Экструдер — это… Что такое Экструдер?
машина для размягчения (пластикации) материалов и придания им формы путём продавливания через профилирующий инструмент (т. н. экструзионную головку), сечение которого соответствует конфигурации изделия. Процесс переработки материалов в Э. называется экструзией. В Э. получают главным образом изделия из термопластичных полимерных материалов (см. Пластические массы), используют их также для переработки резиновых смесей (См. Резиновая смесь) (в этом случае Э. часто называют шприц-машиной). С помощью Э. изготовляют плёнки, листы, трубы, шланги, изделия сложного профиля и др., наносят тонкослойные покрытия на бумагу, картон, ткань, фольгу, а также изоляцию на провода и кабели. Э. применяют, кроме того, для получения гранул, подготовки композиций для каландрирования (См. Каландрирование), формования металлических изделий (об этом процессе см. в ст. Прессование металлов, Порошковая металлургия) и других целей. Э.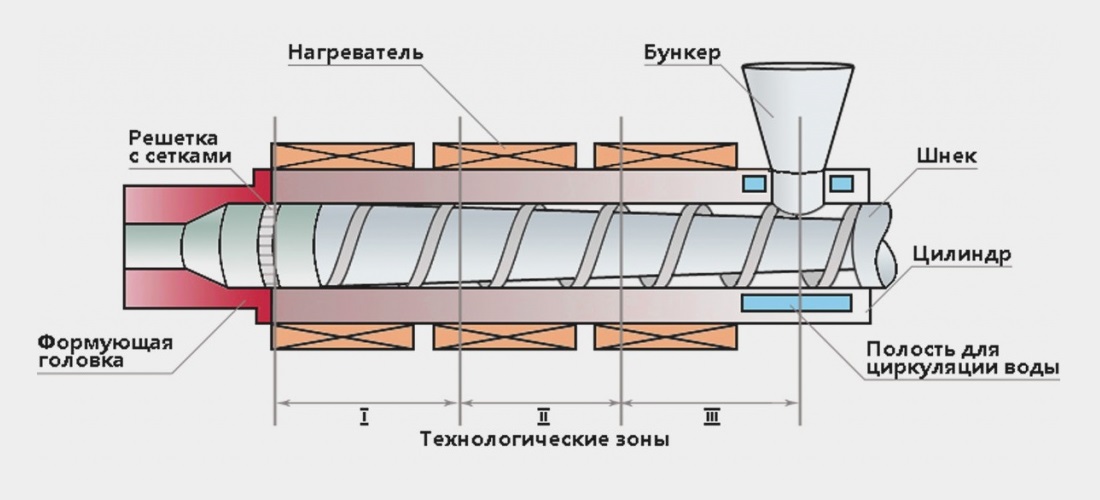
Первые Э. были созданы в 19 в. в Великобритании, Германии и США для нанесения гуттаперчевой изоляции на электрические провода. В начале 20 в. было освоено серийное производство
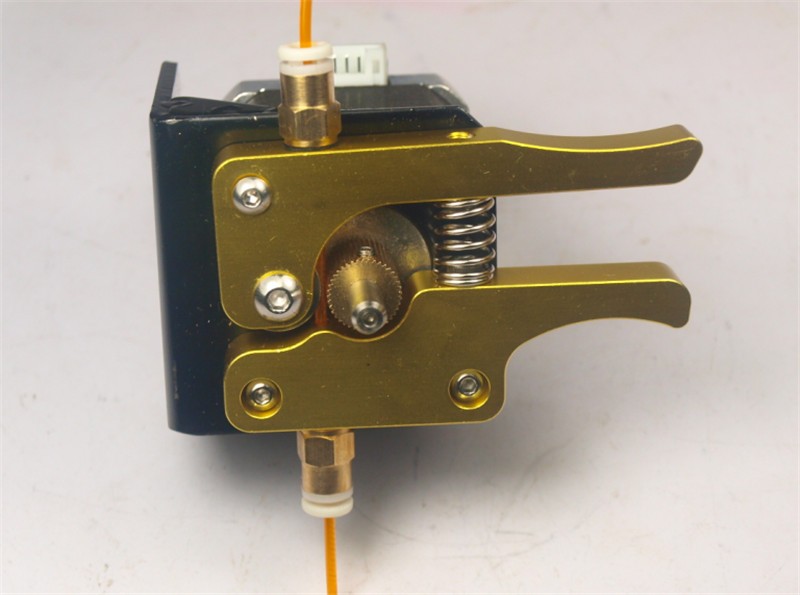
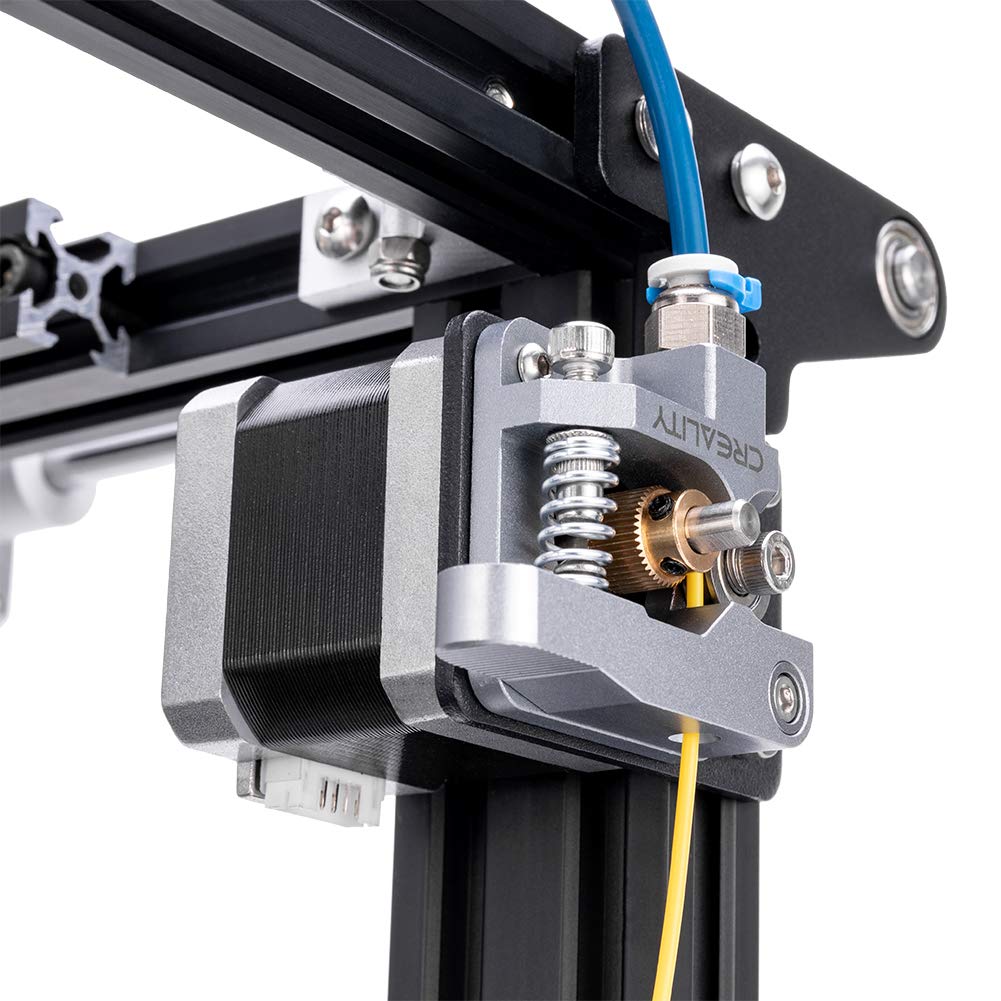
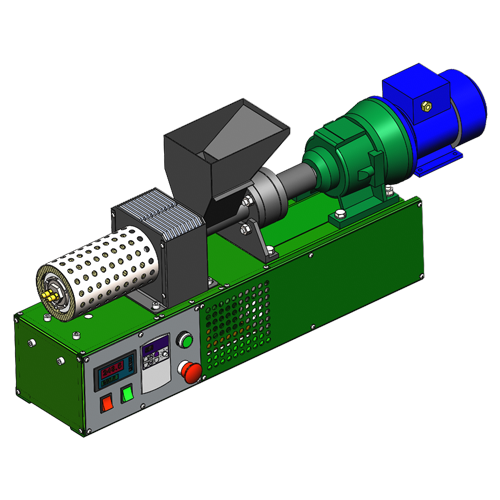
Современные Э. — автоматизированные установки, производительность которых достигает 3—3,5 т/ч. Доля термопластичных полимерных материалов, перерабатываемых в Э., колеблется в разных странах в пределах 30—50%.
Лит.: Бернхардт Э. (сост.), Переработка термопластичных материалов, пер. с англ., М., 1962; Завгородний В. К., Калинчев Э. Л., Махаринский Е. Г., Оборудование предприятий по переработке пластмасс, Л., 1972; Оборудование для переработки пластмасс, М., 1976; Торнер Р. В., Теоретические основы переработки полимеров, М., 1977.
М. Л. Фридман.
Схема одношнекового горизонтального экструдера: 1 — двигатель; 2 — экструзионная головка; 3 — нагреватель корпуса; 4 — корпус; 5 — шнек; 6 — загрузочное устройство; 7 — упорный подшипник; 8 — редуктор.
Что такое экструдер? Назначение экструдеров
Внимание. В данной статье описаны принципы работы и внутренне устройство экструдеров и если вы желаете, можете ознакомиться с производимыми нашей компанией моделями экструдеров на сайте, для этого откройте страницу «Каталог экструдеров»
Что такое экструдер?
Экструдер — это специальная машина для непрерывной обработки сырья (дробленки, гранул, агломерата и т.
Необходимое сырье для экструдера, как правило, высыпается в загрузчик или сразу в бункер машины экструдера. Из этого контейнера, экструдат направляется в зону шнековых приводов и далее перемещается по поверхности пластифицирующего цилиндра. После перемешивания, продавливания и взаимодействия с горячим цилиндром исходное сырье плавится и трансформируется в массу с однородным составом, обычно называемым расплавом.
Экструдер может являться одним из устройств целой линии по производству экструдированных кормов, она называется производственная экструзионная линия.
Чтобы ознакомиться с нашим предложением по экструдерам, грануляторам, измельчителям и др. видам оборудования участвующего в производстве кормов, вы можете также изучить другие разделы сайта, в частности каталог продукции.
Как устроен экструдер?
