сделал рамку для крепления экструдера. Закрепил устройство на раме.


Шаг шестой: сопло
Роль сопла в экструдере играет латунный переходник. Вкручивает переходник.
Шаг седьмой: рычаг
Теперь нужно изготовить рычаг. Сначала мастер удлиняет толкатель поршня.
Закрепляет уголки на раме. К уголкам крепит поперечную трубу. К поперечине присоединяет трубу с прорезью. Берет еще один отрезок трубы. Один конец сплющивает (он крепиться в прорези предыдущего элемента), второй конец соединяет со штоком поршня. Все соединения подвижные.
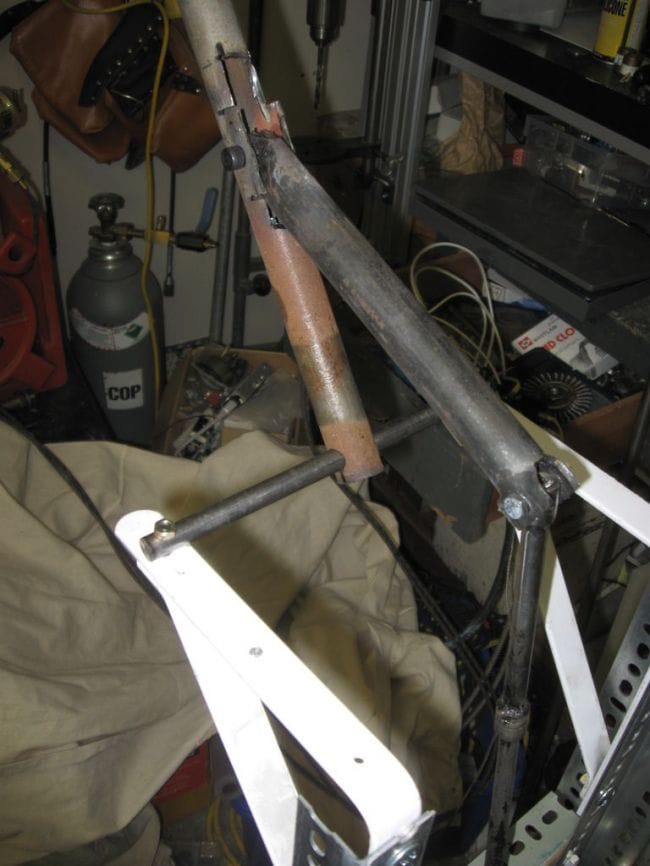
Шаг восьмой: испытание аппарата
Сначала нужно прогреть камеру выше температуры плавления пластика на 2-3 градуса. Затем загрузить измельченный пластик в камеру. Небольшое наличие дыма в начале — это нормально, если дыма много и он идет постоянно нужно снизить температуру.
Работать с экструдером необходимо в хорошо проветриваемом помещении, используя средства защиты.
Источник
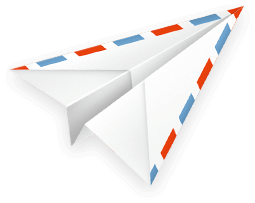
Получайте на почту подборку новых самоделок. Никакого спама, только полезные идеи!
*Заполняя форму вы соглашаетесь на обработку персональных данных
Становитесь автором сайта, публикуйте собственные статьи, описания самоделок с оплатой за текст. Подробнее здесь.Готовим экструдер правильно
Заметка об direct-drive экструдерах.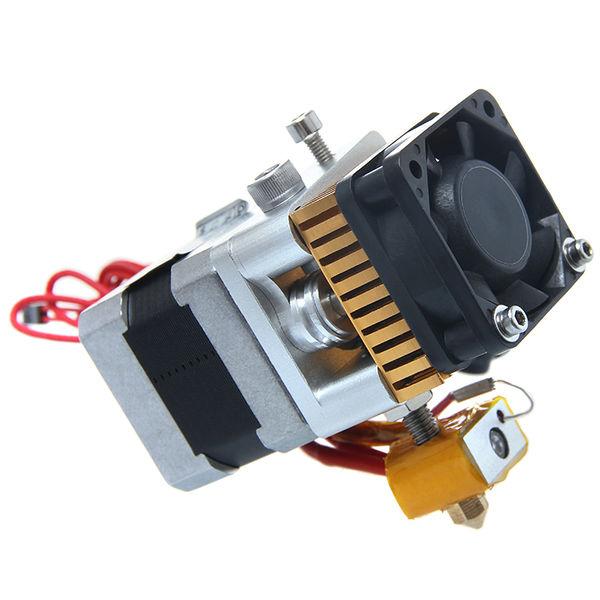
1) Вязкость расплава пластика в сопле. Если пластик только-только начал переходить из твердого состояния в жидкое он больше похож на пластилин, самостоятельно никуда не течет. Если температуру поднять — пластик ставится менее вязким и может под действием гравитации вытекать из сопла. Если температуру поднять еще выше — пластик начнет разлагаться на составляющие и неприятно пахнуть. Обычно стараются печатать при минимальной температуре.
2) Диаметр сопла. Чем меньше сопло тем больше усилий нужно чтобы протолкнуть через него пластик.
3) Силы трения в канале между соплом и механизмом подачи прутка. Этот канал называется термо-барьер. Часто в китайских экструдерах термобарьер представляет собой цельнометаллическую втулку. Чтобы уменьшить силы трения в термобарьер вставляют фоторпластовую трубку, именно такие термобарьеры нас должны интересовать. Убедитесь что у Вас именно такой.
[IMG ID=69819 WIDTH=219 HEIGHT=220]
4) Сила с которой нужно протолкнуть пластик между зубчатой шестерней экструдера и прижимным роликом. Если сильно закрутить регулировочный винт на экструдере, то гарантировано не будет проскальзывания прутка, но при этом часть мощности мотора будет тратится чтобы протолкнуть пластик между зубчатой шестерней и прижимным роликом. Если же прижимной силы будет недостаточно, экструдер будет крутится вхолостую и грызть пруток.
