Самодельная ременная передача
В конструировании часто применяется ременная передача, чтобы передать момент вращения с привода (вала двигателя) на ведомое колесо или вал. В самодельных конструкциях очень часто сложно подобрать требуемый размер валов и ремней, поскольку конструкции, которые сделанные своими руками редко имеют стандартизированные посадочные отверстия и расстояния между ними могут варьироваться в широком диапазоне.
Быстро и достаточно качественно сделать ременную передачу можно самостоятельно, применяя небольшое количество инструмента и расходных материалов. А качество зачастую приближается к заводским образцам. Для работы потребуются следующие материалы и инструменты*:
— дерево или толстый пластик для создания вала ременной передачи.
— дрель и сверла по металлу
— кусачки-бокорезы
— толстый медный провод с диаметром жилы от 1.5мм и более
— ножовка по металлу
— изолента
— тонкий обмоточный провод диаметром 0.125мм или леска
— резиновый клей, либо герметик
— плоскогубцы
— основание для точной выверки расстояний между деталями
— разметочные инструменты (штангельциркуль, линейка, карандаш и т.д.)
* По ходу статьи могут быть добавлены дополнительные материалы и инструменты.
В первую очередь следует определиться с двумя важными размерами:
— расстояние между центрами валов a
— диаметр валов для передачи d
Первый размер определяет длину ремня, а так же расстояние между приводом и ведомым валом, а второй размер определяет на сколько оборотов будет поворачиваться ведомый вал, если ведущий, к примеру, будет в два раза больше по диаметру. Со вторым размером можно определиться либо по специальным формулам, либо проведя натурные эксперименты. В своей практике я всегда использую одинаковые шкивы при ременной передачи, а если мне требуется увеличить, либо уменьшить скорость вращения ведомого вала, я использую шестерню, которая установлена на одном и том же валу с ведомым шкивом.
На деревянной доске, ширина которой равняется ширине ремня, размечается круг диаметром с будущий диаметр шкива, затем на круге отмечаются отверстия через равные промежутки. Например, на небольшом шкиве достаточно будет 12 отверстий с шагом в 30 градусов. Просверлите отверстия, диаметром с диаметр провода. Далее, возьмите коронку и выпилите шкив так, чтобы срезать половину отверстий. У вас получиться некое подобие шестерни. Если делать шкивы из пластика, тогда следует использовать несколько пластин, склеенных между собой, а далее по технологии, описанной выше. Таким же образом изготавливается и второй шкив.Если он другого размера, больше или меньше ведущего, тогда следует изготовить вначале круглую заготовку шкива, а затем наложить уже готовый ремень и отметить места выемок, которые можно сделать круглым напильником. Теперь приступаем к изготовлению ремня.Для этого обмотайте оба шкива изоляционной лентой примерно в три – пять слоев. Ленту при этом не следует сильно натягивать, обратите внимание, чтобы не было складок, либо перекручивания изоленты.Затем возьмите провод, откусите необходимый кусок, снимите изоляцию. Согните небольшой кусок провода под прямым углом и вложите в отверстие между изоляционной лентой и шкивом.Согните нижнюю часть. Капните немного клея для того, чтобы кусок провода не менял своего положения. Поверните одновременно два шкива и продолжите вставлять куски провода в отверстия, пока весь ремень не сделает полный оборот.Теперь намотайте леску или обмоточный провод виток к витку поверх изоляционной ленты с один-три слоя. Обильно промазывайте резиновым клеем витки провода. Загибайте все провода по образцу канцелярских скоб от степлера.Концы провода должны плотно обжимать изоленту с витками лески. После этого намотайте еще слой обмоточного провода или лески.Далее, намотайте изоленты примерно слой – два. Подготовьте небольшую одноразовую емкость. Дождитесь высыхания клея и опустите готовый ремень в емкость и залейте клеем. Дождитесь, когда клей немного подсохнет и вытащите ремень. Удалите с внутренней и боковых сторон ремня остатки клея и дайте ремню полностью просохнуть в течении не менее 8 часов. Ремень готов.
Чтобы улучшить характеристики ремня на растяжение и предотвратить смещение отдельных зубцов ремня, следует делать слои к примеру из прочной нити, либо тканевой полоски вместо обмотки проводом или леской. Ткань впитает в себя клей и станет очень прочной. Можно комбинировать и экспериментировать с расположением обмоточного материала, применять стекловолокно и вакуумное склеивание. Для этого погрузить ремень в емкость, залить клеем и откачать воздух, в таком случае клей попадет в самую глубину ремня. Чтобы сделать его максимально прочным и при этом гибким, я рекомендую взять использованный, либо порванный ремень ГРМ от автомобиля и внимательно рассмотреть на срезе его структуру, расположение армирующих волокон и т.д.