Экструдеры, производимые ООО «Агротехсервис 14», комплектуются единой рамой, спецредуктором с системой внутренней защиты и повышенной надежностью экструдирования.
Электрошкаф с системой тепловой автоматики, приборами управления отсекателем и всего оборудования экструдера находится на пульте оператора. Расположение важных приборов и кнопок в одной панели по отзывам наших клиентов самое удачное, ведь в большинстве случае именно оператор оценивает экструдер в работе.
Система автоматики имеет температурные зоны контроля экструдера и зоны управления нагревом головок, что повышает безопасность изделия. Для управления и контроля всеми зонами применяется приборы теплоавтоматик необходимые для точной регулировки температуры на участках и это положительно отражается на высоком качестве кормов.
Экструдеры, предназначенные для работы в составе линий для производства профиля из пластифицированного ПВХ, имеют увеличенный диаметр шнековой пары и уменьшенную частоту вращения шнека, наша компания выпускает зерновые экструдеры различной мощности.
Все экструдеры комплектуются дополнительными насадками, позволяющими удобнее и быстрее производить экструдированные корма, повышая производительность и эффектинвность работы как обоурдования так и оператора.
Что такое фильера и экструдер?
Экструдер – это оборудование, применяемое в экструзии (размягчении) пластмасс. Фильера для экструдера очень важная деталь в его работе. Ведь, именно благодаря фильерам происходит размягчение и предание нужных форм пластмассе. Фильера – это экструзионная головка, имеющая различную форму и размер.
Классификация фильеров для экструдера
Фильера (экструзионная головка) размещена на конечном выходе экструдера. На сегодняшний день самой используемой классификацией является разделение фильер по форме получаемого сырья. Основная функция фильер состоит в формовании экструзионного продукта нужного вида из потока пластмасс.
Например, для получения трубок, труб и шлангов, применяют кольцевой фильер; для изготовления листов и пленки используют щелевые фильеры.
Название фильер берет начало из обозначения выпускаемой продукции. На деле такие фильеры кличут трубные, плоскощелевые, пленочные, рукавные пленочные.
Профильная фильера могут быть разной формой и размером. Такой тип фильер используется для экструдирования продукта совершенно разной формы, которая имеет отличия от прямоугольной, кольцеобразной или круглой. Существует две разновидности профильных фильер:
— плоская фильера;
— полностью обтекаемая фильера.
В структуре плоских фильер используют ровную плиту с пазухой, по конструкции, совпадающей требуемой экструзионному продукции. Эту пластинку прикрепляют в окончание зоны. Большим плюсом плоской фильеры является легкость в процессе производства. Из минусов обратим внимание на то, что в этих фильерах потоки расплавов пластмасс не обтекаемы и может привести к появлению мертвых зон.
Строение обтекаемой фильеры предполагает пошаговое сужение канала к выходной форме. В связи с чем, на протяжении течения расплава через обтекаемую фильеру замечается поэтапное ускорение потока. Такое строение снижает вероятность застоя продукта, благодаря этому обтекаемые фильера лучше других типов фильеры подходят для длительного, крупнотоннажного, непрерывного процесса экструзии, а еще при переработке пластмасс с малой термостойкостью. Недостатком есть то, что изготовление является достаточно сложным, поэтому эта фильера стоят намного дороже.
Фильера для изготовления плоскощелевого листа и пленки имеют одинаковую структуру, однако элементы имеют некоторые отличия. Основными элементами являются:
- коллекторы;
- входные каналы;
- предформовочные зоны;
- зоны релаксации;
- формообразующие поверхности.
Чтобы изготовить пленку экструзионным методом с последующим раздувом, была произведена фильера специальной конструкции – фильера со специальным дорном. Преимущество таких фильер со спиральным дорном в том состоит из:
- хорошего распределения потока;
- незаметности линий соединения потоков расплава;
- образования винтового потока кольцевой ориентации, при этом увеличивается окружная плотность экструдируемого продукта;
- возможности моделирования течения изделия через зону спирального дорна, что быть полезно при оптимизации и проектировании.
Угловые фильеры используются при нанесении на провода изоляционных покрытий. С их применением проводник передвигается через трубчатые основания и наконечники с высокой скоростью.
Кольцевые фильеры могут быть как угловыми, так и прямоточными. Все каналы прямоточной фильеры находятся на одной оси. Это расположение является предпочтительным, когда существует необходимость равномерно распределить напряжение по всему экструдируемому изделию.
Когда используется угловая фильера, расплав течет вокруг разделителя потока, затем протекает по выступам по направлению дорна и мундштука.
Кольцевая фильера используется в производстве шланг, трубок и труб, рукавных пленок, а также для нанесения изоляции.
Фильера для экструдера – основа механизма
Как вы могли понять и заметить фильера для экструдера – это сердце механизма. Ведь, именно в фильерах происходит доведение до нужно формы и размера пластмасс. Для производства пластмассовых изделий фильера для экструдера имеют особое значение. Если для вашего производства понадобился экструдер или фильера: напишите или позвоните нам, в компанию «РУСМИР инжиниринг».
Одношнековый экструдер (одночервячный экструдер) — Словарь терминов | ПластЭксперт
Понятие и общие сведения
Одношнековый экструдер — это разновидность экструзионной техники, обеспечивающей переработку пластмасс в изделия методом экструзии. Особенность именно этого оборудования заключается в том, что в составе экструдера применятся только один шнек. Такая компоновка в отличие от двушнековых или многошнековых, а также различных специальных экструдеров, является наиболее простой.
Одношнековые экструдеры используются в качестве главного компонента экструзионных линий, которые в зависимости от разновидности формующего инструменты состава прочих компонентов линии могут производить пленки, трубы и другие профили, листы и т.д. Зачастую в составе одной линии присутствуют несколько экструдеров, такие линии называются коэкструзионными или соэкструзионными. Они предназначены для выпуска многослойных или многокомпонентных экструзионных изделий.
Рис.1. Одношнековый экструдер. Принципиальная схема.
Общий вид одношнекового экструдера представлен на рис.1. Где цифрами обозначено:
1 – Загрузочный бункер полимера.
2 – Материальный цилиндр, состоящий из трех или более зон (питания, пластикации и дозирования).
3, 4 – Адаптер, переходное кольцо или другое устройство для передачи расплавленной полимерной массы из экструдера к формующему инструменту.
5 – Формующий инструмент (экструзионная головка).
6 – Шнек (червяк) одношнекового экструдера.
7 – Кольцевые нагреватели материального цилиндра.
8, 9 – Силовые установки, двигатели.
10 – Редуктор.
Применение
Перечислим кратко наиболее частые области применения линий, в конструкциях которых широко используются одношнековые экструдеры.
1. Линии по выпуску однослойных или многослойных пленок, в том числе BOPP-пленки и других упаковочных пленок, сельскохозяйственной пленки, пленок специального назначения и т.д. Пленочные линии могут быть предназначены как для выпуска рукавной пленки, так и для производства пленочного полотна.
2. Для производства труб, трубок, шлангов и т.д. применяются классические горизонтальные линии, сердцем каждой из которых служит одношнековый экструдер. В последнее время в составе таких линий часто применяют несколько экструдеров – как для организации выпуска многослойных труб, так и для экструзионной маркировки изделий.
3. При помощи одношнековых экструдеров также производят разнообразные листы и профили (кроме известных всех профилей ПВХ (окон, подоконников, панелей, водостоков и т.д.) – для их производства обычно применяют не одношнековые, а двушнековые экструдеры. Типичным представителей таких изделий являются сотовые листы (поликарбонат, полипропилен и т. п.).
4. Экструзионная техника также применяется для выпуска прочей продукции, например кабельно-проводниковых изделий, различных плит, кромок и прочих.
5. Важнейшая и набирающая обороты сфера применения одношнековых экструдеров – вторичная переработка пластмасс. Экструдеры применяются в основном при гранулировании предварительно измельченного или агломерированного полимерного материала в конце цикла его рециркуляции при получении полноценных гранул вторичного полимера.
Объявления о покупке и продаже оборудования можно посмотреть на
Доске объявлений ПластЭксперт
Обсудить достоинства марок полимеров и их свойства можно на
Форуме о полимерах ПластЭксперт
Зарегистрировать свою компанию в Каталоге предприятий
Вернуться к списку терминовв чем разница и какой лучше?
Большинство 3D принтеров используют прямую (Direct) или Боуден (Bowden) экструзию. В обеих конструкция используется экструдер для проталкивания материала сквозь нагретое сопло. Разница в том, что в первом случаем материал для 3D печати подается напрямую, а во втором — через трубку Боудена. Несмотря на то, что по принципу работы эти конструкции похожи, они имеют существенные различия. В материале ниже мы детали реализации, а также плюсы и минусы этих двух конструктивных решений.
Direct экструдеры
Direct экструзия — это метод экструзии, при котором экструдер проталкивает материал для 3D печати непосредственно в сопло. Этот метод хорош по многим причинам, но у него есть и недостатки. Давайте взглянем.
Плюсы
Лучшая экструзия: поскольку на печатающей головке установлен прямой экструдер, двигатель может легко проталкивать нить через сопло, что обеспечивает лучшую экструзию.
Более быстрый ретракт: поскольку экструдер находится близко к соплу, прямой экструдер может быстро отводить материал и возникает меньше проблем с остатками материала между пустотами модели.
Менее мощный двигатель: из-за небольшого расстояния между экструдером и соплом для проталкивания материала требуется меньший крутящий момент от двигателя.
Более широкий ассортимент материалов: прямой экструдер совместим с широким спектром материалов для 3D печати. Даже с гибкими и абразивными материалами прямая экструзия обеспечивает надежную 3D печать.
Минусы
Дополнительная тяжесть при перемещении сопла: при установке экструдера на печатающую головку, очевидно, увеличивается вес. Этот дополнительный вес добавляет ограничения скорости, вызывая большее колебание и, возможно, потерю точности по осям X и Y.
Bowden экструдеры
В отличие от Direct механизмов экструзии, экструдеры типа Bowden устанавливаются на раме 3D принтера. Он проталкивает и протягивает нить через длинную трубку Боудена из PTFE непосредственно к хот энду. У этой системы тоже есть плюсы и минусы.
Плюсы
Оптимизация перемещения каретки 3D принтера: поскольку Боуден экструдер устанавливается на раме 3D принтера, а не на печатающей головке, на каретку приходится гораздо меньше веса. Меньший вес означает возможность более быстрых, тихих перемещений и (тут спорно) лучшее качество 3D печати.