Но самый главный в экструдере конечно же шаговый двигатель, именно от его мощности зависит — пройдет пластик или не пройдет.
Если Вы как и я печатаете мелкие детали, соплом 0.3мм или 0.2мм, то нам нужен мотор который будет одновременно и мощным и точным, чтобы можно было печатать слоями 0.05мм и даже 0.02мм. Обычный шаговик не подойдет потому что силы его микрошага будет недостаточно чтобы продавить пластик. Так что, мой выбор пал на шаговик с 400 шагами на один оборот от компании Wantai (вместо 200 у обычных 1.8 градусных шаговиков). Согласно даташиту он развивает усилие 4.8 Кг на см. Хотя как по мне — врут китайцы, скорее всего там 4.2 Кг, во всяком случае продавцы чаще указывают 4.2Кг. 42BYGHM809[IMG ID=69821 WIDTH=292 HEIGHT=292]С ним печать ABS слоем 0.05 выглядит вот так:
[IMG ID=69817 WIDTH=407 HEIGHT=306]
Слой 0.02 ложится так же, но в игру уже вступает качество пластика.
Казалось бы на этом и все, и я ничего нового не сказал ? Я тоже так думал: указанный выше мотор и экструдер, термобарьер с фотораплостовой втулкой, отрегулировал прижим и температуру, но не взлетело. При печати соплом 0.2мм экструдер стучал — пришлось повысить температуру, но и это не спасло и реальность слоем 0.1мм на скорости 30мм/с была жестока:
[IMG ID=69818 WIDTH=390 HEIGHT=435]
Слои ложатся с нахлестом, отчетливо видны диагональные линии. Ситуацию спасало если печатать очень медленно (15мм/с и ниже). Что же не так ?
Оказалось, проблема в одной неприметной маленькой детальке.
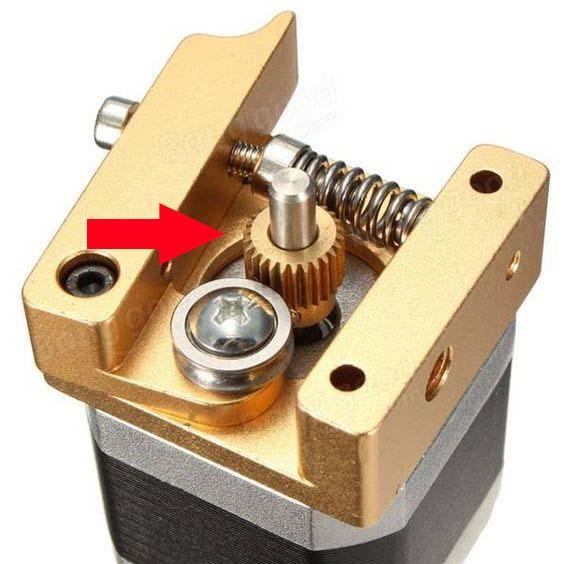

Если же усилие надо больше, то мотор работает с пропусками и график подачи пластика уже вот такой (пропуск микрошагов):

Ну а если печатаем первый слой, который мы хотим ‘вмазать’ в платформу для лучшей адгезии, мотор начинает пропускать шаги и стучать:

Решением данной проблемы простое, нужно шестерню у которой диаметр как можно меньше. Собственно это и есть последний важный ингредиент для хорошего экструдера. С шестерней MK8 от экструдера можно получить расчетные параметры по мощности и давлению.
[IMG ID=69827 WIDTH=225 HEIGHT=223]
Результаты тестирования:

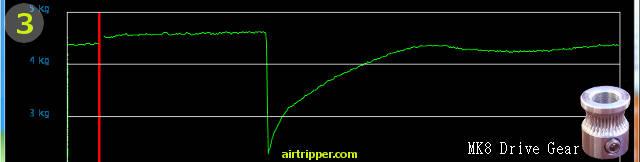
Теперь у нас есть все ингредиенты для хорошего экструдера, перечислю: мощный мотор повышенной точности (0.9 градусов на 1 шаг), термобарьер с фторопластовой втулкой, шестерня MK8, оптимально отрегулирован прижим ролика и выставлена правильная температура, а для быстрой печати — поставлено сопло большого диаметра.
В статье использованы графики из исследования. Оригинал здесь. http://airtripper.com/1676/3d-printer-extruder-filament-drive-gear-review-benchmark/П.С. Есть и другие варианты как повысить усилие и равномерность проталкивания пластика экструдером, чаще всего это повышение мощности двигателя с помощью редуктора, но стоимость растет уже в разы.
Экструдер для переработки пластика своими руками
Всем привет !Нужны советы по созданию экструдера, для переработки пластика
Печатаю много такого
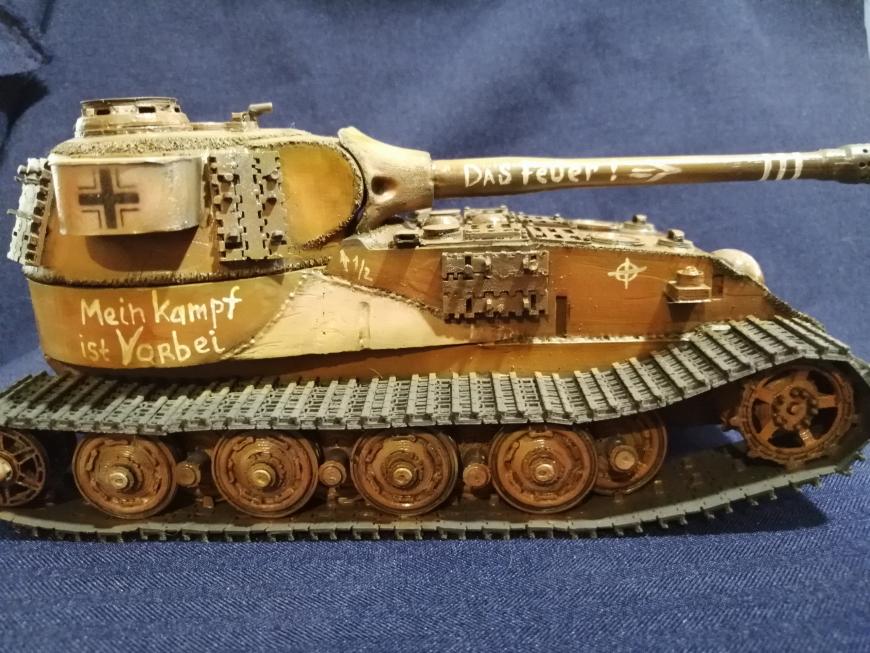

Остается брак и поддержки , хотелось бы и их пустить в дело !