RegenTech(C)2015
Простой способ изготовления и замены приводного ремня на ножной швейной машинке «Зингер»
Я хочу поделиться своим опытом замены ремня на старой ножной машинке «Зингер». Вернее, опытом создания ремня из подручных средств.
Так получилось, что мне отдали машинку, о которой я давно мечтала. Машинкой давно не пользовались, и выглядит она довольно потрепано. Я не была уверена, в рабочем ли она состоянии. Но при осмотре поняла, что не хватает лишь приводного ремня. И возникла идея соорудить ремень самой из подручных средств.
В строительном магазине я купила канат (так он был назван в магазине) — плотный капроновый шнур диаметром около 1 см.
Затем дома надела шнур на машинку, отметила нужный размер. Для этого пришлось снять ограждение шнура сверху на машинке у махового колеса, это не сложно, оно прикручено на один болтик.
Не убирая шнур, опустила машинку в стол, отрезала шнур не по метке, а убавив его примерно на 1,5-2 см, чтобы потом натяжение было достаточным для прокручивания махового колеса. Зажигалкой опалила концы шнура и, пока они расплавлены и мягкие, быстрым движение придала им круглую форму, чтобы стык был как можно аккуратнее. Взяла иглу с толстым ушком, прочную капроновую обувную нить и сшила концы шнура прямо под столом, не вытаскивая шнур из машинки.
Аккуратно подняла машинку, следя чтобы шнур не выскользнул из желобков маховых колес .
У меня были сомнения, что капроновый канат довольно скользкий и будет проскальзывать на маховом колесе. Но результат превзошел все мои ожидания, машинка справляется с любой тканью, ремень не проскальзывает. На фотографии прошита джинсовая ткань, сложенная в 12 слоев.
Буду рада, если мой опыт кому-то пригодится. Если возникнут вопросы, с удовольствием отвечу.
Токарный станок по дереву своими руками на ременной передаче

Привет всем любителям самоделок. Наверно у каждого мастера своего дела есть инструмент, который часто нужен в работе, например, напильник, но иногда бывает так, что ручка не нем или не устраивает или же совсем отсутствует, и в этот момент необходимо сделать такую ручку, дабы вернуть напильнику работоспособность, вот для этого идеально подойдет токарный станок по дереву, о сборке которого я расскажу в этой статье. Данный станок предназначен для обработки деревянных заготовок, а именно тел вращения, с его помощью можно изготовить различные ручки, ножки, фигурки для всяких самоделок.
[media=https://www.youtube.com/watch?v=JkCzQbqXuU8]
Для того, чтобы сделать токарный станок понадобится:
* Электродрель
* Дубовый паркет
* Алюминиевые профиля
* Шурупы
* Отвертка
* Электродвигатель от швейной машинки
* Велосипедная камера
* Эпоксидный клей
* Сверла
* Ножовка по металлу
* Подшипники
* Металлический уголок
Вот и все, что нужно для того, чтобы собрать токарный станок своими руками, материалы как по мне весьма легкодоступные, сложнее всего мне дался поиск двигателя.
Шаг первый.
Для того, чтобы понимать как будет выглядеть станок и уже представлять будущие размеры необходимо сделать из четырех паркетин каркас, который будет станиной — главной частью, начать лучше именно с него, так как все остальные части будут крепиться на станине. Все четыре паркетины нужно предварительно просверлить, а затем в эти отверстия вкрутить шурупы, образовав прямоугольник.
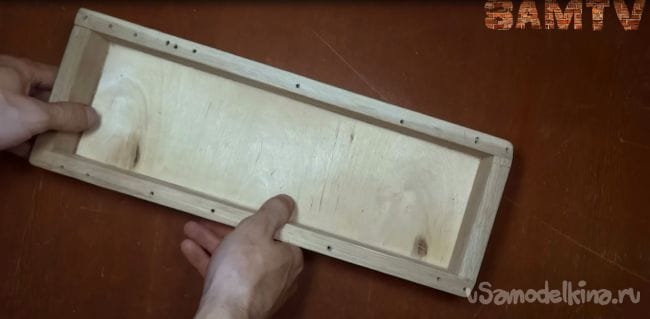
Снизу для сбора стружек я приклеил фанеру, чтобы по окончании работы легко освободить этот отсек для стружек перевернув станок. Для того, чтобы станок при работе не скользил я прикрутил резиновые ножки.
Шаг второй.