Больший объем рабочего пространства: Боуден экструдер позволяет использовать меньшую каретку печатающей головки, что, в свою очередь, позволяет увеличить объем рабочего пространства.
Компактный размер: Боуден экструдеры обычно более компактные и занимают меньше места, чем обычный прямой экструдер.
Минусы
Более мощный двигатель: поскольку Боуден экструдер проталкивает и протягивает материал через длинную трубку, между ними существует определенное трение. Это трение требует большего крутящего момента.
Более медленное время отклика: большее трение в трубке Боудена также приводит к более медленному времени отклика. Экструдеры типа Боуден требуют более длинного настояния и большей скорости ретракта во избежание дефектов 3D печати.
Меньший диапазон доступных материалов: некоторые гибкие и абразивные материалы могут застревать или изнашиваться в трубках Боудена. Например, для 3D печати гибким материалом TPU на Ender 3 рекомендуют сменить Боуден конструкцию на прямую подачу пластика.
Выводы
Итак, какая система лучше? Прежде чем решить, какой вариант экструзии использовать для вашего 3D принтера, следует учесть некоторые важные факторы.
Во-первых, стабильность и жесткость рамы. Например, принтеры Delta наверняка не смогут поддерживать прямую экструзию. Однако если у вашего 3D принтера декартова система координат и прочная рама, 3D печать с помощью Direct экструдера не должна вызывать проблем.
Скорость также является решающим фактором. Если ваш приоритет — быстрая и точная 3D печать стандартными материалами, экструдер типа Боуден может стать отличным выбором.
Наконец, вам следует подумать о материалах, которые вы хотите использовать для 3D печати. Если вас интересуют гибкие или абразивные нити, вам, вероятно, лучше подойдет механизм прямой экструзии.
Экструдеры
Экструдер состоит из нескольких основных узлов — корпуса, оснащенного нагревательными элементами, рабочего органа (шнека, диска, поршня), размещенного в корпусе, узла загрузки перерабатываемого продукта, привода, системы задания и поддержания температурного режима и других контрольно-измерительных и регулирующих устройств.
Существуют экструдеры со шнеками, осуществляющими не только вращательное, но и возвратно-поступательное движение. Для эффективной гомогенизации продукта на шнеках устанавливают дополнительные устройства — зубья, шлицы, диски, кулачки и др. В последнее время получают распространение планетарно-вальцовые экструдеры, у которых вокруг центрального рабочего органа (шпинделя) вращается несколько дополнительных шнеков (от 4 до 12). Принцип действия дискового экструдера основан на использовании возникающих в упруговязком материале напряжений, нормальных к сдвиговым. Основу конструкций такого экструдера составляют два плоскопараллельных диска, один из которых вращается, создавая сдвиговые и нормальные напряжения, а другой неподвижен. В центре неподвижного диска имеется отверстие, через которое выдавливается размеченный материал. Поршневой экструдер из-за низкой производительности используют ограниченно, в основном для изготовления труб и профилей из реактопластов.
Конструкции экструдеров могут быть классифицированы также по геометрической форме, механическим, функциональным или термодинамическим характеристикам. Кроме того, экструдеры рекомендуется классифицировать по их физическим признакам, поскольку они оказывают влияние на химические структурные характеристики экструдированных продуктов. Особое значение имеют такие параметры, как уклон режущей кромки матрицы и количество тепловой энергии, образующейся в процессе экструдирования за счет механического преобразования энергии; температура во время ведения процесса; влажность экструдируемой массы.
При переработке пищевых продуктов наибольшее распространение получили экструдеры со шнеками полного зацепления, вращающимися в одном направлении, когда вершины одного шнека взаимодействуют с впадинами другого.
В двухшнековых самоочищающихся экструдерах обеспечиваются более быстрый пуск шнека и работа на повышенной скорости. В них реже возникают подъемы давления, так как не происходит накопление продукта. В одношнековых экструдерах, вследствие того, что продукт может оставаться в витках и накапливаться, создавая разрывы потока, подъемы давления бывают чаще. В результате продукт из экструдера выпускается неравномерно.
Однако предполагается, что в одношнековом экструдере износ шнека концентрируется по наружной кромке к торцу его витков, и это обеспечивает восстановление шнека.
Двухшнековый экструдер более подвержен износу. Изнашиваются шнеки в местах загрузки и выгрузки продукта. В этой связи свойства конечного продукта и эффективность процесса экструдирования в большой степени зависят от износа рабочих органов машины при обработке в двухшнековом экструдере. При использовании двухшнекового экструдера не требуется предварительной гидротермической обработки продукта, что упрощает производственный процесс. Гидролиз крахмала пшеничной муки протекает гораздо эффективнее в двухшнековом экструдере, чем в одношнековом. В двухшнековом экструдере зоны пластификации и повышения давления отделены друг от друга, что позволяет независимо осуществлять пластификацию и экструдирование продукта. Известно, что затраты, связанные с приобретением одношнековых экструдеров, ниже по сравнению с затратами на приобретение двухшнековых машин. Однако последние компенсируются меньшими эксплуатационными расходами. Высокие расходы по эксплуатации одношнековых машин связаны с длительными простоями при чистке, большими трудозатратами и объемом работ по обслуживанию.
Сравнение конструктивных и технологических достоинств одношнековых и двухшнековых экструдеров показывает значительное преимущество последних.
Материал для матриц должен быть коррозионно-стойким, обладать антиадгезионными свойствами и высокой прочностью. Чтобы снизить прилипаемость формуемого продукта, отверстия полируют и хромируют. Широко применяют в настоящее время матрицы, состоящие из металлической обоймы и сменных вставок. Вставки представляют собой сменные гильзы с формующими отверстиями, изготовляются из пластмасс с сильно выраженными антиадгезионными свойствами.
Форма и размер предматричной камеры зависят от свойств перерабатываемого продукта, типа и размеров нагнетающего механизма и должны способствовать выходу выпрессовываемой массы через каналы матрицы с возможно более равномерной скоростью, а также препятствовать образованию застойных зон. Формование экструзией имеет ряд преимуществ: непрерывность осуществления процесса с высокой скоростью, безотходность технологии и высокая культура производства.
Машина А1-КХП (рис.) предназначена для формования палочек из кукурузной крупы тепловой и механической обработкой.
Рис. Машина А1-КХП
Машина состоит из станины 1, бункера 7, корпуса подшипника 9, цилиндра 3, механизма резки 4, вариатора, щита управления с нагревателями. Машина имеет два индивидуальных привода: для шнека и механизма резки.
На верхней плите сварной станины установлен электродвигатель 8 привода шнека, соединенный через муфту с быстроходным валом редуктора 10. Последний, в свою очередь, с помощью муфты соединяется с валом корпуса подшипника. В литом корпусе подшипника установлен вал, вращающийся в радиальных подшипниках качения. Для восприятия осевой нагрузки от формующего шнека в корпусе установлен упорный шарикоподшипник.
К корпусу подшипника фланцем крепится сварной цилиндр с расположенным внутри него шнеком. С противоположной стороны цилиндр закрыт матрицей. Температура в рабочей зоне контролируется термопарами, введенными в зону через пробку 5. Для нагрева кукурузной массы в передней части цилиндра укреплен блок электронагревателей 6.
У переднего торца матрицы расположен механизм резки с вращающимися ножами, который приводится в движение от отдельного электродвигателя через бесступенчатый вариатор. Электродвигатель и вариатор находятся внутри станины. Частота вращения вариатора регулируется рукояткой 2, установленной в непосредственной близости от панели управления. Для удобства обслуживания механизм резки отводится в сторону.
Над цилиндром установлен бункер для приема кукурузной крупы. Кукурузная крупа из бункера машины через регулируемую заслонку поступает в приемное отверстие цилиндра, где происходит прессование продукта и нагрев до температуры 145 °С.
В результате воздействия тепла, влаги и давления крупа превращается в пластическую массу, которая выдавливается шнеком через отверстия матрицы. При выходе из отверстий матрицы масса под действием пара, образующегося из перегретой влаги, вспучивается, образуя пористую хрустящую жилу. Механизм резки делит выходящие жилы на палочки, которые уносятся конвейером.
Порция крупы (1,5… 2,0 кг при температуре в цилиндре 80… 145 °С) приготовляется за 30…60 мин до пуска машины.
Режим нагрева цилиндра подбирается для каждой машины индивидуально в зависимости от сорта, помола, влажности крупы и степени износа.
Техническая характеристика экструдера А1-КХП приведена в табл.
Машина Б8-КХ-ЗП (рис.) предназначена для производства палочек из кукурузной крупы посредством ее тепловой и механической обработки с последующей фасовкой на других автоматах.
Рис. Машина Б8-КХ-ЗП
Машина состоит из станины 1, формующего механизма 2, механизма 5 отрезки палочек по длине, ворошителя 3 кукурузной крупы, блока электронагревателей 4.
Формующий механизм состоит из охватываемого шнека с правой нарезкой, шнековой втулки с левой нарезкой, матрицы с двенадцатью отверстиями диаметром 3 мм, обоймы с четырьмя отрезными ножами, приводимой во вращение через цепную и клиноременную передачи от электродвигателя.
Ворошитель представляет собой корпус, внутри которого вращается вал с лопастями, перемешивающий поступающую из бункера крупу.
Блок электронагревателей предназначен для нагрева рабочей зоны машины в период пуска и автоматического под держания постоянной температуры от 160 до 180 °С. Во избежание перегрева машины в зоне загрузки предусматривается принудительное водяное циркуляционное охлаждение корпуса формующего механизма с подключением к сети водоснабжения.
Схемой машины предусмотрено ручное управление электроприводами шнека и ножа, а также ручное и автоматическое управление блоком нагревателей.
Перед пуском машины производится нагрев рабочей зоны формующего механизма в течение 30…35 мин до 160… 180 °С с помощью блока электронагревателей. За 25.. .30 мин до пуска машины готовится первая порция крупы влажностью 20.. .21 %. Подготовленная крупа по специальному лотку вручную засыпается небольшим потоком в отверстие зоны загрузки при включенной машине. После выхода палочек из формующей матрицы открывается заслонка, и в машину поступает крупа влажностью 13… 14 %.
Нагрев продукта в момент запуска происходит за счет теплопередачи, а в дальнейшем — за счет тепла, образующегося в результате трения между продуктом, шнеком и шнековой втулкой. Выпрессованная полужидкая масса за счет перепада давления при выходе из отверстия формующей матрицы взрывается с диаметра 3 мм до диаметра 8… 12 мм.