Начну с того что имею на данный момент:
— Доступа к сварочному аппарату у меня нет , использую то что можно купить в магазине и на Алиэкспрес
1) кусок трубы с резьбой + нагревательный элемент + заглушка (в заглушке резьба под сопло от 3д принтера с отверстием 1,7 мм) для универсальности процесса
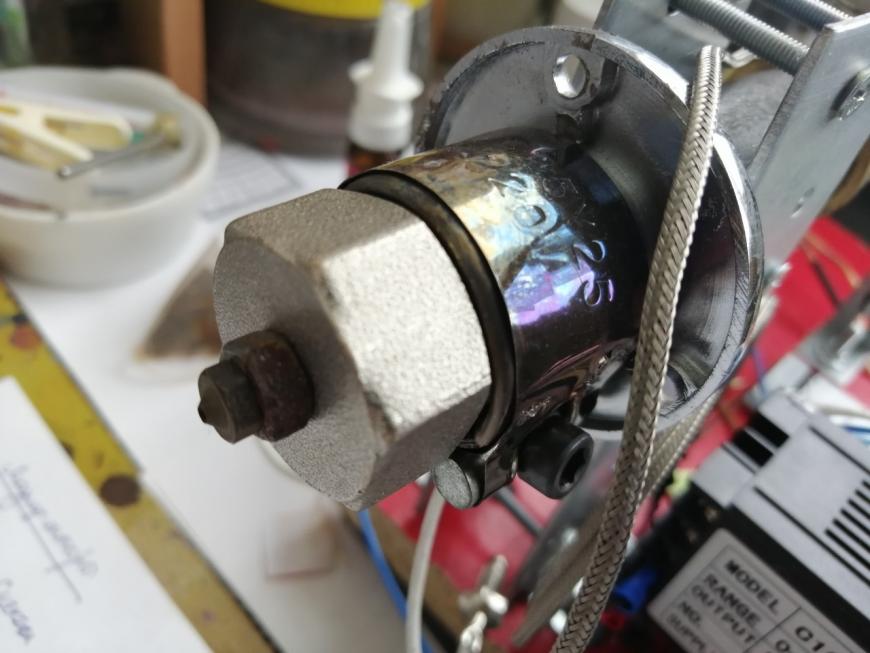
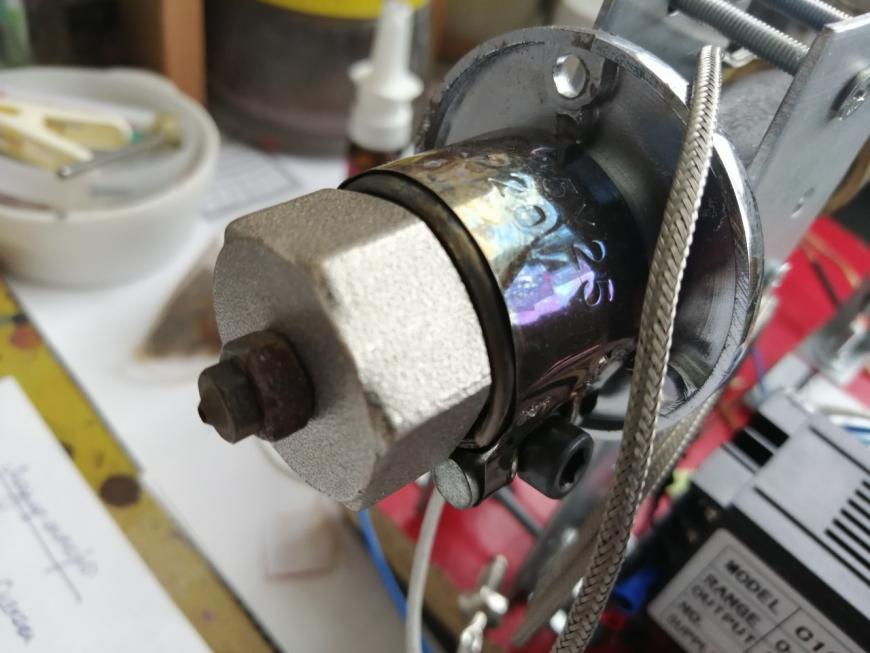
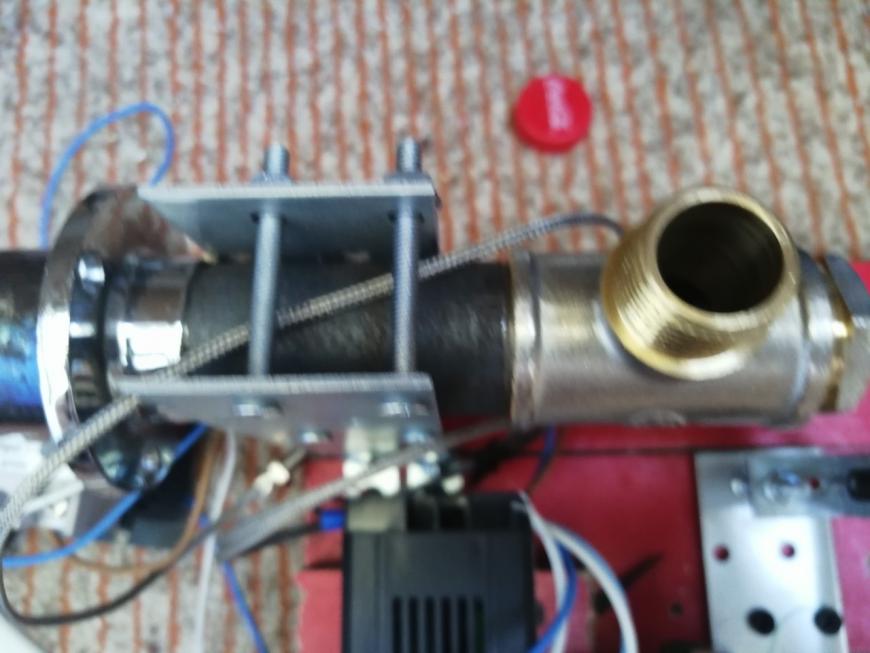

Нагреватель (в комплекте 2 , но 1 я угробил )
http://ali.pub/3ees1i
Заказал еще такой вариант