Так как в любом токарном станке есть задняя бабка, то и в моем случае она тоже будет, поэтому для того, чтобы ее можно было закрепить на станине понадобятся два алюминиевых уголка, которые нужно подогнать по длине и затем просверлить четыре отверстия в каждой направляющей и прикрутить при помощи шурупов к паркетинам на станине. Перед тем, как закрутить шурупы в станину, необходимо просверлить отверстия сверлом на 1-2мм меньше, чем шуруп, делается это для того, чтобы не образовалось трещин.
Шаг третий.
Пришло время сделать и саму заднюю бабку. Из паркетины выпиливаем кусочек и делаем паз под направляющие. После этого нужно впрессовать или же вклеить две гайки по краям нашей будущей задней бабки. В эти гайки будут вкручиваться барашки и с помощью этого задняя бабка будет фиксироваться в неподвижном положении. Для того, чтобы гайки не вытянуло наружу при сильном затягивании нужно промазать сверху их эпоксидным клеем.
Шаг четвертый.
Пока эпоксидный клей будет сохнуть делаем крепления под подшипники на переднюю бабку. Сделать их я решил также из паркета, сверлим отверстия под подшипники и впрессовываем их на законное место, для надежности можно промазать посадочное место эпоксидной смолой.
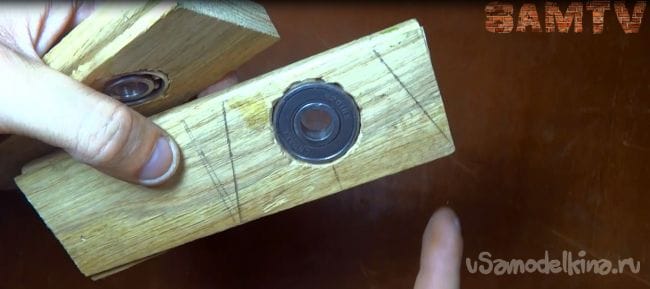

Крепления я сделал в виде равнобедренной трапеции. Основание, на котором будут держаться крепления с подшипниками также делаем из паркета, в нем просверливаем четыре отверстия и прикручиваем, сделанные ранее крепежи с подшипниками, заранее установив их строго посередине.

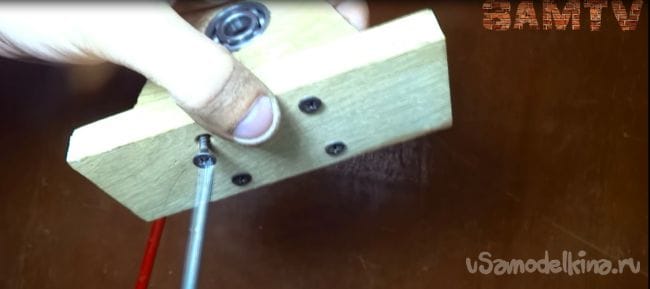
Шаг пятый.
Так как в моем станке я решил применить ременную передачу нужно сделать шкив на переднюю бабку и на сам вал мотора, отношение я взял 1 к 2, чтобы уменьшить количество оборотов, но повысить крутящий момент. Шкив можно сделать при помощи дрели, установив деревяшку в патрон дрели через шпильку и проточить резцом или обычной стамеской.
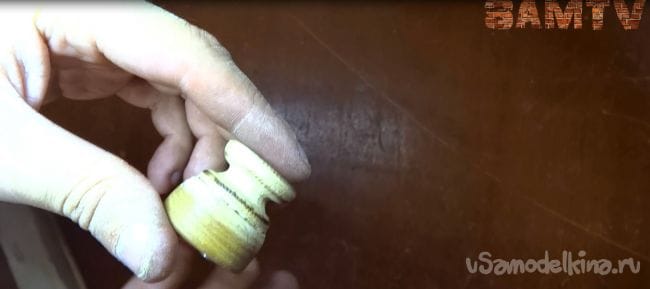
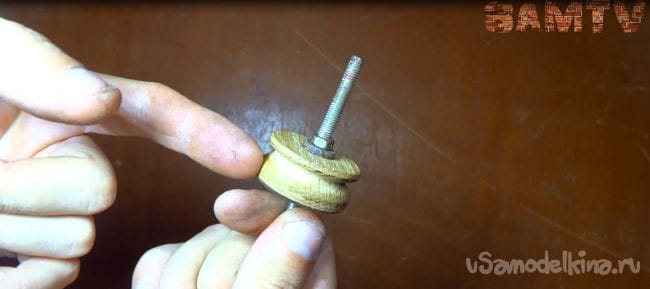
Затем накручиваем на шпильку шкив и устанавливаем в подшипники, через шайбы. Также не забываем смазать подшипники.