Таблица. Техническая характеристика экструдеров
Показатель |
А1-КХП |
Б8-КХ-ЗП |
Производительность, кг/ч |
75 |
90 |
Мощность, кВт: | ||
привода |
21 |
18,5 |
электронагревателя |
3,84 |
2,8 |
Число шнеков |
1 |
1 |
Частота вращения шнеков, мин»1 |
71 |
79,3 |
Диаметр шнеков, мм |
155 |
74 |
Максимальная температура в зоне нагрева, «С |
145 |
160…180 |
Максимально допустимое давление экструзии, МПа |
10 |
12 |
Габаритные размеры, мм |
1750x890x1635 |
1200x1200x1900 |
Масса, кг |
1300 |
950 |
Экструдер МФБ-1 (рис.) состоит из плиты 15, станины 1 с кронштейном 12, электродвигателя 14, червячного редуктора 13, корпуса 4 со шнеком 3 и формующей матрицей 2, головки 7 с парой конических шестерен 8 и загрузочной воронки 5 со спиралью 11.
Рис. Шнековый экструдер МФБ-1
Внутри головки 7 находятся горизонтальный вал 9 с конической шестерней и приводной звездочкой 10, вертикальный вал 6 с конической шестерней и спиралью. Спираль 11 подает конфетную массу в корпус 4 и непрерывно перемешивает ее в загрузочной воронке 5. Шнек 3 выпрессовывает массу через формующие каналы матрицы 2 в виде пяти бесконечных жгутов, которые после предварительного охлаждения разрезаются на конфеты.
Техническая характеристика экструдера МФБ-1 приведена в табл.
Двухшнековый экструдер поточных линий ШФК (рис.) отличается от экструдера МФБ-1 наличием двух горизонтальных шнеков, находящихся в самостоятельных камерах. Шнеки нагнетают массу в общую предматричную камеру 3. Масса выходит через шесть или восемь формующих каналов. Частота вращения спирали в загрузочной воронке 2 изменяется бесступенчатой рукояткой 1. Нагнетающие шнеки имеют постоянную частоту вращения. При переходе с формования жгутов круглого сечения на прямоугольные шнеки заменяют.
Рис. Шнековый экструдер ШФК
В шнековых экструдерах скорости выхода жгутов через формующие каналы неодинаковы. Для выравнивания скоростей увеличивают длину средних формующих каналов по сравнению с крайними, устанавливают дополнительные сопротивления перед средними каналами или в самих каналах либо устанавливают более высокую температуру стенок крайних формующих каналов. Добиться полного равенства скоростей во всех каналах весьма трудно.
Техническая характеристика экструдера приведена в табл.
Экструдер ШВФ-22 (рис.) предназначен для выдавливания конфетной массы при производстве пралиновых конфет.
Рис. Экструдер ШВФ-22
Он имеет в предматричной камере перегородки, образующие секции у каждого выходного отверстия. Это выравнивает скорости у выдавливаемых жгутов. Бункер 1 укреплен на корпусе питателя 2 с расположенными в нем рифлеными валками 3. В корпусе нагнетателя 4 вращаются нагнетающие шестеренные роторы 5, выполненные из набора шестерен. Предматричная камера 7 имеет вертикальные формующие каналы 8. В нижней части корпуса нагнетателя и предматричной камеры имеются вертикальные перегородки 6, которые делят корпус и камеру на отдельные секции.
Бункер, корпус нагнетателя и нагнетатель, а также предматричная камера имеют рубашки для обогрева.
Конфетная масса вытягивается из бункера рифлеными валками 3 и равномерно подается по всей длине шестеренных роторов 5. Они нагнетают массу в предматричную камеру 7 и из нее через формующие каналы 8 выдавливаются жгуты 9 пралиновой массы.
Техническая характеристика экструдера ШВФ-22 приведена в табл.
Таблица. Техническая характеристика экструдеров
Показатель |
МФБ-1 |
ШФК |
ШВФ-22 |
Производительность, кг/ч |
325 |
150…310 |
1000 |
Число отверстий в матрице |
5 |
6 |
22 |
Потребная мощность, кВт |
1,7 |
2,8 |
2,8 |
Габаритные размеры, мм |
1250x845x1640 |
1365x775x2100 |
1000x1160x2980 |
Масса, кг |
410 |
955 |
1220 |
Почему стоит переходить на geared (шестереночный) экструдер и соображения по калибровке экструзии.
Для «гуру» вещи очевидные, но я решил сам посчитать и понять последствия применения DIRECT DRIVE экструдера. DIRECT тут в смысле того, что шестерня двигателя напрямую толкает пруток без понижения или повышения соотношения шестеренок. Т.е. это и к боудену тоже относится.Итак, небольшие расчеты.
Сечение идеального прутка 1.75мм составляет 2,405282 мм2
У меня экструдер в драйвером в режиме микрошагового управления 1/16 и шкивом на 16 зубов. Т.е. 100 микрошагов на 1мм, т.е. один микрошаг это 0.01мм
Таким образом за один микрошаг выдавливается пластик объемом 0,024053 мм3
Это абсолютный минимум, меньше которого выдавить экструдер просто не может.
Предположим мы печатаем слоем 0.1мм. Ширина экструзии 0.4мм. Сечение: 0,04 мм2.
Если мы рисуем линию в 1мм, то объем экструзии будет 0,04 мм3.
Делим: 1,6629942210950816945911112958882 шагов
Проблема в том, что двигатель не может сделать 1,66 шага. Или 1 или 2. Слайсер про количество шагов двигателя ничего не знает и передает в G код реальную длину прутка. Прошивка должна решить, что делать дальше.
Но у прошивки тоже вариантов не много. Все-равно все сводится к тому, дернуть двигатель еще на один шаг или не дернуть. Можно дернуть, в расчете на то, чтобы потом, на следующем интервале, использовать остаток пластика и получить выпучивание на этом интервале. Или не дернуть, и получить нехватку на этом интервале. А если брать интервалы короткие, по 0.1мм, например, как на кривых, то там картина становится еще более печальной.
Но даже и на прямых есть затруднения, за счет наличия ускорений, так как в этот момент надо изменять скорость подачи пластика, а также есть интервал в конце, когда получается не целое число шагов экструзии.
Часть проблем с прямыми решает LIN ADVANCE. Реально помогает более менее крупными отрезками. Но на мелких деталях эффекта не видно, что и понятно.
Единственный путь это уменьшение объема эксктрузии на 1 шаг. Делать пруток меньше не практично, разумеется. А вот уменьшить длину проталкивания на шаг довольно просто. Можно нарастить количество микрошагов (сделать, например, 1/64 или даже 1/128, но это сильно снижает силу проталкивания на 1 микрошаг, что может привести к пропускам микрошагов, которые даже заметить будет невозможно. Другой пусть – использование шестеренок на прямом сцеплении или на ремне. Использование ремня лучше, так как сразу решает проблему с люфтом.
Например, при использовании шкивов на 16 и на 80 получает соотношение 1:5. Т.е. на 1мм будет уже не 1.66 шага, а 8,3. Да, проблема конца интервала не решается, но ее решить и невозможно, при конечном соотношении зубов шкивов. Но чем, чем выше – чем точнее. В процентном соотношении при 100 шагах на интервале в 1мм ошибка по объему экструзии может достигать 39%, а при 500 шагах максимум 8%.
Кроме этого, получаем увеличение в силе проталкивания в 5 раз, т.е. сокращение вероятности механических пропусков или пропусков микрошагов.
Теперь касательно калибровки.
Во многих инструкция по калибровке экструдера предлагается посчитать отклонение от требуемой длины, умножить на коэффициент количество шагов и ввести полученное дробное число в настройки прошивки. Да, это точно поможет на длинных интервалах, но на мелких деталях это не даст значительного эффекта, так как реальных шагов может быть только целое число.
В слайсерах есть два параметра: диаметр прутка и коэффициент подачи. Я заметил, что многие используют второй, для точного подгона. Но синтетический метод, уводящий в сторону от понимания проблемы. Надо фактически измерять пруток, чтобы было ясно его сечение. При правильном калибровке подачи и правильном измерении диаметра, печать должна быть хорошей при коэффициенте подачи именно в 100%.
О том как жить
Основная масса моделей для печати имеет размеры кратные 1мм. Т.е. выбрав механизм подачи прутка обеспечивающий минимальную ошибку именно на таких расстояниях на лучшем слое (например 0.1мм), можно получить чуть выше качество в среднем.
К сожалению, пруток тоже далеко не идеален. Супер, если диаметр колеблется от 1.75 до 1.76, а там и до 1.77 может доходить (т.е. имеет размер 1.76 +-0.01). Рассмотрим пример при соотношении передачи 1:3 (как у титана) и двигатель на 1/16. Получаем 300 шагов на мм. Слой 0.1, ширина 0.4, длина 1мм. Расчетный объем 0,04 мм3.
При прутке ровно 1,75, получаем 5 шагов с ошибкой объема +0.2%. Любопытно, что e3d именно это соотношение выбрали, так как именно оно дает минимум ошибки на 1мм.
Если же диаметр прутка по факту составил 1,76, то ошибка объема экструзии будет уже +1.4%.
Экструдеры — обзор | Темы ScienceDirect
1 Введение
Экструдеры используются для изготовления широкого спектра пищевых продуктов. Их конструкция и технические характеристики должны быть адаптированы к предполагаемому применению, от простых форм, таких как макаронные изделия, до экструдеров для очень короткой варки кукурузных завитков, до более сложных и длинных экструдеров, включающих несколько операций и приводящих к значительным модификациям экструдированного материала. Материал, подаваемый в экструдеры, может включать один твердый или множество твердых и жидких ингредиентов.Твердые ингредиенты — это в основном зерно, бобовые и корнеплоды, подсластители, минералы и витамины. Они используются с различным гранулометрическим составом. К жидкостям относятся вода (почти всегда), масло, жидкие подсластители и красители. Ингредиенты обычно смешивают, превращают в расплав / тесто и формуют в продукт желаемой формы. Между ингредиентами корма, конструкцией экструдера и условиями эксплуатации существует большая взаимосвязь. Понимание принципов конструкции экструдера в виде упрощенного и практичного подхода должно привести к более быстрой разработке продукта, повышению качества и согласованности, эффективности обработки и оптимальной работе.