http://ali.pub/3ees8p
Мозги нагрева + термопара + реле
http://ali.pub/3eesd6
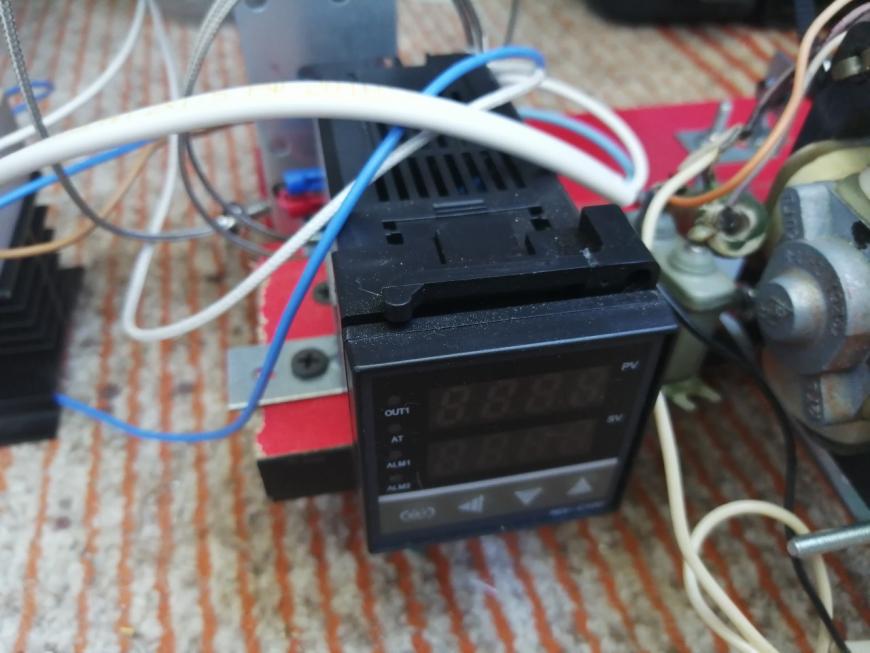
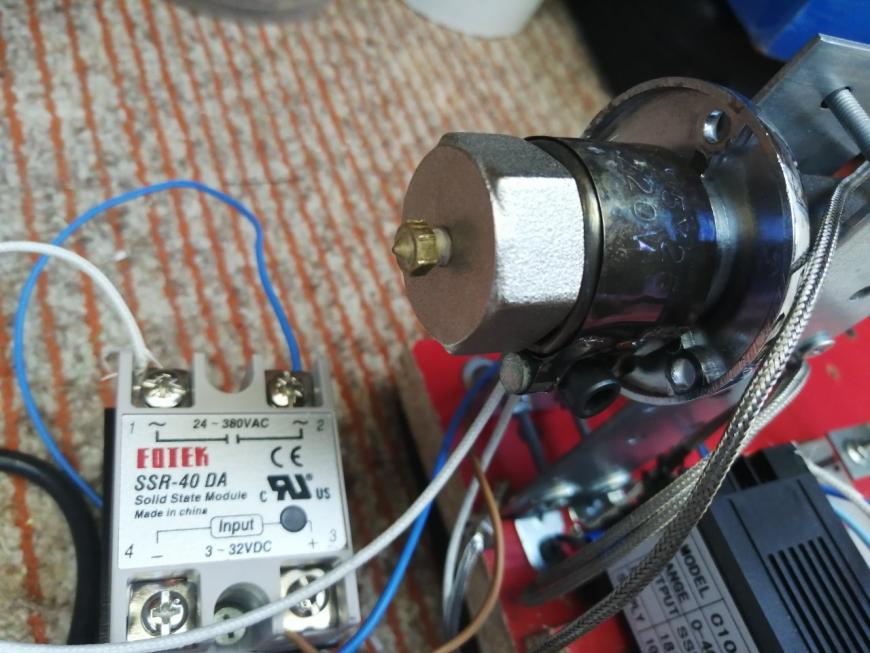
— В ходе экспериментов оказалось что 1 нагревательный элемент мало , 2 много … Во общем минимум 2 , иначе провернуть шнек (сверло ) становиться тяжело во всех смыслах.
выход пластика нормальный, шнек крутил руками, качество пластика … ну неплохое , ожидал хрупкость и ломкость , но получилось что то похожее на PLA , хотя перерабатывал ABS.