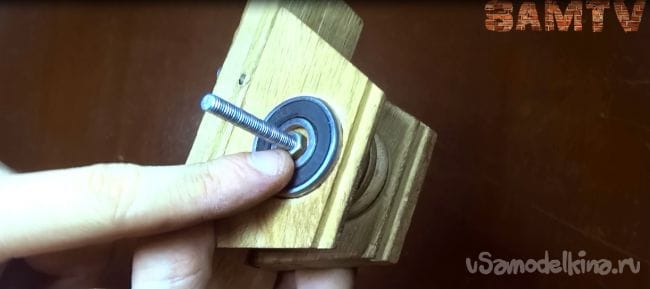

Шаг шестой.
Устанавливаем переднюю бабку и ремень на станину, для этого сверлим отверстия под шурупы и хорошенько все закручиваем.
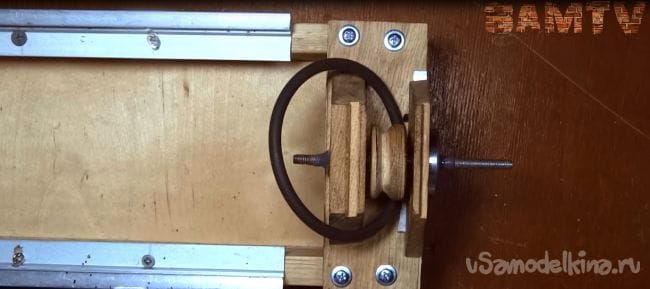
Проверив надежность заднего подшипника я решил, что нужно слегка усилить конструкцию тонкой дощечкой и эпоксидкой.

Шаг седьмой.
Теперь нужно закрепить двигатель, а крепится он будет на специальном креплении, которое я прикрутил при помощи уголка к торцу станины, а также сделал для двигателя подвижную платформу, которая позволит регулировать натяжение ремня, что предотвратит его проскальзывание.
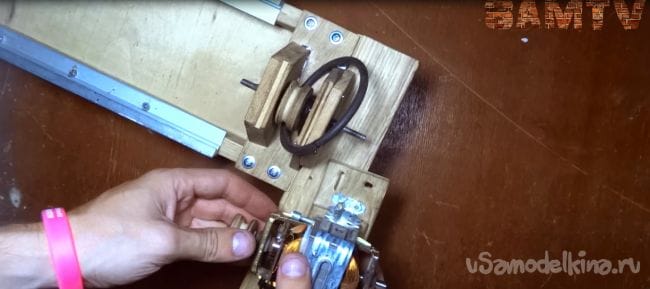
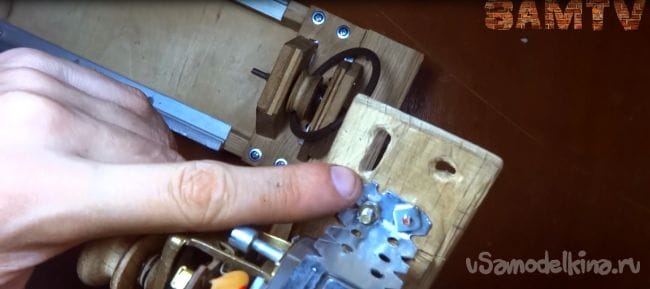
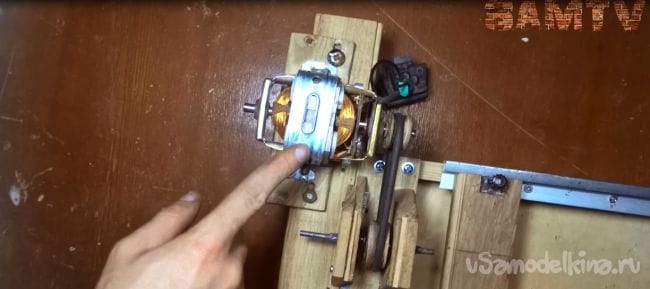
Шаг восьмой.
После того, как двигатель установлен изготавливаем переднюю бабку, которая будет держать заготовку и передавать ей крутящий момент от двигателя. Проще всего это сделать, установив квадрат из паркета на ось передней бабки и обточить стамеской до круглой формы, после чего в трех местах просверлить отверстия и вклеить на эпоксидный клей три штырька, заточенных под конус. После затвердевания можно фиксировать гайкой, подложив шайбочку.