Существует два основных типа экструдеров; одно- и двухшнековые (вращающиеся в одном направлении и в противоположных направлениях). Они поставляются с широким диапазоном диаметров винтов ( D ), длины ( L ) и конструкций. Одношнековый и двухшнековый, вращающийся в одном направлении, по своей сути являются экструдерами с открытыми в осевом направлении каналами. Их можно рассматривать как насосы с сопротивляющимся потоком. На их производительность или степень заполнения (если они не работают с максимальной объемной скоростью) может влиять напорный поток внутри экструдера. Двухшнековые экструдеры с плотным зацеплением, вращающиеся в противоположных направлениях, образуют закрытые каналы в зоне зацепления.Их выход менее уязвим для давления внутри экструдера. Таким образом, их можно рассматривать как поршневые насосы прямого вытеснения.
Эта глава намерена развить предыдущую главу, также написанную Яку (2012). Его цель — разбить процесс экструзии на отдельные части, описать их функции и рабочие параметры, удовлетворить потребности процесса и обеспечить логичный и простой подход к процессу выбора и проектирования. Конструкция экструдера должна улучшаться по мере накопления опыта и лучшего понимания характеристик материала, реологии, реакций трансформации и взаимодействия с конструкцией системы и рабочими параметрами.
Пищевые экструдеры используют тепловую и механическую энергию. Понимание требований к потреблению энергии и потребляемой мощности очень важно для повышения производительности и экономичного проектирования системы. Вода является обычным ингредиентом почти во всех рецептурах для экструзии пищевых продуктов. Это влияет на характеристики ингредиентов, поведение при плавлении и реологию сформированного теста. Часть этой воды может иногда применяться в виде пара, что влияет на общую подводимую энергию экструдера, производительность экструдера, конструкцию системы и рабочие условия.Обе формы воды можно напрямую дозировать в экструдер и / или в смесительное устройство для предварительного кондиционирования. Возможность включения пара может существенно повлиять на выбор, конструкцию и производительность экструдера, а также на характеристики продукта.
К важным конструктивным параметрам экструдера относится соответствующий выбор шнековых элементов и секций цилиндра. Конструкция шнеков и цилиндра влияет на их функциональные характеристики, а именно на транспортировку, смешивание, плавление и дозирование, а также на характеристики продукта.На практике можно предложить более одной конструкции и режима работы системы для производства одного и того же продукта. Оптимальный выбор, вероятно, будет определяться доступностью, гибкостью и экономичностью.
Комбинированная экструзионная варка и холодное формование невспененных продуктов — это распространенный процесс, используемый для изготовления закусок, круп и других продуктов. Ускоренное охлаждение перед заключительным этапом формования имеет решающее значение в таких операциях. Обычно это достигается за счет испарения части жидкой воды на стадии вентиляции либо внутри одного экструдера, либо между варочным аппаратом и формовочным экструдером.Выбор и конструкция такой ступеньки кратко описаны в этой главе.
Когда экструдированный продукт разрабатывается на базе небольшого производства, масштабирование становится частью общего процесса выбора и проектирования экструдера. Кратко обсуждается влияние на процесс масштабирования с указанием важных факторов, ограничений и дополнительных вариантов процесса.
Узел фильерной плиты является частью общей конструкции экструдера. Он отвечает за формирование желаемой формы продукта и действует как сопротивление потоку, таким образом влияя на производительность экструдера / степень заполнения, подвод энергии и получаемые в результате преобразования материалов.Будет кратко описана конструкция узла штампа, определены его важные компоненты и рабочие функции.
Наконец, в этой главе будет описана и рекомендована общая конструкция и принцип работы экструдера для определенных пищевых продуктов, в основном определяемых по полю их вязкости, определяемой концентрацией влаги в исходном материале.
Как добиться максимальной производительности и эффективности вашей экструзионной линии, часть I
Инжир.1 — Подача потоком полностью заполняет каналы шнека и использует всю длину шнека. Он не требует дополнительного оборудования для кормления, но обеспечивает меньший контроль процесса.
Рис. 2 — Кормление голодом требует питателя, но обеспечивает больший контроль процесса и имеет тенденцию к снижению температуры плавления.
Рис. 3 — Этот пример из операции экструзии трубы показывает, что степень недостаточной подачи обеспечивает более равномерную толщину стенки.Подача паводка достигается при 100% заполнении; меньшее — голодное кормление.
Рис. 4 — Каждая смола имеет определенное потребление энергии (SEC) на нагрев и плавление. В идеале винт обеспечивает от 80% до 90% этой энергии. Если он обеспечивает больше, чем SEC, тогда требуется охлаждение для отвода избыточного тепла, что неэффективно и потенциально разрушает пластик. Точка аутогенной экструзии — это место, где винт обеспечивает точно 100% SEC для пластика.Все, что указано выше, указывает на «гиперактивный» винт.
Рис. 5 — Относительно быстрый способ оптимизации температуры ствола — динамическая оптимизация — т. е. произвести большое изменение уставки и измерить изменение температуры и давления со временем. В этом случае одно изменение температуры с 390 F до 300 F показывает, что оптимальная уставка для зоны ствола 1 составляет около 330 F.
Предыдущий СледующийДля достижения того, что я называю эффективной экструзией, необходимо многое сделать.Для качественного и стабильного процесса вам нужны хорошие люди, управляющие производством и управляющие производством. Оборудование должно быть в хорошем состоянии, должна существовать комплексная программа профилактического обслуживания, а конструкция оборудования должна обеспечивать его эффективную работу. Эффективная экструзия требует хорошей производственной дисциплины, когда люди уделяют внимание деталям и всегда стараются улучшить процесс. Успешная экструзия — это не правильное выполнение двух или трех вещей, а правильное выполнение сотен вещей.
ТРИ М
Эффективная экструзия требует надлежащего оборудования. Здесь наиболее важными переменными процесса являются «три М»: давление расплава, температура плавления и нагрузка двигателя. Они являются жизненно важными признаками процесса экструзии. Их необходимо постоянно измерять и контролировать. Также следует измерять и контролировать следующие параметры:
- Температура ствола и матрицы,
- Скорость шнека,
- Потребляемая мощность в каждой зоне нагрева или охлаждения,
- Температура окружающей среды,
- Относительная влажность,
- Температура сырья на входе в экструдер,
- Уровень влажности сырья, поступающего в экструдер (если гигроскопично),
- Расход охлаждающей воды через питающий корпус,
- Температура воды на входе в подающий корпус,
- Температура воды на выходе из загрузочного корпуса,
- Уровень вакуума на вентиляционном отверстии (если применимо).
Расход воды в корпусе подачи плюс температуры на входе и выходе позволяют количественно определить степень охлаждения. Если охлаждающие каналы в загрузочном корпусе покрываются отложениями кальция, теплопередача будет постепенно ухудшаться, что существенно влияет на производительность экструдера. Если скорость охлаждения загрузочного корпуса не измеряется, очень трудно связать ухудшение характеристик экструдера с плохой теплопередачей в загрузочном корпусе.
ПОЛУЧИТЬ ДАННЫЕ
Возможность сбора данных (DA) имеет решающее значение для разработки надежного процесса экструзии, поддержания согласованности процесса, оптимизации процесса и эффективного устранения неполадок. К счастью, современные недорогие компьютеры и широко доступное программное обеспечение DA позволяют установить высокопроизводительную систему DA на существующие экструзионные линии. К сожалению (и это загадочно), сравнительно небольшое количество процессоров используют эту возможность.
Недавно я работал с процессором, чтобы установить систему DA на базе ПК на относительно старой экструзионной линии.Стоимость системы DA составила менее 20 000 долларов. Примерно за три месяца процент брака на этой линии упал с 15% до 5%. В результате система DA окупилась за несколько месяцев и теперь позволяет процессору постоянно работать со значительно меньшим процентом брака на каждой линии.
Уровень брака был снижен, поскольку с помощью системы DA процесс можно было оптимизировать так, как это было невозможно раньше. Кроме того, проблемы, которые могут привести к появлению некондиционного продукта, можно было немедленно выявить и исправить до того, как продукт, не отвечающий техническим требованиям, действительно был произведен.Это не ракетостроение! Это просто использование легкодоступных инструментов и их эффективное использование. Старые экструзионные линии часто могут производить хорошие продукты, если они содержатся в хорошем состоянии и имеют хорошие контрольно-измерительные приборы и средства управления с возможностью DA.
Консистенция подаваемого материала и поток подаваемого материала в экструдер имеют решающее значение для достижения стабильности процесса. Вариации исходного материала (например, различные уровни измельчения) неизменно приводят к изменениям в процессе экструзии.Даже такие, казалось бы, незначительные проблемы, как гранулометрический состав гранул, могут повлиять на процесс. Как правило, более узкое распределение гранул по размеру повышает стабильность процесса экструзии.
ВАРИАНТЫ ПОДАЧИ
Существует два основных метода кормления: кормление из воды и кормление голодом. При заливной загрузке загрузочная воронка заполняется до определенного уровня, материал течет в экструдер массовым потоком (большую часть времени), и экструдер вбирает столько материала, сколько может откусить.Винтовой канал почти сразу имеет тенденцию заполняться полностью (см. Рис. 1). В результате при заливной подаче эффективная длина шнека более или менее равна длине шнека в горизонтальном положении.
При голодной загрузке полимер дозируется в экструдер подающим устройством (рис. 2). В бункере нет скоплений; вместо этого материал падает прямо в шнековый канал, и шнековый канал только частично заполнен у загрузочного отверстия. По мере продвижения материала вперед канал шнека будет полностью заполнен на некотором расстоянии после подачи.
В результате при голодной подаче эффективная длина шнека меньше, чем длина шнека в горизонтальном положении. Важным преимуществом является то, что эффективную длину шнека можно регулировать во время работы экструдера. Это позволяет более широко контролировать процесс, чем при заливной подаче, где эффективная длина не регулируется. Кормление голодом выгодно только в том случае, если экструдер достаточно длинный для достижения полного плавления и эффективного перемешивания. Следовательно, голодная подача обычно не дает улучшений процесса на коротких (длинных 25D) экструдерах.Для кормления голодом требуется питатель, но он снижает нагрузку на двигатель, температуру плавления и вероятность агломерации, образования мостиков и сегрегации в бункере.
Кормление голодом позволяет оптимизировать процесс на уровне, который невозможен при кормлении потоком. На рисунке 3 показан пример операции экструзии трубы, где изменение толщины стенки было измерено на нескольких уровнях заполнения. Стопроцентное заполнение представляет собой кормление паводком; в то время как значения меньше этого указывают на голодное кормление. Процент заполнения — это фактическая скорость подачи по отношению к скорости подачи заливкой.