************
А теперь к главному
По задумке вращать шнек должен двигатель (от старого патифона) но силы ему явно не хватает
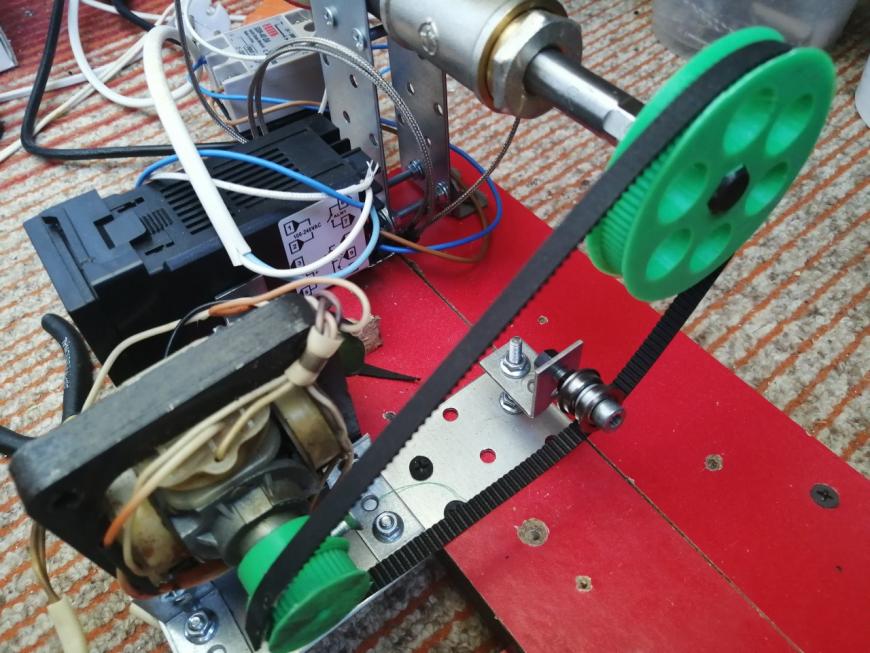
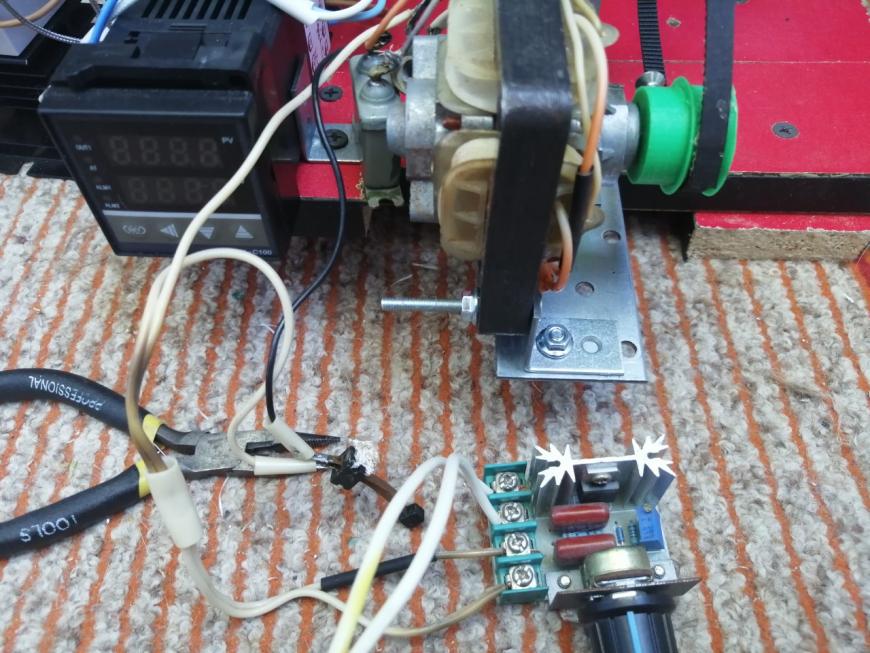
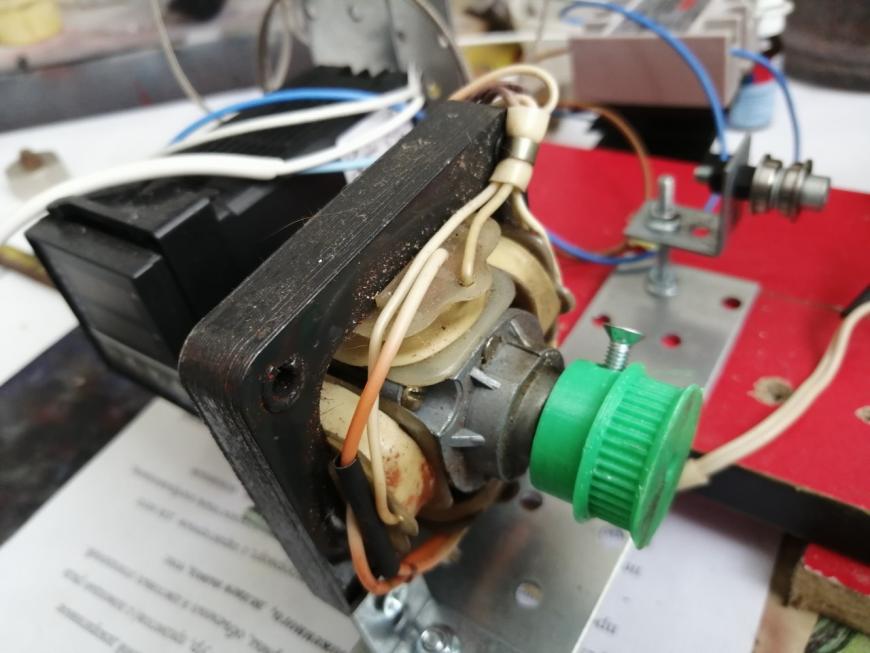
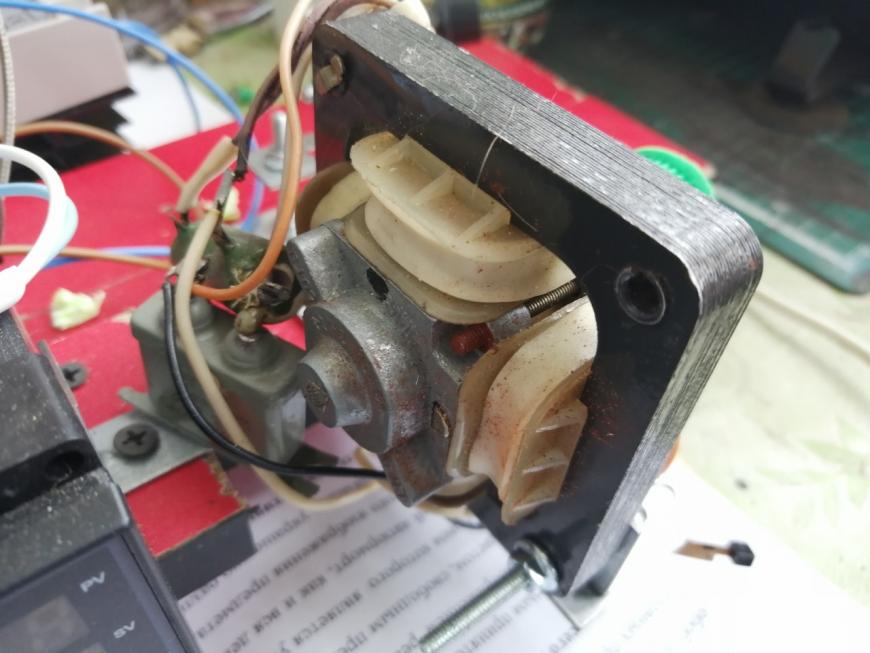
******************
В общем Вопросы следующие :
Стоит ли использовать шаговый двигатель? и какой ? (вместо того что я вам показал)
Как и чем его питать и регулировать обороты ?