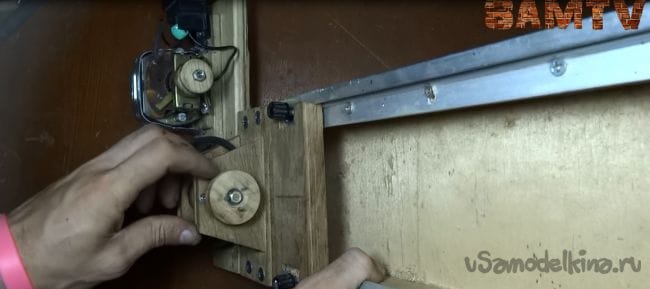
Шаг девятый.
Двигатель у меня от швейной машинки с педалью, которая регулирует обороты, отсюда следует, что он не предназначен для таких нагрузок, поэтому я решил установить вентилятор на вал мотора, чтобы его обмотки не перегревались, думаю такие манипуляции продлят ему жизнь.
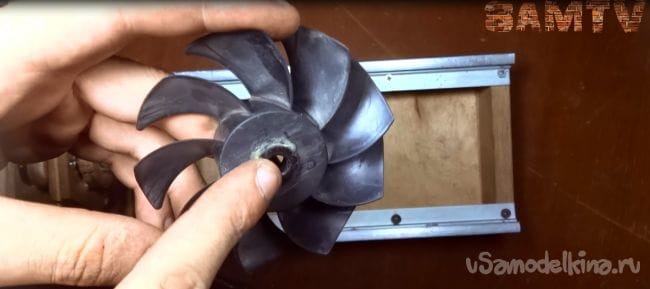
Также не обошлось без доработок, ремень на шкиву во время вытачивания круглой платформы для трезубца проскальзывал, поэтому я приклеил на оба шкива велосипедную камеру при помощи клея «Момент».
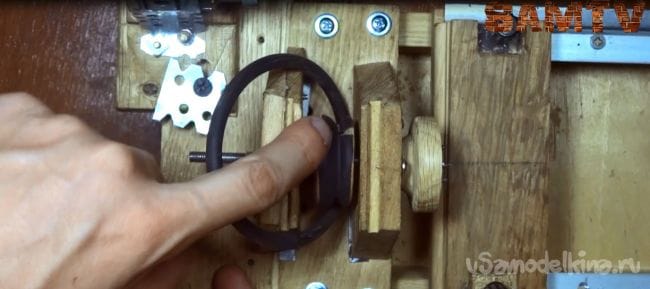
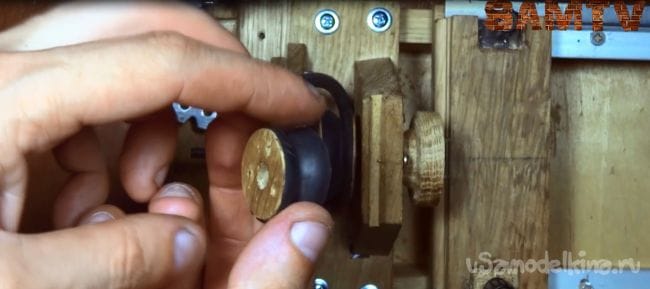
Шаг десятый.
Какой же это станок, если тут нет задней бабки. Исправим это. Задняя бабка собирается из двух паркетин, двух подшипников и оси, которую необходимо заточить под конус. Сажаем ось в два подшипника, после чего их приклеиваем на эпоксидку в канавки на паркетинах, которые будут креплениями задней бабки.
Когда эпоксидка затвердеет при помощи шурупов крепим получившуюся конструкцию к подвижной части с барашками, которую я сделал ранее.
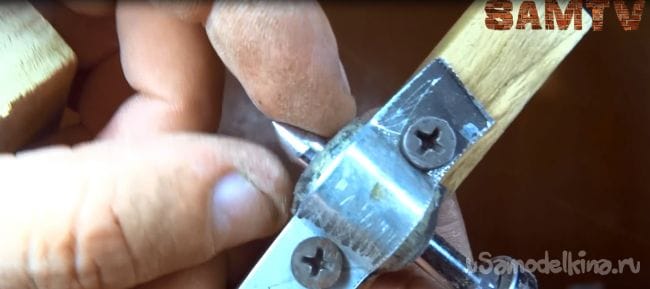
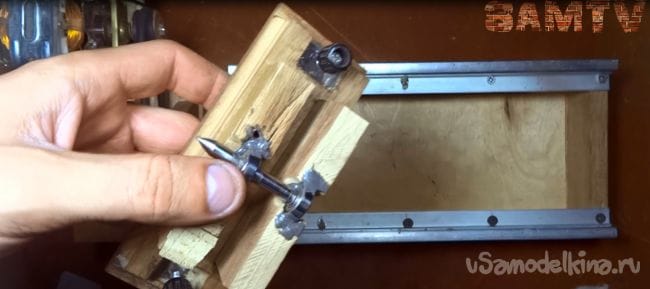
Принцип работы задней бабки прост, по длине заготовки подгоняется задняя бабка и после чего плотно прижимается барашками, что не даст ей самопроизвольно двигаться. Эпоксидку я решил прикрыть сверху крышкой, что сделает конструкцию еще более крепкой.