Очевидно, что оптимальные технологические условия для минимизации вариации толщины стенок составляют около 98% заполнения. Изменение толщины стенки при оптимальной степени голодания примерно вдвое меньше, чем при питании паводком. Это означает, что при оптимальных условиях можно использовать меньше материала, поскольку труба может быть изготовлена с толщиной стенки, близкой к минимальному значению. В этом случае одна только экономия материала составила около 100 000 долларов в год.
Окружающая среда на заводе также играет важную роль в процессе экструзии.Изменения комнатной температуры и относительной влажности могут повлиять на процесс. То же самое и с воздушными потоками: открытие двери или окна может изменить условия теплопередачи вокруг экструдера и вызвать сдвиг в технологическом процессе. Включение или выключение вентилятора в непосредственной близости от экструдера может вызвать аналогичное изменение процесса. Поскольку события такого рода обычно не отображаются на приборной панели, может быть нелегко найти источник такого изменения процесса.
СКОРОСТЬ ВИНТА И НАСТРОЙКА БОЧКА
Экструдер работает наиболее эффективно, когда шнек обеспечивает от 80% до 90% энергии, необходимой для нагрева и плавления пластика.В таких случаях нагреватель ствола обеспечивает от 10% до 20% дополнительного тепла. Иногда винт обеспечивает более 100% энергии, необходимой для нагрева и плавления пластика. Мы можем назвать это «гиперактивным» винтом. Здесь охлаждение ствола необходимо для контроля температуры.
Охлаждение бочки нежелательно, потому что оно тратит впустую энергию и, конечно же, энергия не бесплатна. На рисунке 4 показано, как удельное потребление энергии (SEC) в кВтч / кг изменяется в зависимости от скорости вращения шнека. У каждого пластика есть определенная потребность в энергии для нагрева и плавления.Для полукристаллических пластиков это значение составляет около 0,15 кВтч / кг, для аморфных полимеров — около 0,10 кВтч / кг.
Изогнутая линия на рис. 4 представляет комбинацию фрикционного и вязкого нагрева винтом. Это часто называют нагревом сдвигом, хотя этот термин не совсем правильный. При низкой скорости вращения шнека нагрев шнека невелик, и нагреватели цилиндра должны вносить значительный вклад. При более высокой скорости вращения шнека большая часть тепла (от 80% до 90%) выделяется винтом — это предпочтительный рабочий диапазон.
При дальнейшем увеличении скорости винта она пересекает горизонтальную линию, которая указывает на требования SEC для пластика. Эта точка пересечения называется точкой аутогенной экструзии. В этот момент все тепло вырабатывается винтом, и нагреватели цилиндра больше не должны выделять тепло. За пределами этой аутогенной точки винт выделяет больше тепла, чем необходимо — он становится гиперактивным. Когда скорость вращения шнека превышает точку перехода, цилиндр необходимо охладить, чтобы отвести избыточное тепло, передаваемое винтом.
Когда цилиндр охлаждается, температура расплава в экструдере будет выше заданного значения температуры цилиндра, потому что тепло течет изнутри цилиндра наружу. Когда происходит небольшое охлаждение, температура расплава может быть на 10–50 ° F выше заданного значения. При среднем охлаждении температура расплава может быть на 50–100 ° F выше заданного значения. Когда охлаждение все время идет на полную мощность, фактическая температура расплава может быть на 100–150 ° F выше заданного значения или даже выше.Поскольку температуру плавления в этот момент, как правило, невозможно измерить, большинство переработчиков не осознают, что такая ситуация может быть вредной.
Важно понимать, что необходимость охлаждения подразумевает перегрев пластика. Это увеличивает риск разрушения пластика и образования черных пятен, гелей и обесцвечивания. Это также снижает прочность расплава на выходе из фильеры и затрудняет охлаждение экструдата. Запуск экструдера с охлаждением цилиндра похож на вождение автомобиля с нажатой педалью тормоза — это расходует энергию и приводит к чрезмерному износу.
Эффективная экструзия требует тщательной оптимизации температуры цилиндра. Многие компании не уделяют должного внимания температурному профилю ствола. Существуют различные подходы к настройке температуры ствола. Эффективным методом оптимизации температуры цилиндра является динамическая оптимизация (см. Plastics Technology, май 2008 г., стр. 72, или на сайте ptonline.com). Этот метод включает в себя большое изменение уставки и отслеживание того, как фактические изменения температуры и давления меняются со временем.На рисунке 5 показано, как изменение давления изменяется в зависимости от температуры при изменении уставки с 390 F на 300 F.
В случае, показанном выше, оптимальная уставка для зоны цилиндра 1 составляет около 330 F. Этот метод нахождения оптимальной уставки быстрее, чем внесение небольших изменений в уставку и ожидание реакции экструдера на это изменение уставки. Для больших экструдеров может потребоваться 30 минут или больше, чтобы машина отреагировала на изменение уставки. Если было сделано шесть изменений, экструдеру может потребоваться три часа или больше, чтобы отреагировать на эти изменения.
Об авторе
Крис Раувендал работает в сфере экструзии более 37 лет. Он возглавляет собственную инженерную фирму в Оберне, Калифорния, которая предоставляет индивидуальные винты и матрицы, обучение и услуги по устранению неполадок. Автор приветствует вопросы и комментарии читателей по электронной почте [email protected].
Зачем и как определять основу для вашего экструдера
Знаете ли вы, какой будет ожидаемая производительность при установке нового экструдера или установке нового шнека в существующую машину? Вам следует.Если вы не ориентируете свой экструдер, как вы собираетесь установить реалистичные ожидания в отношении его производительности?
Если шнеки экструдера спроектированы должным образом, они обычно способны выдерживать максимальный крутящий момент, доступный от экструдера и обрабатываемой смолы. Экструдер должен работать примерно на 90% от своего полного доступного крутящего момента, исходя из 100% гранул, что обычно является наихудшим сценарием. Используя сегодняшнюю технологию барьерных шнеков, можно получить более высокую производительность, более низкие температуры плавления и более высокую энергоэффективность.
Эта статья предоставит некоторые основные сведения, чтобы помочь переработчикам определить, получают ли они максимальную производительность от своих экструдеров, при условии, что у них есть соответствующее оборудование для охлаждения и обработки в экструзионной системе.
ОЖИДАЕМЫЕ ПРОИЗВОДИТЕЛЬНЫЕ СТАВКИ
Двадцать лет назад 3,5-дюйм. Предполагалось, что экструдер (90 мм) с соотношением L / D 24: 1 будет производить от 500 до 550 фунтов / час HDPE, если он был оснащен двигателем мощностью 125 л.с. и редуктором с максимальной скоростью 125 об / мин.2,5 дюйма Предполагалось, что экструдер (65 мм), 24: 1 будет получать от 200 до 225 фунтов / час HDPE с двигателем мощностью 60 л.с. и редуктором с максимальной скоростью 125 об / мин.
В настоящее время 3,5-дюйм. экструдер с двигателем мощностью 150 л.с. может производить от 650 до 700 фунтов / час при 125 об / мин и обеспечивать температуру плавления от 410 F до 420 F при среднем давлении на головке 4000 фунтов на квадратный дюйм для HDPE с фракционным плавлением. 2,5 дюйма Машина должна обеспечивать производительность в диапазоне от 250 до 275 фунтов / час. Этого можно достичь, используя современные барьерные технологии vs.старый одноступенчатый шнек со смесителем Maddock (он же LeRoy или Union Carbide).
Но всякий раз, когда к сырью добавляется измельченный материал, производительность падает пропорционально процентной разнице в общей объемной плотности сырья. Таким образом, если 100% гранулы загружаются в экструдер с насыпной плотностью 32 фунта / фут3, а смесь гранул и измельченного материала весит всего 29 фунтов / фут3, фактическая производительность может снизиться примерно на 10% при всех других условиях. быть таким же.
ЧТО ДЕЛАТЬ ПЕРВЫЙ
При покупке нового экструдера или нового шнека спросите продавца, какую «теоретическую» пропускную способность вы должны ожидать, а также спросите, какой температурный профиль они порекомендуют для материала, для которого был разработан шнек.
Раньше при использовании одноступенчатого шнека с миксером Maddock большинство операторов экструзии использовали либо «плоский» профиль температуры цилиндра, либо профиль «возрастающей рампы». Эти температурные профили работали, но они не были оптимальными.
Используя сегодняшнюю технологию барьерных шнеков, необходимо использовать гораздо более сложные профили температуры цилиндра для оптимизации рабочих условий экструдера. Сегодня многие эксперты рекомендуют использовать температурный профиль «горба», в котором первая зона ствола установлена на нормальную настройку зоны 1, а зона 2 установлена на 75–100 ° F выше, а затем остальные зоны уменьшаются. равномерно по температуре до точки, при которой последняя зона цилиндра устанавливается примерно на 10 ° F ниже желаемой температуры плавления.График на рис. 1 показывает разницу в производительности, которая может быть достигнута при использовании правильного температурного профиля при обработке HDPE на 2-дюймовом. экструдер. Увеличение пропускной способности на 53% наблюдалось при использовании температурного профиля «горба» по сравнению с «наклонным» профилем, а увеличение на 14% было достигнуто по сравнению с «плоским» температурным профилем.
На Рисунке 2 показан типичный профиль, используемый на шнеке барьерного типа, обрабатывающем фракционный расплав ПЭВП. Все расположенные ниже по потоку переходные зоны и зоны фильеры должны быть изначально установлены близкими к желаемой температуре плавления, а затем оптимизированы для получения наилучших результатов.Основываясь на лабораторных исследованиях, указанные выше настройки температуры будут обеспечивать температуру расплава от 410 F до 420 F, как показано на рис. 3.
Обратите внимание, что для обеспечения максимальной точности температуру расплава всегда следует измерять с помощью ручного пирометра. Использование иммерсионных датчиков в адаптере потока или инфракрасных пистолетов часто приводит к ложным показаниям из-за присущих им ограничений. Но эти ограничения можно исправить с помощью правильной техники. Например, погружные датчики температуры расплава должны входить примерно на одну треть в отверстие переходника для потока расплава.Например, если адаптер потока имеет 1-дюйм. диаметра отверстия зонд должен входить в полимер примерно на 5/16 дюйма, как показано на рис. 4.