В электронике я почти 0 , нужны готовые решения (типо с алика )
Буду рад если поделитесь опытом и идеями !
( Об узлах контроля и протяжки прутка пока не будем, не хочу загадывать далеко )
(если что моя группа https://vk.com/public_model_hends)
Еще несколько фото
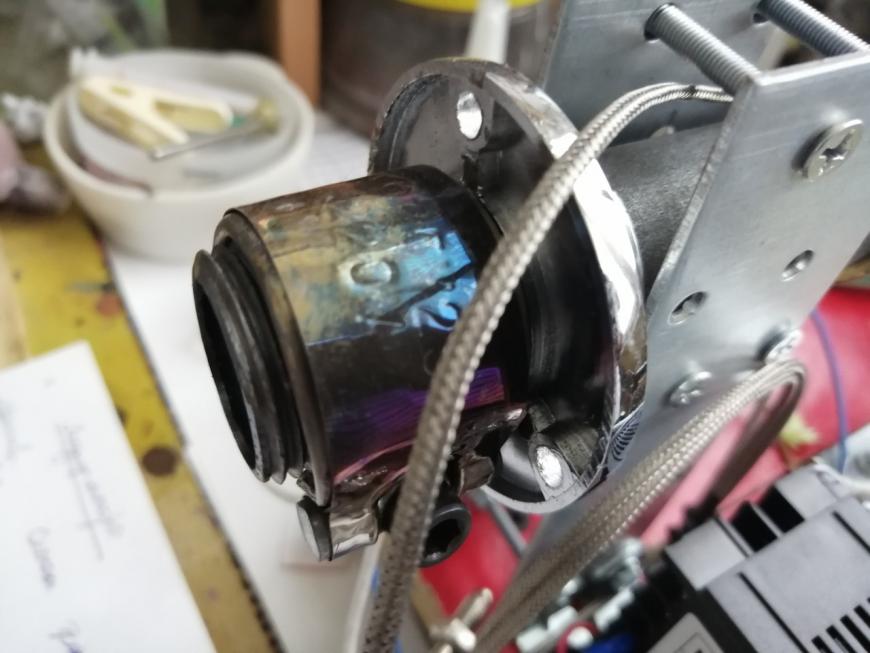
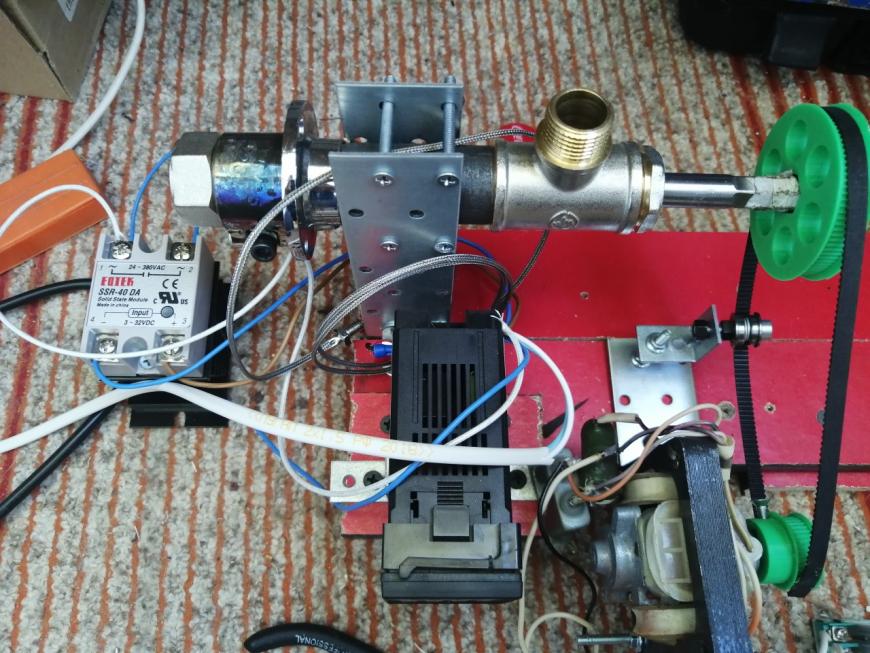
Как работает экструдер
При переработке пластмасс часто используют экструзию, которая заключается в расплавлении полимерной заготовки и изготовлении, в последующем, пластмассовых изделий определенной формы.