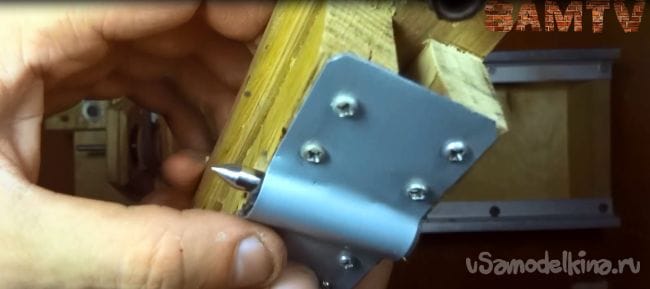
Не забываем проверить сходятся ли центра передней и задней бабок, если да, то все хорошо.
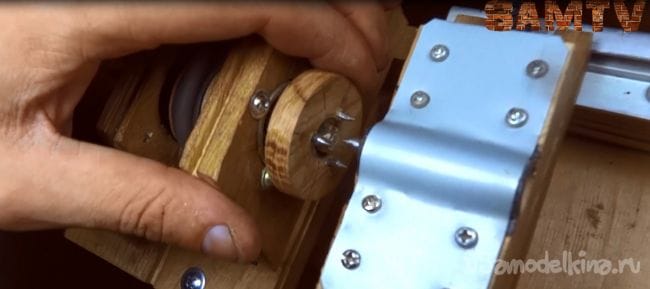
На этом токарный станок по дереву готов, можно смело приступать к деревообработке и вытачивать на станке различные резные самоделки.
Всем спасибо за внимание и всем успехов в самоделках.
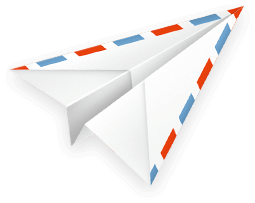
Получайте на почту подборку новых самоделок. Никакого спама, только полезные идеи!
*Заполняя форму вы соглашаетесь на обработку персональных данных
Становитесь автором сайта, публикуйте собственные статьи, описания самоделок с оплатой за текст. Подробнее здесь.Шкив за 15 минут | DIY Life
Февраль 10th, 2013 SamВ этом посте я расскажу, как сделать шкив для 3d-принтера за 15 минут.
Таких шкивов в принтере всего 2 шт — один перемещает стол, второй — печатающую головку.
Для изготовления шкива я использовал холодную сварку — она достаточно простая в обработке,прочная в применении, супер дешевая (30-50 руб). Для информации — родной шкив для ремня стоит от 300 руб и делается на заказ.
Итак, приступим. Все что нам потребуется вы видите на картинке:
набор для изготовления шкива
Слева направо: холодная сварка (любая), масло для смазки формы (любое, хоть сливочное), колпачок от парфюма и кусок зубчатого ремня.
Я думаю, из картинки понятен способ изготовления — мы делаем слепок:
Берем кусок ремня с количеством зубцов 10 шт (количество зубцов не принципиально, но считать шаги двигателя для перемещения стола на 1 мм удобнее именно со шкивом с 10 зубцами).
Далее ищем подходящий цилиндр, что бы этот кусочек ремня целиком и полностью без люфтов поместился в него. Я перепробовал множество колпачков и трубок и нашел нужный экземпляр — видимо мне повезло.
ремень в колпачке от парфюма
Если вам не удастся найти подходящий колпачок — уменьшите или увеличьте количество количество зубцов на ремне.
Другой вариант — выточить такой цилиндр самостоятельно. Берем образец ремня нужной длины, замеряем его длину. По формуле периметр окружности L=2*pi*r, вычисляем радиус и диаметр цилиндра. Вытачиваем его из деревяшки, пенопласта, склеиваем из бумаги или делаем любым другим способом.. Делаем слепок цилиндра при помощи той же самой холодной сварки и получаем свой вариант колпачка от парфюма
Так, ремень у нас помещается внутрь колпачка, но в шкиве должно быть отверстие для оси двигателя. Можно конечно сначала сделать шкив и потом сверлить отверстие, но не факт, что оно будет проходить ровно по центру и ровно по оси вращения. Вышел я из этой ситуации следующим образом — вырезал 2 картонных кружочка диаметром равным диаметру цилиндра, по центру вкрутил в них болт m3 и затянул гайкой, зажал болт в дрель, включил её и напильником довел картонные кружочки до идеально круглых и соосных.