Когда полимер течет через отверстие, он всегда будет центрировать поток, то есть скорость потока выше в центре потока, чем у краев. Температурный градиент в потоке расплава будет иметь параболическую конфигурацию с более низкой температурой у стенки и более высокой температурой расплава в центре. Если зонд расплава вставлен примерно на 33% в поток расплава, он обеспечит более точную общую температуру расплава.Обратите внимание, что поверхностные датчики температуры расплава, устанавливаемые заподлицо, на самом деле не будут измерять температуру плавления текучего полимера, но, скорее всего, будут измерять температуру металла адаптера.
Что касается инфракрасных пистолетов, это правда, что они удобны, а иногда и являются единственным способом измерения температуры расплава во время производства экструдера. Но если излучательная способность пистолета не установлена должным образом или если есть шум от каких-либо фоновых объектов, они могут дать ложные показания температуры плавления.
Показания температуры погружного зонда и ИК-пистолета следует использовать только как относительные, а не как истинные абсолютные значения.
слов для жизни: Температура плавления полимера может варьироваться в зависимости от того, где она измеряется, как это измеряется и кто проводит измерения.
СБОР ДАННЫХ
После установки нового экструдера или шнека бункер должен быть полностью заполнен материалом, для которого был разработан шнек, и должна быть проведена серия проверок скорости для определения базовой производительности системы экструдера.
Обычно эта серия проверок скорости должна выполняться при 20%, 40%, 60%, 80% и 100% полной скорости шнека или 25%, 50%, 75% и 100%, в зависимости от размера экструдера. , сколько смолы вы можете позволить себе пожертвовать и сколько времени. По правде говоря, количество смолы, используемой для базовой линии экструдера, в конечном итоге невелико, потому что сроки тестирования относительно короткие.
При каждой скорости вращения шнека следует взять три 2-х минутных пробы для взвешивания. На более крупных экструдерах — 4.5 дюймов (115 мм) и более — время отбора пробы может быть сокращено до 1 минуты для сохранения материала, но 2 минуты всегда лучше. Затем каждый образец следует взвесить на наборе цифровых весов, которые обеспечат точность по крайней мере до одного десятичного знака. Не используйте весы для поддонов, которые, к сожалению, слишком распространены, потому что эти весы будут измерять только в пределах ± 0,5 фунта. Например, если 2-минутный образец взят из 3,5-дюймового. экструдер со скоростью 20 об / мин, и он взвешивается на весах поддона, показывающих 4 фунта, реальный вес может быть где угодно от 3.От 7 до 4,3 фунта. Этот поворот означает расчетный диапазон пропускной способности от 111 до 129 фунтов / час, что является существенной разницей. И наоборот, если цифровые весы с однозначным показателем обеспечивают диапазон веса от 3,9 до 4,0 фунтов для 2-минутного образца, это дает расчетную пропускную способность от 117 до 120 фунтов / час.
Теперь, когда метод сбора данных о пропускной способности прояснен, другая информация, необходимая для определения базовых параметров экструдера:
• Скорость шнека
• Частота отбора проб (фунт / 2 мин)
• Частота отбора проб (фунт / час)
• Температура расплава
• Ампер двигателя привода (или процент нагрузки)
• Давление на головке
• Настройки зоны цилиндра
Все это можно легко зафиксировать в простой электронной таблице.При настройке стола используйте «S» и «A», чтобы различать «Установленную» и «Фактическую» настройки температуры ствола. Если тестирование проводится в течение длительного периода времени, вы можете наблюдать переопределение зон, что всегда следует отмечать.
После сбора всех этих исходных данных во время установки нового шнека или экструдера их можно затем сравнить с будущими данными. Если становятся очевидными какие-либо отклонения, такие как более высокая температура плавления, снижение производительности или обход зоны, эту информацию можно использовать для определения необходимости профилактического обслуживания, такого как восстановление шнека или замена цилиндра.
ЧТО ЭТО ВСЕ ОЗНАЧАЕТ
Когда исходные данные собираются сразу после установки нового шнека или экструдера, эта информация может оказаться бесценной в будущем. А если один и тот же метод испытаний используется на периодической основе, обычно каждые шесть месяцев, то профилактическое обслуживание может быть запланировано более эффективно, а любые изменения в производстве могут быть лучше объяснены.
Если пропускная способность отслеживается на регулярной основе, как показано на рис.5, тогда капитальные затраты на новый шнек или цилиндр можно лучше спрогнозировать, и они не станут неожиданным сюрпризом, который может вызвать длительный останов экструзионной системы до тех пор, пока не будут поставлены новые заменяемые компоненты. Как показано на рис. 5, если бы процессор заказал новый винт примерно в июле 2009 г., он не увидел бы значительных потерь в производстве, которые он испытал.
Если вы потратите час времени во время остановки на сбор данных каждые шесть месяцев, а затем сведение всей информации в таблицу, это может существенно повлиять на общую прибыль компании в конце года.
Что такое экструзия? | Plastics International News and Blog
Слово экструзия взято из латинского слова extrudere, означающего (ex) наружу и (trudere) толкать. В процессе экструзии гранулы или сухой пластиковый порошок нагревают и продавливают через фильеру. Большая часть экструзии выполняется с помощью шнеков, хотя экструзия с плунжером все еще используется специально для порошков СВМП. Винты плавятся, перемешивают материал и выталкивают его из отверстия в матрице.Экструдер может быть одноцилиндровым или двухшнековым / двухцилиндровым. Экструзионный материал определяет, какая технология экструзии требуется. Двухкамерные экструдеры в основном используются для смешивания основных пластмасс с различными пластификаторами, наполнителями, красителями и другими ингредиентами. Экструзия позволяет производить трубы, стержни, профили, пленку или листовой пластик различной ширины и толщины.
Экструзия — один из основных способов изготовления пластмассовых изделий на станках.Экструзия имеет несколько преимуществ:
— Высокая производительность (по сравнению с другими процессами) обеспечивает более низкие материальные затраты.
— В зависимости от объема может быть больше вариантов ширины и длины для увеличения урожайности.
— Относительно низкие затраты на инструмент.
Экструзия может иметь некоторые недостатки:
-Пределы толщины для некоторых материалов.
— С точки зрения механической обработки, материал может иметь более высокий уровень напряжения при вторичном или постпроизводственном отжиге, необходимом для снятия напряжений, чтобы форма заготовки была более поддающейся механической обработке.
— Трудно достичь формы с жестким допуском.
— Ограничено формами равномерного поперечного сечения (по длине).
Экструзия — один из наиболее распространенных способов изготовления пластиковых заготовок. Обработка заготовок такой формы при использовании авторитетного экструдера с использованием материалов высочайшего качества может стать успешной частью бизнеса любой мастерской. Чтобы найти самый широкий выбор качественных заготовок для обработки, просто нажмите здесь.
Что такое экструзия пластика? | Предпочтительные пластмассы
Вы когда-нибудь задумывались, как изготавливаются окна из композитных материалов, виниловые ограждения или прокладки для морозильных камер? Эти и многие другие продукты производятся с использованием крупносерийного производственного процесса, называемого экструзия пластика .
Экструдер является частью оборудования, лежащим в основе этой технологии производства. Экструдеры состоят в основном из следующих компонентов:
- A ручной или вакуумный бункер , который удерживает и подает сырье из пластмассы.
- Длинный ствол с винтовым механизмом, проталкивающим пластик через ствол.
- Внешние нагреватели , которые помогают поддерживать желаемую температуру внутри ствола.
- Матрица , которая формирует профиль изготавливаемой пластмассовой детали.
Предпочтительный процесс экструзии пластмасс
Процесс экструзии пластика начинается, когда полимерные соединения и добавки в форме гранул, хлопьев, гранул или порошков непрерывно подают через бункер в экструдер. Винт постепенно перемещает эти материалы по цилиндру, и в процессе вырабатывается достаточно тепла, чтобы расплавить пластик. Внешние нагреватели помогают поддерживать желаемую температуру при движении расплавленного пластика через ствол.
Когда расплавленный пластик выходит из ствола, он проталкивается через матрицу, которая придает ему желаемый профиль. Секция охлаждения помогает сохранить профиль, пока пластик схватывается и затвердевает.
Преимущества экструзии пластика
Экструзия пластмасс является непрерывной и позволяет выпускать большие объемы продукции, что делает ее более экономичным методом производства пластмасс по сравнению с другими процессами. Кроме того, стоимость инструментов относительно невысока.
Экструзия пластика особенно хорошо подходит для производства пластиковых деталей с одинаковой толщиной стенок, а также для профилей, которые шире и длиннее, чем профили, производимые другими видами производства.Пластиковые пленки, пакеты, трубопроводы, трубки, стержни, уплотнители и перила палубы — это лишь некоторые из многих продуктов, которые успешно и экономично производятся методом экструзии пластика.
Возможности экструзии пластика на заказ
Preferred Plastics — ведущий в отрасли экструдер для пластмасс по индивидуальному заказу, предлагающий услуги экструзии и отделки под ключ. За последние 40 лет мы заработали мировую репутацию в области экструзии пластмассовых деталей высокого качества в соответствии с самыми строгими требованиями.Наши инновационные процессы экструзии поддерживаются превосходным обслуживанием клиентов и стремлением производить детали, соответствующие самым высоким стандартам качества и доставляемые вовремя и в рамках бюджета. Свяжитесь с нами сегодня!
Предлагаем:
- Экструзионные профили — нестандартные формы и размеры для удовлетворения требований для широкого спектра отраслей и областей применения
- Профили для труб — специальные профили для труб для широкого спектра промышленных и бытовых применений
- Коэкструзия — использование двух или более смол для производства деталей, отвечающих строгим требованиям к рабочим характеристикам
- Экструзионные крейцкопфы — обеспечение усиления детали или герметизация металлических деталей внутри экструзии
Свяжитесь с Preferred Plastics Today
Если вы ищете метод производства пластмасс, обеспечивающий высокое качество, большие объемы, большие возможности профиля и хорошую экономичность, рассмотрите возможность экструзии пластмасс компанией Preferred Plastics.Свяжитесь с нашей командой сегодня, чтобы запросить смету проекта: 269-685-5873 .
Руководство по экструзии| Пластмассы
На рынке существует ряд уважаемых публикаций, посвященных процессу экструзии, но многие из них сосредоточены на теории, а не на реальности, что делает их непрактичными для операторов или слишком академичными для образовательных и обучающих целей. В отличие от этого, наше Руководство по экструзии (EGB) предназначено для того, чтобы дать практические ответы на вопросы операторов относительно экструзии термопластичных материалов.Различные темы будут охватывать основы: «Как экструдировать?» (охватывает наиболее распространенные материалы, такие как ПВХ, ПЭ, ПУ, ПЭТ), ответы на часто задаваемые вопросы, руководства по устранению неполадок и веб-ссылки. Самым простым и распространенным экструдером для экструзии термопластичных материалов является одношнековый экструдер. Поскольку шнек можно рассматривать как сердце одношнекового экструдера, это будет наша первая тема.