Данный процесс совершается при помощи специальных аппаратов — экструдеров, которые различаются в зависимости от типа действия и вида перерабатываемой пластмассы. Более подробно узнать о них, а если нужно, то и купить, можно на сайте http://www.plastikmash.ru/.
Экструдер изнутри
Данный механизм производит формовку пластмассовых деталей. Основой для таких изделий являются полимерные полуфабрикаты.
Механизм состоит из нескольких важных частей:
- Корпус, в котором размещается система нагрева. Нагревание происходит при помощи резистивных или индукционных систем, в которых подается индукционный ток Фуко.
- Устройство, сквозь которое подается сырье в корпус.
- Органы для подачи и перемещения внутри механизма пластмассовых заготовок.
- Устройство, формирующее форму изделий (так называемая экструзионная головка).
- Редукторы и двигатель, при помощи которых создается и передается энергия на другие рабочие органы.
- Механизмы для управления и контроля рабочего процесса.
Принцип работы
Сырье для экструдера можно использовать в различном виде. Это могут быть гранулы, порошок или лом определенного полимерного состава.
После попадания внутрь, пластмасса перемещается при помощи специальных органов, в зону переработки. Там она нагревается до определенной температуры, из-за чего она плавится.
Благодаря определенным устройствам, она хорошо перемешивается и получается однородная расплавленная масса. Затем этот материал под высоким давлением подается через фильтры в специальные головки для формирования изделия.
После этого оно выходит и остывает. Охлаждение продукции может происходить как естественным способом, так и с помощью специального оборудования.
Когда все остыло, получаются изделия определенной формы и с конкретными физическими параметрами.
При помощи экструдеров можно получать разнообразные конструкции, например полимерные трубы, пластиковые доски, оконные и дверные проемы и много другого. Сырье для таких машин может быть разнообразное, это может быть определенный полимер или обычные пластиковые бутылки.
Применение таких механизмов позволило использовать пластиковые отходы и получать при этом качественные изделия.
Смотрите также:
Инструмент для монтажа кабеля http://domkrat.org/instrument-dlya-montazha-kabelya/.
Интересное по теме: Как построить сруб
Советы в статье «Как сделать ремонт в квартире своими руками » здесь.
Схема работы экструдера изнутри:
Источник №1: http://www.plastikmash.ru/
TweetЭкструдер для производства изделий и из пластика
Одна из наиболее сложных экологических проблем мировой экономики – это утилизация химически опасных предметов, в первую очередь, изделий из ПВХ пластика. Многочисленные компании и индивидуальные предприниматели теряют миллионы, которые приходится платить за утилизацию использованной тары, изделий из поливинилхлорида. А затем вновь тратят деньги на покупку сырья!
Принципиальное решение
Есть простой, надежный и действенный способ решения проблемы – купить экструдер для пластика. Это устройство не только позволит выполнить задачу по утилизации пластика, но станет эффективным способом для развития бизнеса. Экструзия – это технология по переработке тары и других изделий из пластика с целью формирования сырья, необходимого для повторного изготовления различных деталей и продукции из ПВХ. Если коротко – суть технологии заключается в формировании расплавленной полимерной массы с дальнейшим формированием небольших гранул, имеющих форму, определенную техническими условиями эксплуатации.
Таким образом, используя технологию экструзии пластмасс можно развивать бизнес, собственное дело, предлагая недорогое сырье, которое получается из отходов производства. В обозримом будущем проблемы с вторсырьем (а именно в эту категорию входит большинство пластиковых отходов) не будет. А ведь именно сырье у производителей составляет большую часть расходов. Очевидно, что в современных условиях возможность переработки и повторного использования полимерных материалов — простое и эффектное решение для бизнеса!
Стоит более подробно изучить вопрос и разобраться, как работает экструдер пластмасс, и какие перспективы есть для ведения такого бизнеса.
Суть процесса
Экструзия представляет собой относительно простой технологический процесс, при котором на специальной линии (в нашем случае – изготовленной инженерами на территории России, на 100% из отечественных комплектующих) происходит процесс переработки сложных композиций, разнородного пластикового сырья. Под воздействием постоянного давления, создаваемого в работе системы, расплавленная масса продавливается через специальные отверстия формующей головки. В зависимости от формы и диаметра этой головки на выходе получают готовые полуфабрикаты, которые впоследствии могут использоваться для производства новых деталей и изделий либо храниться на складе в ожидании отгрузки заказчику.
Общее устройство и принцип работы оборудования
Extruder – это достаточно сложное электромеханическое устройство, предназначенное для переработки использованного поливинилхлорида и изготовления пластмассовых профильных небольших гранул. Такое сырье из полимеров можно в дальнейшем использовать для нового производства разнообразной ПВХ продукции или организации хранения сырья для его последующей продажи.
Специализированная компания «Полимермаш-Сервис» специализируется на изготовлении оборудования и специализированных линий по изготовлению сырья из переработанного пластика. Агрегат российского производства полностью соответствует требованиям качества, надежности и долговечности работы, а использование отечественных комплектующих, узлов и агрегатов, позволяет снизить стоимость оборудования. Наибольшей популярностью и спросом пользуется одношнековое устройство, как наиболее простое, надежное и безотказное в работе, позволяющее с помощью метода экструзии получать полимерное высококачественное сырье.
Конструктивные особенности
Экструдер полимеров состоит из следующих основных узлов и деталей:
- Прочный стальной корпус (цилиндр), оснащенный системой нагрева пластмасс до необходимой температуры. Используются керамические нагревательные элементы.
- Приемный бункер. Экструзионная линия начинается именно с этого элемента. Для переработки сюда насыпается подготовленный полимер в виде гранул, небольших лент или крупнозернистого порошка. Главное назначение бункера – обеспечить равномерную подачу сырья, что обеспечивает высокое качество экструдированного материала на выходе.