Все приготовления сделаны, приступаем к основной части:
1. Смазываем «колпачок» смазкой, чтобы холодная сварка не прилипла.
2. Вставляем первый картонный круг
3. Вставляем кусок зубчатого ремня (чем ровнее, тем лучше)
4. Наполняем и утрамбовываем в форму холодную сварку (высота заполнения = 2 ширины ремня)
5. Вставляем в форму второй картонный круг
6. Вкручиваем болт так, чтобы он проходил через центры картонных кругов
7. Выравниваем болт (если он болтается)
Через час холодная сварка затвердеет настолько, что готовое изделие можно достать из формы (но я подождал до утра).
Вот, что у меня получилось:
извлекаем готовый шкив
Болт выполняет еще одну очень важную функцию — с его помощью мы и достаем шкив из формы
Аккуратно снимаем ремень:
готовый шкив
Теперь остается немножко доработать его напильником, убрать бумажные круги, рассверлить отверстие под диаметр вала двигателя и использовать в принтере. Одна маленькая хитрость — обязательно посадите этот шкив на вал двигателя на холодную сварку, иначе будете очень долго ловить микро-проскальзывания в виде косяков в геометрии напечатанных деталей, не повторяйте моих ошибок!
Фото обработанного шкива:
обработанный шкив
Шкив на валу двигателя:
шкив на двигателе
Простите за качество — фотоаппарат так и не смог сфокусироваться.
Есть несколько тонкостей при изготовлении такого шкива. После изготовления шкива, протестируйте его, посмотрите, что бы ремень на длине всего хода не приподнимался, не соскальзывал, четко держался на шкиве. Если происходят какие-то аномалии, то лучше изготовить новый шкив. На этом деле надо «набить руку», изготовить хороший шкив и сделать его слепок, чтобы следующий шкив сделать намного быстрее. Вот такой слепок изготовил я:
слепок шкива
Удачи в изготовлении шкива
Точим шкив для поликлиновидного ремня :: АвтоМотоГараж
После того как мы определились с типом ремня и рассчитали конфигурацию обоих шкивов, принимаемся за разработку чертежей.
В качестве заготовок мы будем использовать болванки собственного изготовления. Подробнее об этом можно ознакомиться в разделе Литейка. Две заготовки были специально отлиты для этой задачи. В качестве сырья использовался сорный алюминий и всё хоть немного было похоже на него. В связи с этим в материале присутствуют изъяны, но они никаким образом не повлияют на последующее функционирование станка. Итак, приступим к работе.
Начинаем обработку первой заготовки. Она отливалась в жестяную банку из-под автоэмали. Размеры оказались критическими, и мы её чудом зафиксировали за самые кончики обратных кулачков. Для начала нам нужно проточить заготовку так, чтобы её можно было безопасно установить в токарный патрон. Выставляем скорость вращения шпинделя равной пятьсот оборотов в минуту и включаем станок. Потихоньку торцуем и выводим диаметр заготовки до уверенного зажима кулачками токарного патрона.
Как показала практика, такую процедуру выполнить вполне реально, но не безопасно.
Теперь можно смело отрабатывать заготовку используя большие скорости и подачи. По ходу снятия металла в центре заготовки были обнаружены поры. К ним мы были готовы. Они являются следствием того, что при отливке заготовки применялось всё, хоть как-то отдалённо напоминало металл из семейства алюминиевых.
Получилось так, что сердцевина заготовки с большим количеством пор, следовательно, есть вероятность, что посадочное место под вал может со временем разбить. Чтобы исключить эту вероятность мы в центр шкива при помощи гидравлического пресса установим стальной цилиндр диаметром 30 миллиметров. В качестве материала для центральных вставок мы используем ролики от тормозного механизма ЗИЛа 130. Этот момент обозначен на проектном эскизе выше.
Приступаем к обработке роликов. Данные детали достаточно специфичны они состоят они двух элементов, большого закаленного кольца и вала. Так как на деталях присутствует ржавчина и окалина, то перед обработкой сперва проточим базу с одной из сторон. Это необходимо для хорошей фиксации ролика в патроне, так как в дальнейшем планируем обрабатывать больной закаленный цилиндр.
С одной из сторон валы проточены, а с другой срезаны.
Далее протачиваем внешний диаметр и торец.
Теперь также, как и с противоположной стороны срезаем малые валы. После протачиваем торец.