Основное изображение: барьерный винт (фото: Groche Technik)
A) Подготовка материала: смешивание, смешивание и сушка
B) Подача экструдера: от голода до силы
C) Экструдер: экструзия материала
D) Оснастка: формовка, калибровка и охлаждение
E) Вторичные процессы
Одинарные шнеки обычно подразделяются на две основные разные конструкции: «трехзонный шнек» (также называемый «дозирующим шнеком») и «барьерный шнек», как с участком смешивания, так и без него (распределительное или дисперсионное смешивание).Важность смешивания становится очевидной, если принять во внимание большое количество добавок, которые можно обрабатывать, таких как технологические добавки (добавки, улучшающие скольжение, термостабилизаторы, смазочные материалы), агенты (антиблокирующие, антистатические, противотуманные), антиоксиданты, пластификаторы и т. Д. пигменты и наполнители среди прочего. Большинство отдельных винтов азотированы для обеспечения базовой износостойкости, но они также доступны с широким спектром поверхностных покрытий для обеспечения повышенной износостойкости (стеллит или колмоной) или химической стойкости (хромирование).Из-за масштаба и сложности элементы смешивания, покрытие поверхности винтов и износ винта будут отдельными темами.
Винт, будь то дозирующий или барьерный, выполняет следующие основные задачи:
- Транспортировка материала вперед (и для создания необходимого давления перед матрицей)
- Нагрев и плавление (за счет сдвига материала)
- Смешивание и гомогенизация расплава
Винтовые клеммы
Глубина канала: расстояние от вершины лестницы до корня
Канал: пространство между витками
Задний фланг полета: задний край витка
Толкающий фланг полета: передний край витка
Шаг: расстояние между последовательными витками
Угол наклона спирали: угловые выступы образуются по линии, перпендикулярной валу винта
Диаметр винта: расстояние между самыми дальними витками на валу винта
Диаметр корня: расстояние от дна канала с одной стороны до дна канала с противоположной стороны
Длина: расстояние от любой шпоночной канавки , бункер или первый виток на наконечник винта
Трехзонный шнек
Этот шнек, обычно длиной от 20D до 28D, имеет три разные секции: подающую секцию, компрессионную (или переходную) секцию и дозирующую секцию.В случае экструдера с вентиляцией, который оборудован вакуумной дегазацией, шнек будет длиннее и будет иметь две дополнительные зоны: зону декомпрессии перед дегазированием и вторую зону дозирования. Трехзонный шнек обычно используется в диапазоне от низкой до средней производительности, а также при обработке материалов, чувствительных к сдвигу (например, ПВХ).
Загрузочная секция имеет глубокие ламели для приема материала из загрузочного отверстия (загрузочного отверстия) и выполняет главную задачу по транспортировке твердых частиц. Эта зона имеет особое значение, поскольку общая производительность экструдера напрямую связана со скоростью транспортировки твердых частиц в этой зоне.Для транспортировки твердых частиц материал должен «прилипать к цилиндру и скользить по винту». Для этого очень важен правильный контроль температуры. Например, если зона подачи настроена на неправильную температуру, возможно, что материал просто перемещается вокруг шнека под горловиной подачи без какой-либо тенденции к продвижению вперед. Секция подачи — это зона, где может возникнуть множество проблем, и где опытный оператор может увеличить производительность с помощью правильного регулирования температуры корня шнека, секции подачи / цилиндра и цилиндра.Секция подачи обычно составляет 4-8 пролетов.
Пролеты компрессорной секции постепенно меняются с глубоких на мелкие. Здесь материал сжимается и расплавляется на длину от 5D до 10D. Дозирующая секция является последней секцией и имеет наименьшую глубину полета и обычно составляет 6-10 полетов. Этот участок нужен для создания необходимого давления перед штампом.
Барьерный винт
Если трехзонный шнек не может завершить процесс плавления и требуется более высокая производительность, можно использовать «барьерный шнек».Этот винт имеет вторичную лопасть (барьерную лопасть) в канале, которая подрезана и позволяет проходить только полностью расплавленному пластику. Сегодня доступно множество различных исполнений этой конструкции барьера, но все они направлены на обеспечение более высокой производительности при низкой температуре расплава. Эта конструкция шнека, представленная более 50 лет назад, сегодня стала ведущей и наиболее широко используемой. Барьерный винт, особенно когда он используется в сочетании с подающей втулкой / секцией с пазами, может значительно улучшить скорость транспортировки твердых частиц (и, следовательно, выход) материалов с низким коэффициентом трения (COF), которые трудно обрабатывать на обычных станках. три зоны-винта.
Барьерный винт (фото: Groche Technik)
Часто задаваемые вопросы
Какая степень сжатия винта?
Степень сжатия — это соотношение между двумя глубинами, глубиной канала подачи и глубиной канала дозирования (степень сжатия = глубина канала подачи / глубина канала дозирования).
Пример:
Глубина канала (секция подачи): 20,5 мм
Глубина канала (секция измерения): 6,2 мм
Степень сжатия: 3,3: 1
Степень сжатия трехзонного шнека можно рассматривать как самый основной параметр при обработке различных полимерных материалов с разными вязкоупругими свойствами.Это соотношение обычно составляет от 1,5: 1 до 4,5: 1. Некоторые полимеры просто лучше работают на винтах со степенью сжатия 2,5: 1, в то время как другие материалы лучше работают на винтах со степенью сжатия 4: 1. Часто используются так называемые винты общего назначения (GP) с соотношением примерно 2,5–3: 1, которые подходят для более широкого диапазона материалов.
Эта степень сжатия относится к глубине каналов. Важно отметить, что эта степень сжатия не показывает, сколько сдвига винт вносит в материал, и два винта с одинаковой степенью сжатия могут иметь существенно разную производительность.И эта степень сжатия по глубине не имеет значения для барьерного винта. Другой подход — это «объемная степень сжатия», которую подробно объясняет Тимоти Уомер в книге «Базовая геометрия винта»: «То, что ваш дизайнер винтов никогда не рассказывал вам о винтах».
Материал — степень сжатия винта (глубина)
Как определяется соотношение L / D?
Отношение L / D — это длина винта, деленная на диаметр винта. Термин диаметр четко определен, но не длина винта, и компании интерпретируют длину по-своему.Производители винтов обычно указывают общую длину винта, начиная от шпоночной канавки, другие измеряют от передней стороны или центра горловины подачи (отверстия подачи), третьи измеряют только эффективную длину винта (длину в плоскости) в местах, где имеются выступы. L / D для шнеков экструдера профиля, где гибкость в производительности имеет приоритет, обычно составляет от 24: 1 до 30: 1, в то время как винты с высокой производительностью, например, барьерные винты для труб и листов, могут составлять 35/38: 1.
Руководство по поиску и устранению неисправностей
Всплеск, приводящий к колебаниям производительности, является наиболее распространенной проблемой, связанной с одношнековыми экструдерами.А поскольку одношнековый экструдер, в отличие от двухшнекового экструдера, не является устройством прямого вытеснения, колебания подачи напрямую приводят к колебаниям производительности. Большинство проблем с помпажами возникает из-за зоны / секции подачи.
Список литературы
Экструзия: полное руководство и справочник по обработке | Гарольд Ф. Джайлс-младший, Джон Р. Вагнер-младший, Элдридж М. Маунт, III
Базовая геометрия винта: «То, что ваш разработчик винтов никогда не говорил вам о винтах» | Тимоти В. Уомер — 1 октября 2007 г.
Фундаментальные концепции экструзионного дизайна | Лу Пиффер (Davis-Standard Corp.)
Центр исследований принципов экструзии, применения продуктов и исследований (Мумбаи)
доставлено вам по
БЕСПЛАТНЫЕ онлайн-курсы BitDegree
— нажмите здесь —
Хотите узнать больше из Руководства по экструзии? [wysija_form id = ”6 ″]
Экструдеры должны быть настроены на все температуры цилиндра, адаптера и головки в соответствии с рекомендациями производителей полимеров.Обычно производители полимеров рекомендуют идеальную температуру расплава, то есть температуру расплава на выходе из фильеры. Все остальные температуры должны быть установлены таким образом, чтобы достичь температуры плавления, рекомендованной для конкретного сорта полимера. Когда используется этот тип рабочих условий, регулирование температуры экструдата полностью зависит от геометрии шнека и вязкого тепла, выделяемого при сдвиге, создаваемом глубиной канала, зазорами между витками и скоростью шнека.
Это особенно проблематично, когда в экструдере используется шнек барьерного типа, который обычно используется в большинстве процессов экструзии для достижения оптимальной производительности и производительности.Барьерные винты — это высокопроизводительные винты, которые требуют более точной настройки профилей температурных зон цилиндра. Теперь в зоне 1 можно установить температуру, которая будет обеспечивать максимальную транспортировку твердых частиц полимера. Зона 1 должна быть установлена примерно на 5–15 ° C ниже температуры плавления, рекомендованной поставщиком полимера, или, как упоминалось ранее, на 5–15 ° C ниже настроек зоны адаптера и фильеры. Для большинства полиолефинов зона 1 должна быть установлена в пределах 100-200 C.Чем выше конечная рекомендуемая температура плавления полимера, тем выше можно установить зону 1. Его следует установить как можно выше, не вызывая при этом перегородки в горле. При достаточном охлаждении в кожухе загрузочного отверстия в зоне 1 можно установить более высокие температуры. Для плавления пластика требуется энергия. Таким образом, зона 2 должна быть установлена на 65-90 ° C выше, чем зона 1. Эта повышенная температура зоны не вызовет более высокой температуры плавления, потому что в этот момент полимер все еще находится в форме гранул. Но более высокая температура в этой зоне даст полимеру больше энергии и поможет расплавить полимер.Энергия может быть передана полимеру посредством механической энергии от шнека или энергии от нагревателей. Подача большого количества энергии через нагреватели цилиндра в задней части экструдера обычно снижает нагрузку на приводной двигатель или силу тока. Температурные настройки, подходящие для полиолефинов для барьерного винта:
При этих рекомендуемых температурах полимер подвергается наименьшей нагрузке. |