- Экструзионная головка. Другое название этой детали – фильера, она и задает необходимую форму полимеров.
- Приводной механизм. Состоит из электродвигателя и системы редукторов, с помощью которых происходит передача необходимого усилия и обеспечение работы одношнековой машины и происходит процесс переработки полимеров.
- Система управления. Стационарный или выносной пульт, с помощью которого управляется процесс экструзионной переработки пластмасс.
Схема работы
Сформированная технологическая линия российского производства отвечает всем необходимым требованиям по надежности и долговечности работы и позволяет осуществлять переработку пластиков на профессиональном уровне. Экструзия заключается в последовательном выполнении следующих операций:
- сырье в виде гранул, порошка или лома пластика поступает в приемный отсек;
- перемешанная масса направляется в рабочую зону одношнекового экструдера, где не нее воздействуют: давление, небольшая сила трения, подаваемая снаружи повышенная температура;
- под воздействием тепла, происходит нагревание пластмасс и их плавление до состояния, позволяющего продолжать экструзию далее;
- в ходе продвижения по направлению к фильере происходит тщательное перемешивание пластиковой массы, в результате чего, к моменту поступления в формирующие головки полихлорвинил имеет единую однородную форму, подготовленную к выдавливанию;
- для повышения качества изделий, перед окончательным формированием гранул, масса проходит под высоким давлением через специальный сетчатый фильтр, где удаляются различные мельчайшие посторонние предметы;
Далее сырье упаковывается и укладывается на хранение либо передается заказчик для переработки и производства новых изделий. Хранить гранулы можно неограниченное время!
Вот так работает экструзионная линия. Ничего сложного в работе экструдера нет. Главное, после принятия решения на покупку данного оборудования, сделать правильный выбор и обратиться к профессионалам.
Отличные перспективы
Метод экструзии используется повсеместно, до 50% термопластов подвергается переработке данным способом. Экструзия позволяет изготавливать из ПВХ следующие материалы:
- пленки;
- листы;
- трубы;
- шланги;
- капилляры;
- прутки;
- сайдинг;
- профильную продукцию независимо от степени сложности и конфигурации;
- нанесение полимерного материала на элементы электропроводов;
- изготовление многослойных элементов и деталей.
При этом количество переработанного термопласта с помощью экструдеров год от года растет. Сейчас на рынке сложилась ситуация, при которой спрос на переработку превышает предложение. А значит, созданы условия для открытия собственного бизнеса!
Выгодное предложение
ООО «Полимермаш-Сервис» предлагает на выгодных условиях приобрести одношнековый экструдер для переработки полимеров, а также ряд другого востребованного на рынке производственного оборудования. Производственные мощности Общества располагаются в Пензенской области, но реализация экструдеров и линий производится в любые города и регионы страны. Каждому клиенту компании мы готовы предложить высококачественное, надежное и недорогое оборудование для переработки полимеров.
Каждая установка, прежде чем поступить в продажу, проходит испытание под нагрузкой, проверку надежности и эффективности работы. В качестве дополнительной услуги выполняем комплекс работ по подготовке экструдеров и производственных линий к вводу в эксплуатацию. Если потребуется – инженеры компании проведут подготовку персонала компании-заказчика.
С нами выгодно сотрудничать. Обращайтесь, господа предприниматели!
Экструдер ЭПС 125×30
|
|
Экструдер эпс 150х30, назначение, описание, преимущества выбора
Полимерное покрытие, нанесенное на металлические поверхности трубопроводов, существенно увеличивает эксплуатационный ресурс изделий, защищает от коррозии. Использование специального оборудования позволяет повысить эффективность, качество готовой продукции.
Назначение
Экструдер эпс 150х30 предназначен для переработки гранулированных полимерных материалов и передачи расплавленной смеси в экструзионную головку для последующего нанесения массы на металл. Конструктивные особенности экструдера позволяют использовать агрегат в закрытых помещениях, с соблюдением всех установленных требований и правил пожарной, экологической безопасности.
Основные технические характеристики
Прежде чем принять окончательное решение на покупку ЭПС, рекомендуем изучить эксплуатационные параметры оборудования. Экструдер может быть использован в процессе наложения полимерного покрытия на стальные трубы диаметром от 57 до 820 мм. Привод назад осуществляется за счет трехфазного электродвигателя, также работу системы обеспечивают электронагреватели и вентиляторы. Суммарная потребляемая мощность установки составляет не более 320 кВт, производительность – до 750 кг/ч Предусмотрена возможность регулировкитемпературы, подогреваемой смеси, в пределах 0 — 400°С.
Экструдер поставляется в следующей комплектации:
- платформа установки с механизмом перемещения назад;
- массивный корпус;
- шнек;
- редуктор с узлом упорного подшипника;
- электрический привод;
- пульт управления;
- шкаф частотного преобразователя;
- бункер;
- электрооборудование.
Правильный выбор
Если по вышеперечисленным параметрам модель ЭПС подходит, приобрести установку на выгодных условиях можно у нас.
В каталоге представлен широкий выбор оборудования, предназначенного для производства и переработки полимерных материалов. На установки предоставляется гарантия качества, надежности, долговечности эксплуатации. Доставка осуществляется по всей территории России и в страны СНГ. Не было ни одного случая возврата назад по причине неэффективности работы. География поставок постоянно расширяется, благодаря балансу реализуемого оборудования в соотношении цены и качества.
Экструдер ЭПС 20×25 | Экструдер ЭПС 25×25
|
Экструдер ЭПС 32×25
|
Экструдер ЭПС 32×30
|
Экструдер ЭПС 45×25
|
Экструдер ЭПС 45×30
|
Экструдер ЭПС 48×25
|
Экструдер ЭПС 63×25 | Экструдер ЭПС 63×30
|
Экструдер ЭПС 75×25
|
Экструдер ЭПС 75×30
|
Экструдер ЭПС 90×25 | Экструдер ЭПС 90×30
|