Весь материал для изготовления шкивов подготовлен.
Устанавливаем первую заготовку в токарный станок и начинаем растачивать центр.
Отверстие под посадку цилиндра готово. Следующей операцией мы запрессуем металлический цилиндр в заготовку.
После запрессовки, заготовку снова устанавливаем в токарный патрон и начинаем растачивать отверстие для вала электродвигателя. С этого момента все токарные работы, которые могут повлиять на соосность и биение шкива необходимо выполнить за одну установку.
То есть проточить ручьи для шкивов и расточить отверстие под вал нужно без демонтажа заготовки из токарного патрона. В противоположном случае осевого биения шкива не избежать. Сперва, высверлим отверстие.
Чистовую обработку выполним расточным резцом.
Отверстие под посадку вала электродвигателя готово.
Теперь создаём форму шкива.
Канавки или как их ещё называют ручьи будем протачивать при помощи резьбового резца LW1215R-06. Для этой операции он подходит как нельзя лучше.
Первая половина шкива готова. По аналогии с ней протачиваем ручьи второй половины шкива.
Только после того как полностью проточены обе части шкива и расточено отверстие под вал, можно демонтировать заготовку из токарного патрона. Далее её аккуратно зажимаем за малый шкив и обрабатываем обратную сторону.
Вот уже вырисовываются очертания полноценного шкива.
Шкив полностью готов.
Единственно, выявилась одна неприятность, отверстие проточено под вал электродвигателя, а внешние диаметры шкивов для передней бабки. Придётся повторить тоже самое только соблюдая соответствия диаметра шкива и посадочного отверстия.
Выточили полтора шкива, а стружки уже целая гора.
Обе ступени шкива полностью готовы. Приступаем к операции отрезания.
Также как и в предыдущем случае, с обратной стороны доводим шкив до совершенства.
Сделан первый правильный шкив.
К этому времени мы рассчитали и приобрели нужный приводной ремень. Об этом напишем в следующей статье. А пока приготовим очередную заготовку для второго шкива.
Проделываем аналогичные операции описанные выше. Хочу обратить внимание на заготовку. Она отливалась для изготовления проставки к гидравлическому прессу. При её отливке в основном использовался алюминиевый профиль и ему подобные детали. В том числе там был и силумин. В связи с чем проявился интересный эффект. Я его назвал «Звёздное небо». Он заключается, в рассредоточении относительно мелких пор по всему объёму заготовки. Этот эффект также, никоем образом, не будет влиять на работу механизма.
Профиль второго шкива изготовлен, теперь можно отрезать.
Завершены работы и по второму шкиву.
Из-за конфигурации резца LW1215R-06, ручьи под ремень на этом шкиве пришлось выполнять при помощи другого резьбового резца с державкой 8×8 миллиметров. Вылет от края резцедержателя, до режущего кончика был двадцать миллиметров, в связи с этим, в ручьях можно наблюдать некую ребристость. Она является следствием недостаточной жёсткости маленьких резцов.
По завершении изготовления второго шкива, был собран и электродвигатель.
Подробнее про сборку силового агрегата читайте в статье: Новый электродвигатель станка СТД 120 — переборка, покраска.
Дополнительная информация по шкивам:
Мы начали первые экспиременты и уже подготовили первую часть материала: Тест ремённого привода. Поликлиновидный ремень. Так же выпустили обучающий короткометражный видеофильм.
Расчёт диаметров шкивов ремённой передачи для поликлиновидного ремня. Онлайн калькулятор.
Расчёт диаметров шкивов ремённой передачи с использованием клиновидного ремня. Онлайн калькулятор.
Расчёт диаметров шкивов ремённой передачи с применение плоского ведомого шкива. Онлайн калькулятор.
Расчёт длинны приводного поликлиновидного ремня. Онлайн калькулятор.
Расчёт длинны приводного клиновидного ремня. Онлайн калькулятор.
Расчёт и подбор натяжного ролика для поликлиновидного ремня
Расчёт и подбор натяжного ролика для клиновидного ремня
Точим шкив для поликлиновидного ремня
Тест ремённого привода. Поликлиновидный ремень. Первая передача.
Онлайн калькуляторы на все случаи жизни, рекомендуем ознакомиться:
Расчёт количества масла для бензина,
Расчёт масла для топливной смеси — ёмкость без маркировки объёма,
Расчёт шунтирующего сопротивления амперметра,
Онлайн калькулятор — закон Ома (ток, напряжение, сопротивление) + Мощность,
Расчет трансформатора с тороидальным магнитопроводом,
Расчет трансформатора с броневым магнитопроводом.